Amy Buck, SLS core stage insight lead at NASA's Marshall Space Flight Center in Huntsville, Alabama, holds up a sample of foam that recently went through testing in Marshall's Hot Gas Facility. The facility is used for development and qualification of material systems for use on launch vehicles, like NASA's Space Launch System. These foam panels were tested to determine recession characteristics of the foam during the ascent phase of flight. The surface of the foam reaches more than 500 degrees Fahrenheit as it undergoes a hot gas flow at speeds of up to Mach 4 to simulate the environment during launch. NASA engineers then take the samples and measure how much foam is lost during the test to characterize the materials for use in the launch vehicle design and analysis.
Credits: NASA/MSFC/Emmett Given
You may not think about insulation much, but it's one of those unsung industry heroes that keeps our drinks cold and homes warm on those bone-chilling winter days. Insulation also is a key component to protecting NASA's Space Launch Systemand its super-cold fuels for the journey to Mars.
Different types of cryogenic foam – used for very low temperatures -- will insulate the rocket's core stage and launch vehicle stage adapter, which connects the core stage to the interim cryogenic propulsion stage (ICPS). The core stage is the backbone of the rocket, and houses the avionics system, propellant and RS-25 engines. On the first flight of SLS with the Orion spacecraft, called Exploration Mission-1, the ICPS will give the Orion the big push needed to fly beyond the moon before the spacecraft returns to Earth.
The rocket's fuel is comprised of liquid hydrogen and liquid oxygen. Liquid hydrogen is cooled to -423 degrees Fahrenheit, and the liquid oxygen is cooled to -297 degrees Fahrenheit. Insulation protects the outside of the core stage from ice build-up resulting from the subzero propellants inside the aluminum walls. Insulation also reduces heat flow to the propellants, hardware and flight systems during launch and atmospheric re-entry.
So, what kind of insulation materials can measure up for the world's most powerful rocket? Engineers at NASA's Marshall Space Flight Center in Huntsville, Alabama, are peeling back the layers to find out.
"NASA has developed new, more environmentally friendly insulation materials for future launch vehicles," said Michael Frazier, nonmetallic materials branch chief at the Marshall Center. "The cryoinsulation materials for SLS are not only more environmentally compliant, but they are also just as efficient and lightweight as the previous generation of materials."
Three types of foam have been developed and are being tested for SLS. The foams are all closed-cell materials, which means they are stronger and have greater resistance to heat flow and moisture. They also are non-ozone-depleting and flame resistant.
The different types of insulation are applied by varying methods: automatically by a robot; manually using a hand-held spray system; and hand mixed for pouring into molds. "With some parts of the rocket being so massive, like the core stage, robotic applications help reduce time and manpower with more control and continuous sprays," said Amy Buck, SLS core stage insight lead. The thickness of the insulation varies depending on the hardware, but it is typically about one inch.
Hundreds of 24-by-24-inch panels have been covered with the three types of foam for a variety of tests, which are being conducted by NASA and prime contractor Boeing, headquartered in Chicago, to qualify the insulation for the challenging environments SLS will experience before and during flight. Tests range from density measurements to exposing the foams to heating environments similar to those the SLS will see during ascent.
Qualification testing of all the foam systems is anticipated to be completed later this year. At that point, the materials will be ready to use on Exploration Mission-1 in late 2018. "There are some follow-on aging tests that we will run over the next few years, but those are just being done to ensure we don’t have any problems with long-term storage of the cured-foam products," Frazier said.
So the next time you reach for a drink inside your cooler or shed the cold of winter in your home, think about another type of insulator that will be headed to deep space.
The initial SLS configuration, known as Block 1, will have a minimum 70-metric-ton (77-ton) lift capability. The next planned upgrade of SLS, Block 1B, will use a more powerful exploration upper stage for more ambitious missions with a 105-metric-ton (115-ton) lift capacity. Block 2 will add a pair of advanced solid or liquid propellant boosters to provide a 130-metric-ton (143-ton) lift capacity. In each configuration, SLS will continue to use the same core stage and four RS-25 engines.
