.
NASA dreams of future Morpheus project templates
NASA’s Morpheus team have completed a review of its operations, following the conclusion of its test program. This week’s overview – which also hinted at the possibility of a new lander vehicle – provided a glowing review of a project that conducted 63 test flights and only cost $14 million over four years, in turn creating a roadmap for future “lean” programs within NASA.
Project Morpheus:
The system was manufactured and assembled at the Johnson Space Center (JSC) in association with Armadillo Aerospace – with its heritage based on Armadillo’s Pixel system.
The project ran from its conception in the summer of 2010, through to its final test flight in December of 2014.
Morpheus was designed to be large enough to carry 1,100 pounds of cargo to the moon – ranging from a humanoid robot, a small rover, or a small laboratory to convert moon dust into oxygen – performing all propellant burns after the trans lunar injection.
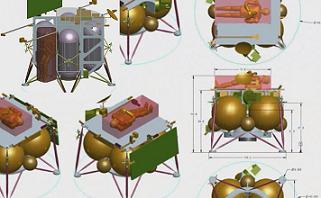
In its early days, it was heavily associated with a project to send a version of the Robonaut – not unlike the one currently residing on the International Space Station (ISS) – to the Moon. This was known as Project M (documentation available in L2).
This notional mission would see the robot and lander launched from KSC on a commercial expendable launch vehicle and inserted into a trans-lunar trajectory.
Once at the moon, the spacecraft would be inserted into a low lunar orbit where it would orbit until ready to perform the entry, descent, and landing (EDL).
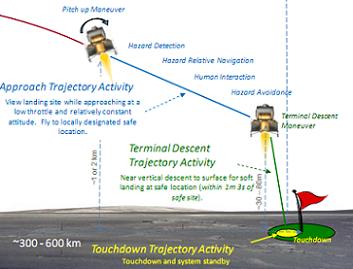
The project focused on vertical test bed demonstrations with green propellant propulsion systems and autonomous landing and hazard detection technology.
The development of Morpheus also allowed prototype lander engineers to integrate technologies for future spacecraft that could land on a variety of destinations in our solar system.
Per the project’s review on March 12 (full notes in L2), spin off and patents are now being worked on to build on the heritage of Morpheus testing.
The first vehicle, Morpheus 1.0, was strictly a non-free flight test vehicle that flew under a tether system attached to a crane at JSC in Houston.
Those tests evaluated the system’s LOX-Methane propulsion, which was utilized on both the 5,400 pound thrust main engine and the Reaction Control System/Roll Control thrusters.
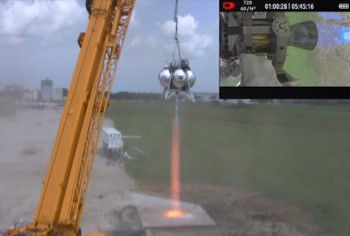
The main engine – which was also tested at the Stennis Space Center – could throttle at a ratio of 4 to 1, ranging between 1,400 and 5,400 pounds thrust. All Morpheus engines were custom designed and built specifically for Morpheus and only cost $60,000 each.
The test program provided many interesting data points, from dealing with combustion stability – which was classed as a major issue during the engine development and Morpheus 1.0’s testing – through to using the main engine and the roll thrusters, supplied by propellants from the same fuel tankage – something that had never been done before with a LOX-Methane set up.
There were a total of 24 tests at JSC of both Morpheus 1.0 and the follow on 1.5A, before Morpheus 1.5A was shipped for testing at the Kennedy Space Center (KSC) in 2012.
Morpheus was staged at the Shuttle Landing Facility (SLF) at KSC, ahead of attempting its first free flight over a specially constructed hazard field of craters and rocks at the end of the runway.
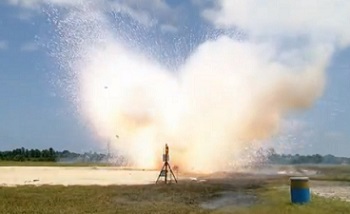
However, the test – conducted in August of last year – did not go to plan, as the vehicle’s Thrust Vector Control (TVC) system suffer a major malfunction, sending it into a roll, prior to crashing into the ground.
“At T plus 0.6 seconds, Morpheus lost its guidance, the engine remained locked into its last commanded position, and the vehicle executed a half loop into the ground, quickly catching fire and was largely consumed in the resulting propellants feed fire,” added notes from the review.
