.
5.06.2015
Wir berichteten schon vor drei Jahren über das kleine aber feine Raumfahrtunternehmen Cobenhagen Suborbitals in Dänemark ( http://www.hjkc.de/_blog/2012/07/28/raumfahrt---erfolgreicher-start-von-daenemark-smaragd-1-rakete/), welches sich nun durch viele Raketentriebwerk-Tests auf sich aufmerksam macht:
.
Bad weather has forced us to move the test to Sunday (May 31st)
Dear readers
Just a small update on the progress during the last week. More details on the upcoming test further down in this text.
GO for testing!
I am happy to announce that we are still ready for testing on Sunday – first burn will be at 13.30 CEST.
The doors will open to the test range at 12.30 CEST, and the crowd area will just like the last time be here.
We urge you to book your tickets in advance. The tickets costs 50 kroner. Kids and supporters have free access. Read more at the ticket service.
Nexø design
There’s great progress in this area: the jet vane servo system has been designed and the internal piping is almost complete. Hopefully there should be no more than a couple of working days left for the design to ready enough for the components to be ordered.
.
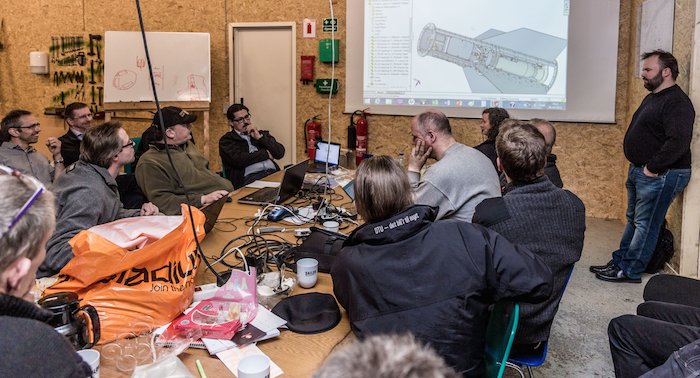
All departments have been sworn in with regards to the total weight budget, and we are currently within 1 kg of our requirements. Maybe it’s time to re-introduce the lead coated main parachute? :-)
BPM-5 Static test
As written above, things are progressing as planned towards this weekends test. The injector, with serial number 002 has been readied for the test, and we are eagerly looking forward the characterise its behaviour.
.
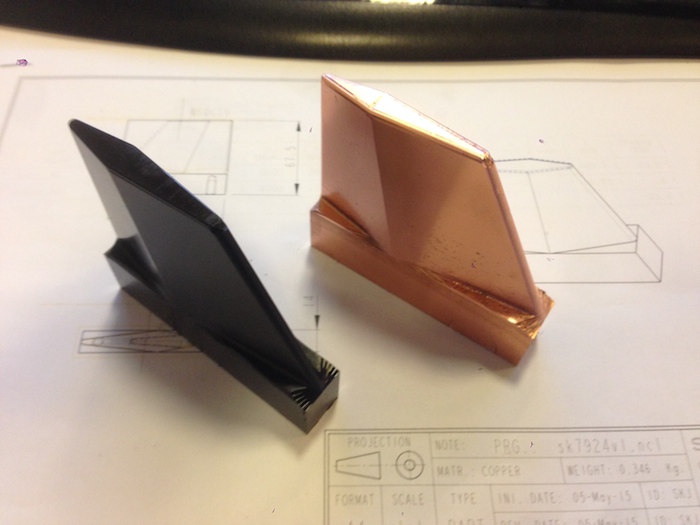
The copper vane to the right, next to a plastic- graphite look-a-like. Photo: Flemming Rasmussen
Flemming Rasmussen working on the graphite jet vane and he has proudly sent us this picture:
.
The graphite jet vane is ready for some beating on Saturday. Foto: Flemming Rasmussen
The graphite jet vane is ready for some beating on Saturday. Foto: Flemming Rasmussen
The purpose of literally putting the the two jet vanes into the fire is to test their durability, and measure the temperatures they reach during a burn. We will also measure their weight before and after the test, to measure how much the fire has corroded them.
What will be tested on Sunday
The planning has come to a point where we can present to you the wish list below.
Commissioning of the new injector (sn. 002) with larger LOX channels than injector 001. 7 sec burn
Commissioning of automated pre-to-main stage transition. 2-3 runs of 7 seconds at different prestage angles of the main valve.