Quelle: NASA
.
Update: 5.09.2016
.
Orion Crew Module Reaches Milestone in Processing for First Test Flight with NASA’s Space Launch System

The Orion crew module for Exploration Mission 1 was transferred into the clean room inside the Neil Armstrong Operations and Checkout Building at Kennedy Space Center in late July to begin installation of the spacecraft's critical systems, including propellant lines. Photo credit: NASA
Assembly of the Orion crew module for the first uncrewed flight test atop NASA’s Space Launch System reached a significant milestone this month in the Neil Armstrong Operations and Checkout Building high bay at the agency’s Kennedy Space Center in Florida. Lockheed Martin, manufacturer of Orion, and its subcontractor engineers, technicians and X-ray specialists completed the first propellant system tube welds on the exterior of the Orion pressure vessel.
Orion’s propulsion lines are comprised of multiple metal tubes of varying lengths that are welded together around the vehicle. With the first tubes in place, X-ray specialists performed inspections of the welds for any imperfections. This process will be repeated as each of the remaining tube assemblies are completed along the exterior of the crew module in the clean room.
“Completion of the first Orion propulsion system welds marks an important milestone for production of the next spacecraft for flight,” said Scott Wilson, NASA manager of production operations for the Orion Program. “We are moving from assembling structure to installing the critical systems that will propel Orion farther and farther from Earth than human-capable spacecraft ever have journeyed.”
The propellant lines will provide hydrazine to the spacecraft thrusters during missions into deep space. The propellant lines complete a continuous connection from the propellant tanks in the aft bay of the crew module to the spacecraft’s thrusters, which are part of the system that helps to steer the capsule during the mission.
“These first propulsion system welds marks a significant transition during the build-up of the crew module, signifying the completion of the structures assembly and the beginning of the fluid systems integration,” said Jules Schneider, Orion KSC operations manager with Lockheed Martin.
Orion was moved from the birdcage assembly fixture and secured in the clean room for the first time in late July. The first propellant system weld was completed in the clean room. The spacecraft’s critical systems, including the Environmental Control and Life Support System and propellant lines, will be completed in this room.
Orion is the NASA spacecraft that will send astronauts to deep-space destinations, including on toward the journey to Mars. The pressure vessel will contain the atmosphere that a crew would breathe during a mission. It also will provide living and working space for the crew, and withstand the loads and forces experienced during launch and landing.
The SLS rocket with Orion atop is targeted to launch from Kennedy’s Launch Pad 39B in 2018. EM-1 will send Orion on a path thousands of miles beyond the moon over a course of three weeks, farther into space than human spaceflight has ever travelled before. The spacecraft will return to Earth and safely splash down in the Pacific Ocean off the coast of California. The mission will advance and validate capabilities required for human exploration of Mars.
“Our human journey to Mars is underway. It is milestones like these that mark our progress to deep space,” Wilson said.
Quelle: NASA
-
Update: 7.09.2016
.
Report: Orion's aggressive launch plan hurt by 'funding instability'
-
A report issued by NASA's inspector general Tuesday said that "much work remains" in the space agency's effort to prepare its Orion spacecraft for an eventual flight to Mars in the 2030s.
Among the obstacles facing NASA, according to the report, are delivery delays of a service module for the spacecraft, multiple financial shortfalls and the need for a successful test flight in September 2018 that will send Orion around the moon.
That test flight will carry with it 13 small satellites into space as well.
The report found that "officials are working toward an optimistic internal launch date of August 2021 for (a crewed test launch around the moon) – 20 months earlier than the agency's external commitment date of April 2023."
According to the report, officials are "concerned" that the schedule, along with the program's budget, will ultimately mean deferments of certain tasks, resulting in a delay to the schedule and increased costs.
NASA has conducted several splashdown tests on the spacecraft, including one in late August.
The Orion spacecraft will carry with it 13 small satellites when it launches its next test flight.
