.
The first SLS flight engine roared to life for testing at Stennis Space Center on March 10, 2016. Intended for the first crewed SLS mission, EM-2, the engine last saw action powering the space shuttle Endeavor into orbit in 2011 on STS-134. Photo Credit: NASA
-
The first of 14 former space shuttle main engines, now being repurposed to power NASA’s Space Launch System (SLS), roared to life at Stennis Space Center in southern Mississippi today. Under highly instrumented and controlled conditions, the most efficient rocket engine in history unleashed over a half-million pounds of thrust on the deep south during a 500-second full duration hot fire test, marking the beginning of a new (second) series of test fires this year as engineers modify the engines to the new requirements for what will become the most powerful rocket in history.
“Every test is important, but there really is a different energy level associated with flight engines,” said Ronnie Rigney, RS-25 project manager at Stennis. “It’s hard to describe the feeling you get knowing you’re going to see that engine lift off into the sky one day soon. It’s a very exciting time for all of us here.”
The 500-second test fire, carried out by flight engine E-2059 on the historic A-1 test stand, went off without issue—something that has come to be expected of the RS-25 engine. The RS-25 was the first reusable rocket engine in history, as well as being one of the most tested large rocket engines ever made, having conducted more than 3,000 starts and over one million seconds (nearly 280 hours) of total ground test and flight firing time over the course of 30 years of NASA’s 135 space shuttle flights.
Aerojet Rocketdyne has 16 flight engines in inventory (14 former shuttle and 2 new), plus two more development test engines.
The engines proved their worth time and time again, but the RS-25 now requires several modifications to adapt to the new environment they will encounter with SLS and meet the giant 320-foot tall rocket’s enormous thrust requirements.
Engine E-2059 last saw action on space shuttle Endeavor in 2011, mission STS-134, powering the baby of NASA’s shuttle fleet into orbit on its 25th and final flight.
After its test series it will fly one more time, on the second mission of the SLS, Exploration Mission 2 (EM-2), the first mission with crew onboard to go beyond low-Earth orbit in 50 years (by the time that mission flies, no sooner than 2021 and as late as 2023).
“This rocket will take humans farther and faster into the solar system than we have ever traveled and increase our capability of making exciting new discoveries by launching large astronomical observatories and other scientific missions,” said Eileen Drake, Aerojet Rocketdyne CEO and president. “Mission success is our driving factor, which is why testing each engine is critical to ensure the safety of the astronauts and cargo that will fly on SLS.”
Last year NASA and Aerojet carried out a series of seven test fires on a development engine, #0525, to provide engineers with critical data on the engine’s new state-of-the-art controller unit—the “brain” of the engine, which allows communication between the SLS and the engine itself, relaying commands to the engine and transmitting data back to the vehicle. The new controller also provides closed-loop management of the engine by regulating the thrust and fuel mixture ratio while monitoring the engine’s health and status, thanks to updated hardware and software configured to operate with the new SLS avionics architecture.
“We’ve made modifications to the RS-25 to meet SLS specifications and will analyze and test a variety of conditions during the hot fire series,” said Wofford. “The engines for SLS will encounter colder liquid oxygen temperatures than shuttle; greater inlet pressure due to the taller core stage liquid oxygen tank and higher vehicle acceleration; and more nozzle heating due to the four-engine configuration and their position in-plane with the SLS booster exhaust nozzles.”
For shuttle flights the engines pushed 491,000 pounds of thrust during launch—each—and shuttle required three to fly, but for SLS the power level was increased to 512,000 pounds of thrust per engine (more than 12 million horsepower). The SLS will require four to help launch the massive rocket and its payloads with a 70-metric-ton (77-ton) lift capacity that the initial SLS configuration promises.
“Not only does this test mark an important step towards proving our existing design for SLS’s first flight,” said Steve Wofford, engines manager at NASA’s Marshall Space Flight Center in Huntsville, Alabama, where the SLS Program is managed for the agency. “But it’s also a great feeling that this engine that has carried so many astronauts into space before is being prepared to take astronauts to space once again on SLS’s first crewed flight.”