Trimming the operation point to a chamber pressure at 15 bar. 2-3 runs of seven seconds.
Injector mode characterization. 1 run at > 20 sec blow-down burn with the starting chamber pressure of 15 bar.
DPR–based automated pressurization (the function we will make use of on the Nexø 1). 1-2 runs of 7 seconds. (DPR omay not be ready for Saturday, but we are struggling to reach it)
So we are looking at up to 10 burns!
Do notice that this is a wish list. Lack of time, engine breakdown or other unforeseen events can change the number. But there’s nothing wrong with our ambitions.
production of Ballute sn-002
The parts for the next ballute have been laser cut, and assembly will now commence.
.
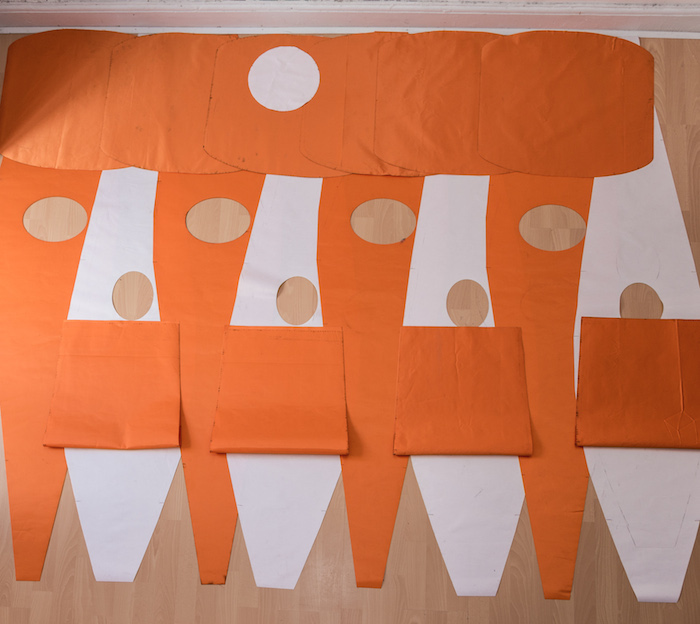
The parts for the next ballute are ready, and all that is left is a bit of sewing. Photo: Mads Stenfatt
---
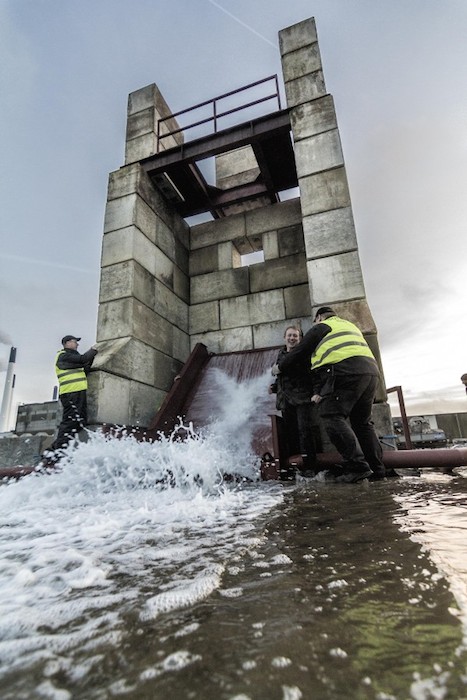
VTC3 water sound suppression system being tested
.
This is the Vertical Test Cell three – better known as VTC-3.
VTC-3 is a 160 ton steel and concrete structure. It consists of 60 large 2,5 ton concrete blocks. These make up the flame bucket and fragment containment. Inside the massive structure we find the flame deflector. Its job is to divert the hundreds of cubic meters of exhaust gasses that are generated each second during a main stage test of the HEAT 1600 single TM260 rocket engine. The flame deflector is water cooled. Two diesel engine powered centrifugal pumps supply cooling water at a rate of 20 ton pr. minute – to prevent the structure from melting. The flame deflector is cooled by a waterfall on the front and by dual “showerheads” on the back side. The cooling water enters the test stand via two six inch pipelines. To control the coolant flow, two remotely operated six inch butterfly valves are installed in the pipelines.