"Over its life, the Orion program has experienced funding instability, both in terms of overall budget amounts and the erratic timing of receipt of those funds," the report read. "In past reports, we noted that the most effective budget profilefor large and complex space system development programs like Orion is steady funding in the early stages and increased fundingduring the middle stages of development."
Lockheed Martin, a main contractor on the mission, was also singled out in the report as spending financial reserves at a higher rate than company leaders expected, which could lead to an eventual financial shortfall for Orion.
Quelle: Orlando Sentinel
-
Update: 10.09.2016
.
We successfully test fired launch abort system for our human
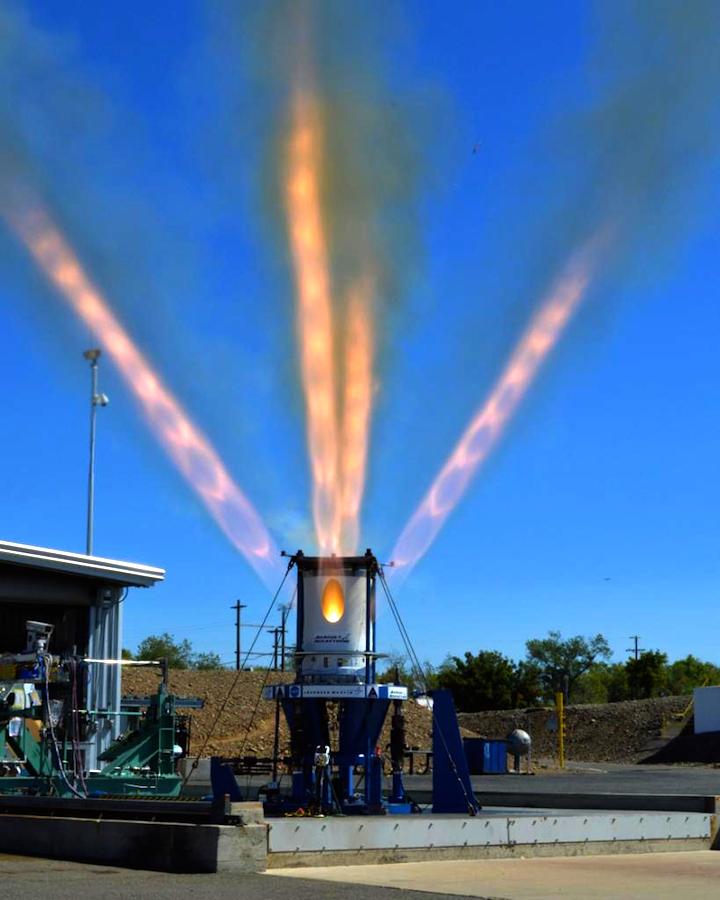
Quelle: NASA
-
Update: 19.09.2016
.
Orion Heat Shield for Next Space Flight Arrives at NASA’s Kennedy Space Center
Inside the Neil Armstrong Operations and Checkout Building high bay at NASA’s Kennedy Space Center in Florida, technicians assist as a crane lifts the Orion heat shield for Exploration Mission 1 away from the base of its shipping container. The heat shield arrived aboard the agency’s Super Guppy aircraft at the Shuttle Landing Facility, managed and operated by Space Florida, from Lockheed Martin’s manufacturing facility near Denver. The Orion spacecraft will launch atop NASA’s Space Launch System rocket on EM-1, an uncrewed test flight, in 2018. Photo credit: NASA/Dimitri Gerondidakis
The Orion heat shield, which will protect the Orion crew module during re-entry after the spacecraft’s first uncrewed flight test with NASA’s Space Launch System rocket, arrived at the agency’s Kennedy Space Center in Florida in August. It was transported to the Shuttle Landing Facility, which is managed and operated by Space Florida, aboard NASA’s Super Guppy aircraft.