Although SLF fire crews were on hand, the pressurized system could not be approached as it laid crippled on the site. Eventually, the fire breached the pressurized fuel tanks, resulting in it exploding. The review noted that remains will go on display at the Smithsonian this Summer.
The failure was attributed to a connector failure, caused by Vibro-Acoustic induced vibrations at engine ignition, the review notes added.
Morpheus 1.5A used commercial connectors, while the follow on Morpheus 1.5B strictly used Mil-Spec connectors for everything. The off the shelf commercial grade connectors were replaced with Mil-Spec Aerospace grade connectors.
As with a large amount of test programs, a failure was an expected and acceptable risk, as such as there was no formal Failure Review.
The Morpheus team, then combined with the Autonomous Landing Hazard Avoidance Technology (ALHAT) team members, were then directed to build the next Morpheus vehicle, ahead of a return to static hot fire and dynamic tethered flight tests at JSC in early 2013.
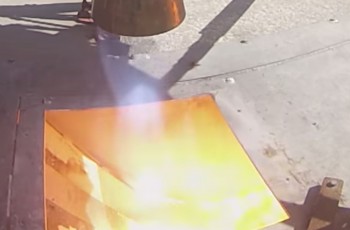
Morpheus 1.5B was quickly built as a replacement test vehicle with over 70 upgrades, while a flame trench was added – by the KSC Swamp Works – to the launch area to reduce the Vibro-Acoustic loads on the test vehicle at engine ignition.
During testing at JSC, the lander’s engine was successfully ignited six times in a row, with each burn lasting 600 milliseconds. This period of testing was classed as challenging, resulting in the test schedule for a return to KSC to be delayed several times.
The ALHAT guidance system was eventually installed on Morpheus ahead of its big tests at the SLF.
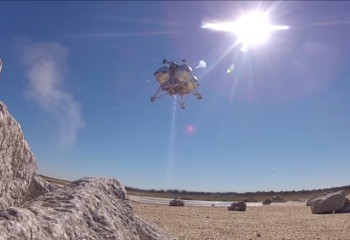
Its return to Florida was a huge success, with incremental increases in the challenges for the vehicle, resulting in numerous hops over the hazard field, prior to smooth touchdowns on the target pad.
The final test was conducted in December, with a 97 second flight resulting in the lander climbing to 800 feet, flying forward 1,300 feet – scanning its simulated lunar landscape below – before safely landing.
This marked the conclusion of testing for Morpheus.
Looking back on the program achievements, Project Manager Jon Olansen continued the March 21 overview by noting not just the successes enjoyed by the vehicle, but also the lessons learned from how the “lean project” was run.
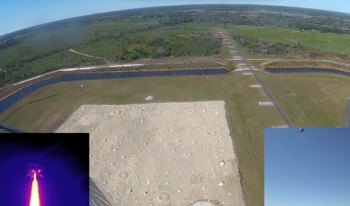
The overview noted the entire program management and record keeping was conducted on line, with only six Formal Documents generated during the entire program’s life. This is a notable change from how NASA normally runs a program – which is usually “paper heavy” on the documentation side.
The total program cost was relatively cheap by NASA standards, costing only $14 million in Materials and Labor over its 4.5 years – with an average of just 40 people working the project at any one time.
The project was also run from a “fail forward” mindset, doing away with the risk adverse nature that is embedded into modern day aerospace programs.
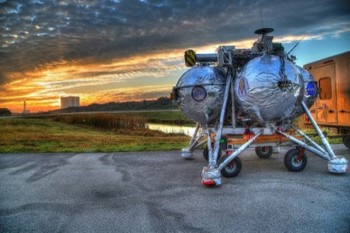
The vehicle was completely “Single String Failure”, meaning it was built without backups or redundancy.
“You must be willing to take risks, and your management has to fully understand you are willing to take the risks,” as was outlined at the overview, with an “assume it will fail every time” approach taken and accepted as meeting the Range Safety requirements.
It was also added that the team was made to feel more involved with the vehicle, with individual team members taking ownership of his/her part of the vehicle, and had total authority over that part of the vehicle, without the “Mother may I?” approach.
Costs were kept low by utilizing the “MSC-Granger-Home Depot supply chain” when ever and where ever possible, with this “Beg and Borrow” approach classed as saving the project at least $50 million.
As to the future, the overview concluded by noting another Morpheus could be possible, if funding was appropriated.
For the meantime, the data from the testing is being fed into spin offs and patents.
(Images: Via NASA and L2)
Quelle: NASA
4736 Views