The big test stand sits on the grounds of a derelict shipyard. Its 55.000 cubic meter large drydock basin is used for cooling water. It also prevents fire from spreading in the southern direction. To the north, a ten meter pile of gravel contains the test stand area. To the east we find the sea, and to the vest we have a large open space, with the command post placed 300 meters away. The VTC-3 is designed to contain any imaginable test anomaly.
Above the flame pit a steel girder bridge made of IPE 400 profiles holds the booster. The steel structure has all the same hold down positions as the launch pad, and indeed – VTC-3 could act as a HEAT 1600 launch complex if it was not for the lack of frangible nuts in the hold down system. The HEAT 1600 booster is held down by four 40 mm bolts. They lock it to the IPE 400 profiles via four 30 mm thick triangular steel plates.
In the event of a serious engine mishap, the tank structure may be damaged. To contain this, it is held down by four additional hardpoints mounted on the intertank, just below the LOX tank.
VTC-3 is not an engine test stand – instead it’s designed to test entire flight stages. All the umbilicals and support systems mimic the ones on the launch pad, so the tests are also verification of the functionality of the ground support systems. One difference is, however, that the VTC-3 does not have a service / umbilical tower like Sputnik. We can do this because, unlike flights, we don’t have either spacecrafts or potential upper stages during a static test.
VTC-3 can accommodate other rocket stages, and other types of rocket engines than the HEAT 1600. This is done using a number of adapters that make smaller rockets like the HEAT 2X fit the test stand. The very powerful solid fuel launch escape system motor will also be testfired on this site. In fact, the very first test ever conducted at the VTC-3 site was a solid propellant miniature launch escape system test motor.
It has been decided that the maximum allowable propellant load on the VTC -3 will be 2000 kg. This makes it possible to conduct full duration static test on HEAT 2X, but for HEAT 1600 it will give us a maximum test duration of sixteen seconds. The HEAT 2X and HEAT 1600 rocket motors are basically the same design except for the size, making it easier to accept this limitation.
During tests, the entire area around the test stand is covered by water from the cooling system. In the event of a fuel (alcohol) spill, the alcohol will be dissolved and not be able to ignite.
Together with the construction facilities in HAB2, the VTC-3 is the most important land based Copenhagen Suborbitals structures.
Our Test facility
HEAT 1600 – Copenhagen Suborbitals big liquid fueled booster – is destined to become the most powerful amateur rocket ever devised. At 260 kN, its thrust will exceed that of the V2 missile or the X-15 space plane.
Let’s get the numbers right here…
Amateur rocketry uses a letter classification of motor size. It starts with A motors at 2,5 newton seconds. However, amateurs practically do fly larger M, N end O size motors at up to 40 thousand newton seconds. This numbers was exceeded by the total impulse of the HEAT 1X back in 2011. In its 16 second powered phase of its flight it produced some 75 thousand newton seconds. It lifted off with potential for 135 thousand newton second, but the engine had to be shut down during flight due to a trajectory anomaly.
By 2012, the flight of the two stage Smaragd marked the end of the phase with passive stable rockets in CS.
By 2013 we had successfully flown Sapphire with active guidance, and we are now aiming for the flight of the 260 thousand newton seconds HEAT 2X. This pressure feed ten meter by 65 cm diameter rocket is scheduled for lift off in mid 2014
However, the HEAT 1600 under construction takes this to a whole new level. Its total impulse during flight will be an unbelievable 26 million newton seconds.
To conduct flight qualification of this massive turbo pump feed liquid propellant propulsion system – a test stand on a similar scale is needed.
.
Our Launch sites
Virtually all space companies launch their rockets from land based launch pads, as, from obvious reasons, land based infrastructure has the big advantage of easy accessibility. The launch of rockets – be it small or huge – demand a lot of surrounding space, and typically a large area has to be cleared of people prior to launch. This restricts rocket launch sites (spaceports) to military or otherwise controlled or uninhabited areas.
Very few spaceports are located in Northern Europe, as most areas are densely populated. We have considered established spaceports like Andøya Rocket Range in Norway, or Esrange in Sweden, but they are both very remote from our facilities in Copenhagen, and Esrange do not accommodate non-flight proven hardware.
In Denmark, the land based military controlled shooting ranges are far too small to fit our needs, though they are often used by amateur rocket clubs, launching sounding rockets to 1-4 km altitude.