The shipping container carrying the Orion heat shield for Exploration Mission 1 is offloaded from NASA’s Super Guppy aircraft at the Shuttle Landing Facility, managed and operated by Space Florida, at Kennedy Space Center. Photo credit: NASA/Dimitri Gerondidakis
The shipping container with the heat shield inside was offloaded and transported to the Neil Armstrong Operations and Checkout (O&C) Building high bay where technicians uncrated and secured it on a stand to begin the work to prepare it for Orion’s next test flight, known as Exploration Mission-1 (EM-1).
“We are very excited the EM-1 heat shield has arrived here at the Orion factory on the first leg of a journey that will ultimately take it beyond the moon and back,” said Scott Wilson, NASA manager of production operations for the Orion Program.
The heat shield was designed by the Lockheed Martin and NASA Orion team and built at the Lockheed Martin manufacturing facility near Denver. It is 16.4 feet wide (5 meters) in diameter, making it the largest of its kind.
The titanium truss structure has a composite substrate surrounding it. The heat shield will be capable of withstanding temperatures of up to 5,000 degrees F during Orion’s re-entry into Earth’s atmosphere.
“Arrival of the EM-1 heat shield structure at Kennedy marks a significant milestone that gets us one step closer to achieving NASA’s ultimate goal, sending humans to Mars and returning them safely to Earth,” said Jules Schneider, Lockheed Martin Orion KSC Operations senior manager.
In the O&C, technicians will apply the Avcoat, a type of thermal protection that wears away as it heats up (a process known as ablation), to the EM-1 heat shield in a different way than was done for Orion’s 2014 flight test. Blocks of Avcoat will be bonded to the heat shield rather than filling individual honeycomb cells. The way the structure is attached to the crew module for the EM-1 heat shield has been simplified. Several different types of instrumentation also will be installed on the heat shield to gather data on heating and performance.
After the thermal protection system has been applied and inspected, engineers and technicians will put the heat shield through a thermal cycle test. The thermal cycle test ensures the thermal protection blocks are properly bonded and will perform as expected when they are exposed to the extreme temperatures during the mission. The heat shield will be attached to the Orion crew module in the summer of 2017.
During EM-1, Orion will travel farther than any spacecraft built for humans has flown before. It will travel thousands of miles past the moon and then return to Earth. During its three-week mission, engineers will monitor how Orion’s systems perform in the environment of deep space and its return to Earth.
Orion is the spacecraft that will carry astronauts to deep-space destinations as NASA prepares for its Journey to Mars. Orion will be equipped with power, communications and life support systems to sustain space travelers during their missions and return them safely to Earth.
Quelle: NASA
-
Update: 22.09.2016
.
Everyone makes a big fuss about how to launch rockets up into space, but it’s important to remember that we also need to know how to recover them once they come back down to Earth. That’s why NASA is rehearsing how to best get its Orion spacecraft out of the ocean post-splashdown.
Orion — the space agency’s first new human spacecraft in a decade — might one day take mankind to Mars. It’s one of NASA’s biggest projects alongside the massive Space Launch System that will rocket it into space. Orion’s first flight on the SLS, Exploration Mission-1, won’t boast human passengers, but the testing process is extremely thorough. Hence, water.
Like the Apollo spacecraft before it, Orion will land in the water rather than on a runway like the Spaceshutter, which was built for much less-distant trips into space. NASA tested the splashdown last month, and measured how the impact into the water would affect the people inside, and now they’re rehearsing the next step — recovery.
Splashdown!
Orion was placed in NASA’s massive testing pool — the Neutral Buoyancy Laboratory — at the agency’s Johnson Space Center in Houston. A group of U.S. Navy divers, Air Force pararescuemen, and Coast Guard rescue swimmers came out to the floating craft to practice recovering the capsule, connecting cable lines that, in the real word, would tie to a Navy ship.
The rehearsals, which will also help prepare for the Underway Recovery Test 5 — the first major integrated test of the craft — began on September 20 and are expected to wrap up by the 22.
Exploration Mission-1 will take Orion around 40,000 miles past the moon for a three-week mission testing its systems and —- when it comes back to Earth for the much-prepared for splashdown — its heat shield.
Quelle: INVERSE