This leaves Copenhagen Suborbitals with only one remaining realistic option – sea launch!
.
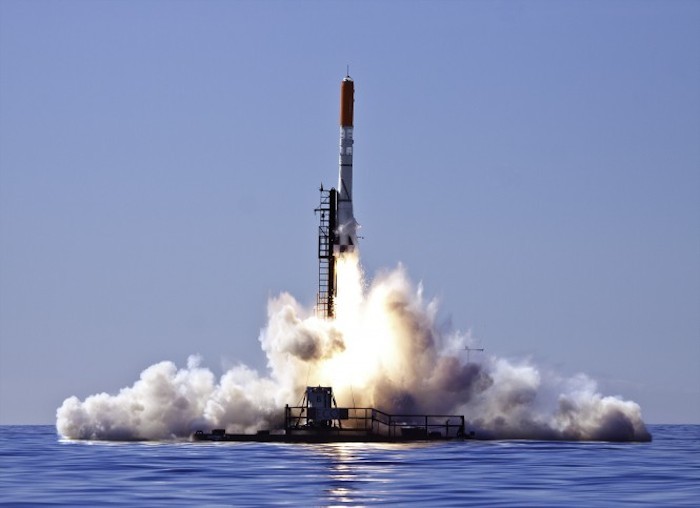
Sea launch
Though burdened with logistical impracticalities, sea launch also offers many advantages. Outside the national territorial waters – typically 12 nautical miles off the coast – things, as an example, get a lot simpler from a legal perspective.
Few landmasses on the planet are as empty as the open sea – and as easy to monitor. This makes the whole issue of range safety relatively simple compared to the conditions on land. For the same reason, most spaceports are located on a coastline. Finally – operating out of Copenhagen, Denmark – the logistic challenge of launching rockets from Sahara or some place in the Arctic is much larger than sailing a couple of hundred nautical miles out to sea.
.
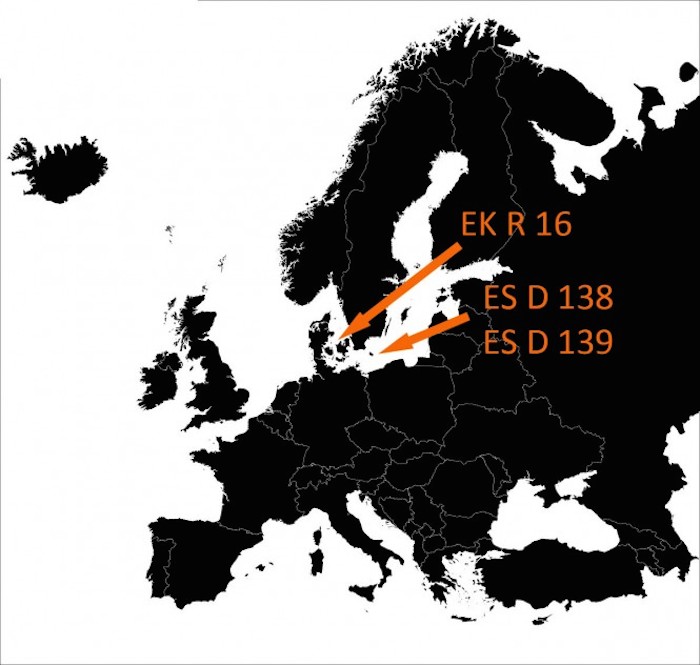
The positions of our launch sites ESD138, ESD139 and EK R 16
-
As a result, in 2009, we decided to commit Copenhagen Suborbitals to sea launch.
ES D 138/139
Our primary launch area is the military firing practice areas ES D 138/ES D 139 in the Baltic Sea, east of Bornholm, Denmark. The combined area is approximate 70×35 km.
These areas are provided to us by the Admiral Danish Fleet for a specific time period (launch window), and with help from the Danish and Swedish authorities, the airspace above is closed for any traffic in the hours of the actual launch.
During launch campaigns, we operate from the town of Nexøe on the eastern coast of Bornholm, and the site is now known as Spaceport Nexøe.
To help us clear the area of fishermen and other vessels, we get help from the local Marine National Guard on Bornholm, typically by means of the MHV 903 Hjortø, which until the acquisition of our command ship Vostok, served as launch control center.
EK R 16
Though suitable for high altitude launches, operations from Spaceport Nexøe involves a lot of logistics and expenses. For minor launch operations, such as LES tests and 1/3 scale TDS launches, a better alternative is the EK R 16 shooting range in the bay of Sejerø, on the western coast of Sealand in Denmark. This area is only 100 km from our facilities in Copenhagen, and the area is approximate 6×14 km.
We have yet to try this area out, and as opposed to the remote offshore shooting ranges in the Baltic Sea, the EK R 16 area enables a direct sight possibility for spectators at the shore.
NEWSLETTER
Email address:
LATEST NEWS
27.05.2015
There will be MANY rocket engine tests on Sunday!NOTICE: Bad weather has forced us to move the test to Sunday (May 31st) Dear readers Just a small update…
21.05.2015
When streaming failsDear readers, We have previously promised to describe what caused our streaming from the BPM2 test weekend on the 2nd…
19.05.2015
Next BPM-5 rocket engine test: Sunday May 31NOTICE: madtruck.dk will be selling delicious burgers and fries at the event. We love the smell of rocket fuel in…
07.05.2015
42!Dear readers Sunday was one of those days where you really have to try hard to find something to complain…
06.05.2015
May 10th we’ll test fire a BPM-5 rocket engine for the first time.Sunday May 10th we'll test fire a BPM-5 rocket engine for the first time. This is the engine type that will fly…
23.04.2015
Come and see us test rocket enginesOn Saturday May 2nd we'll testfire several rocket engines. The viewing area is open from 12.00. The plan is to…
-
Quelle: Copenhagen Suborbitals
.
Update: 23.07.2015
.
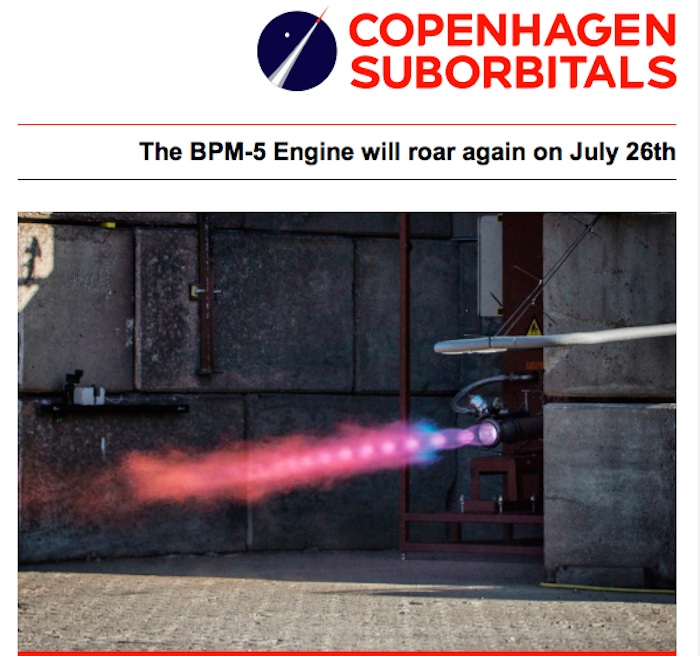
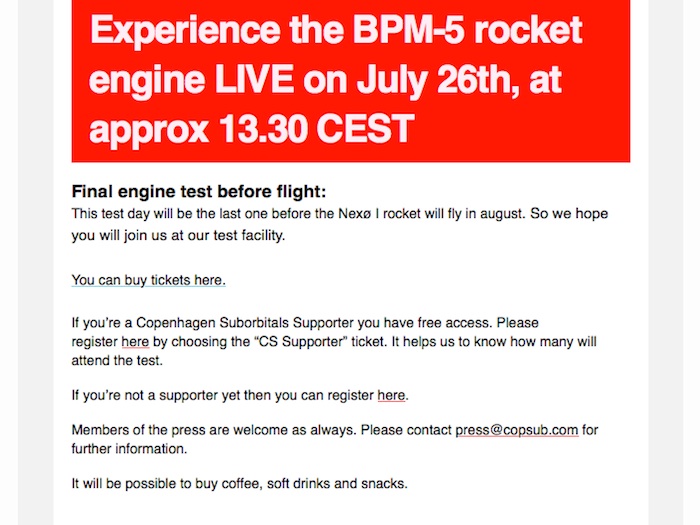
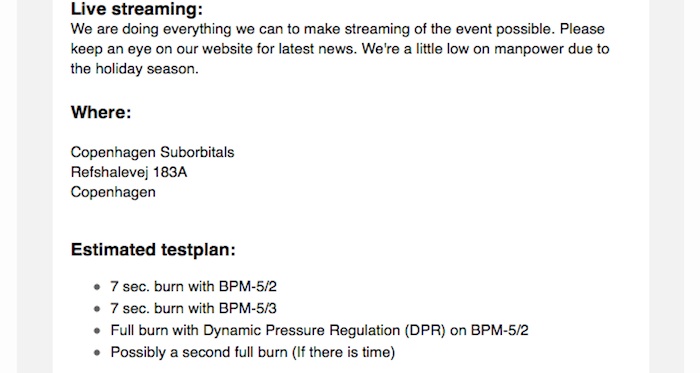
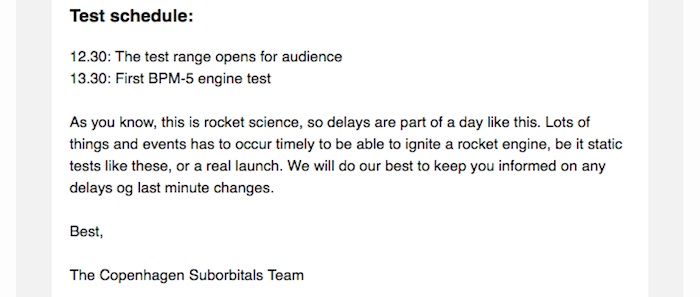
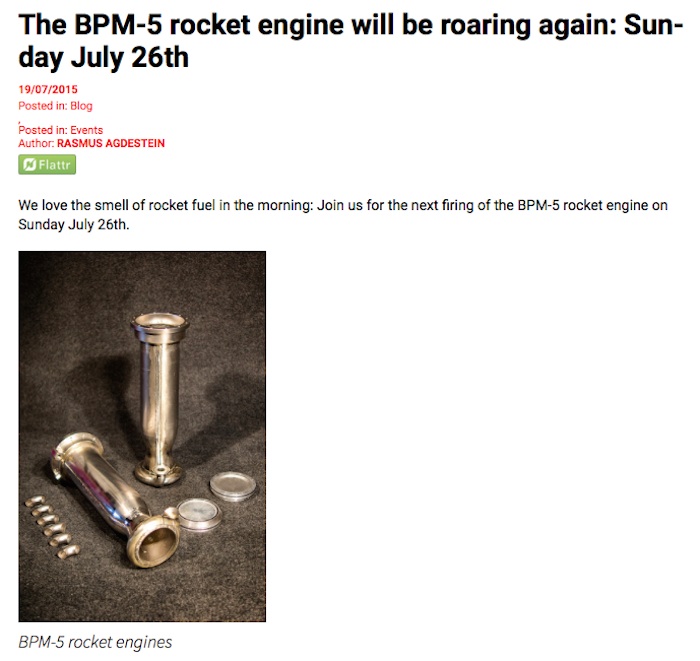
Quelle: Copenhagen Suborbitals
-
Update: 1.08.2015
.
Tonight at 18:00 CEST:
The final roar of the BPM-5 engine before flight |
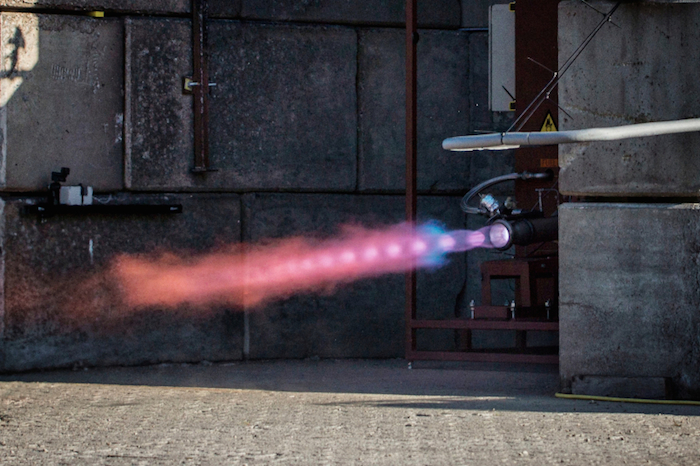
Final roar before the launch of Nexø I. Watch it online.
Final engine test before flight:
This evening at from approx 18:00 CEST we will perform the final tests of the BPM-5 engine before flight.
Due to the urgency of these test and reduced manpower there will not be public access.
Live streaming:
We will stream via youtube here:
https://www.youtube.com/watch?v=crffeP7u2rc
Estimated testplan:
A short qualification burn with the BPM-5/3 (Flight engine)
Two long burns with the BPM-5/2
As you know, this is rocket science, so delays are part of a day like this. Lots of things and events has to occur timely to be able to ignite a rocket engine, be it static tests like these, or a real launch. We will do our best to keep you informed on any delays og last minute changes.
Quelle: The Copenhagen Suborbitals Team
.
Update: 7.08.2015
.
Rocket launch coming up!
We have booked the last two weekends of August (2015) and the first two weekends of September as our launch window for the Nexø I rocket. Once ready, and the weather forecast is okay, we'll launch. Typically we launch early in the day, CEST, and our activity will be broadcast live on our youtube channel
Quelle: The Copenhagen Suborbitals Team
-
Update: 9.09.2015
.
Launch postponed until September 19th-20th:
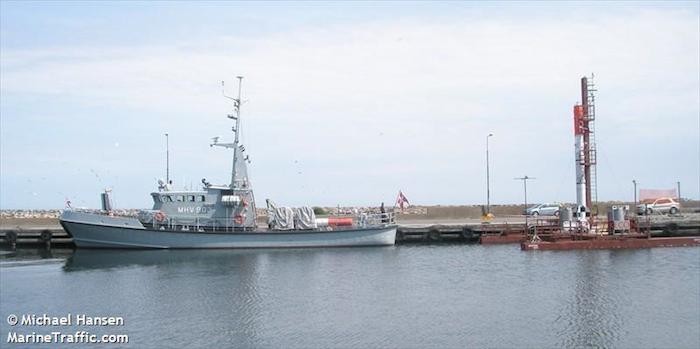
Unfortunately, the weather forecast for this weekend is looking quite bad, so we won't be able to launch the rocket as planned. We've extended our launch window and are hoping for better weather on September 19th-20th.
The weather forecast for sailing our launch platform Sputnik to Spaceport Nexø is looking quite good over the next couple of days. Sputnik embarked towards Spaceport Nexø on the island of Bornholm this morning!
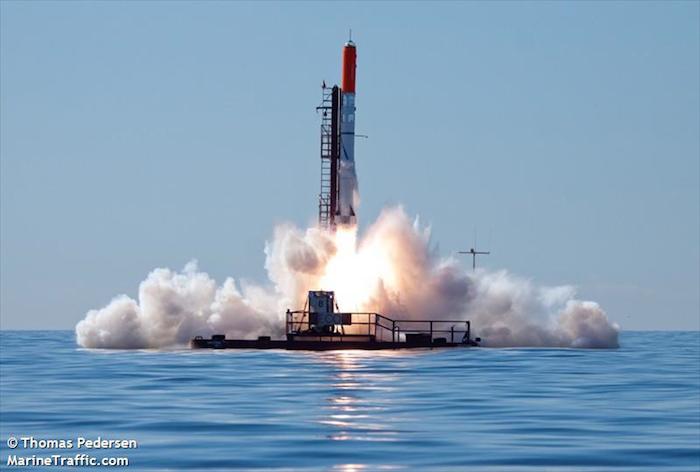
Quelle: The Copenhagen Suborbitals Team
.
Update: 20.09.2015
.
Nexø I launch attempt postponed to September 26th - 27th.
Even through the weather is getting better at Spaceport Nexø there will not be a launch this weekend. We have had a visit from good old Murphy. Some of the checkout tests needed before the rocket can be flight qualified has taken longer than expected.
This weekend we will perform the final tests and after that the engine section will be disassembled for LOX cleaning, reassembled and final checkout procedures performed. We aim for launch the weekend 26th -27th of september. The long term weather prognoses look promising!
Quelle: The Copenhagen Suborbitals Team
5470 Views