.
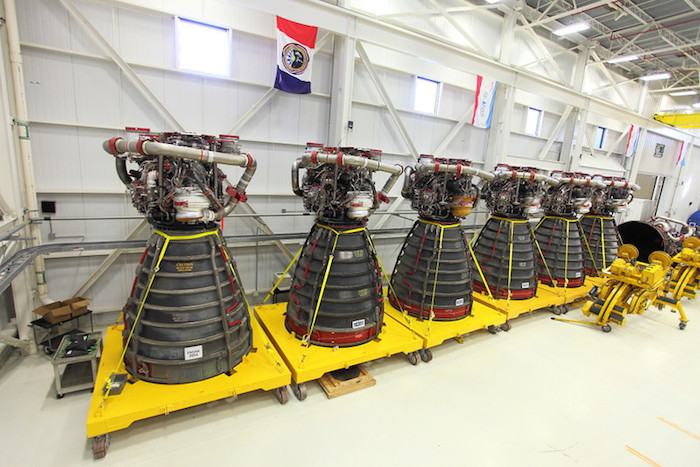
A row of Rocketdyne-built RS-25 Space Shuttle Main Engines just before being shipped to Stennis Space Center for use on the Space Launch System program. Photo Credit: Alan Walters
-
With engine E-2059 having carried out its test, engineers at Stennis will swap it for another development engine and conduct at least a handful of test fires with that this summer, followed by test firings of two new engines to the inventory that have never flown (engines 2062 and 2063).
An all out test fire of the SLS core stage, with all four of its engines, will be conducted at Stennis in late 2017, prior to the inaugural EM-1 flight of SLS with Orion no earlier than late 2018.
Known as the “Ferrari of rocket engines”, the RS-25 can handle temperatures as low as minus 400 degrees (where the propellants enter the engine) and as high as 6,000 degrees as the exhaust exits the combustion chamber where the propellants are burned.
To put the power of the Aerojet Rocketdyne-built RS-25 engines into perspective, consider this:
The fuel turbine on the RS-25’s high-pressure fuel turbopump is so powerful that if it were spinning an electrical generator instead of a pump, it could power 11 locomotives; 1,315 Toyota Prius cars; 1,231,519 iPads; lighting for 430 Major League baseball stadiums; or 9,844 miles of residential street lights—all the street lights in Chicago, Los Angeles, or New York City.
Pressure within the RS-25 is equivalent to the pressure a submarine experiences three miles beneath the ocean.
The four RS-25 engines on the SLS launch vehicle gobble propellant at the rate of 1,500 gallons per second. That’s enough to drain an average family-sized swimming pool in 60 seconds.
If the RS-25 were generating electricity instead of propelling rockets, it could provide twice the power needed to move all 10 existing Nimitz-class aircraft carriers at 30 knots.
“There is nothing in the world that compares to this engine,” said Jim Paulsen, vice president, Program Execution, Advanced Space & Launch Programs at Aerojet Rocketdyne. “It is great that we are able to adapt this advanced engine for what will be the world’s most powerful rocket to usher in a new space age.”
.
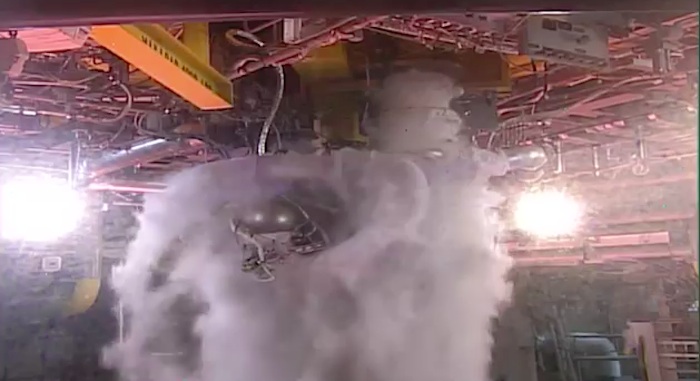
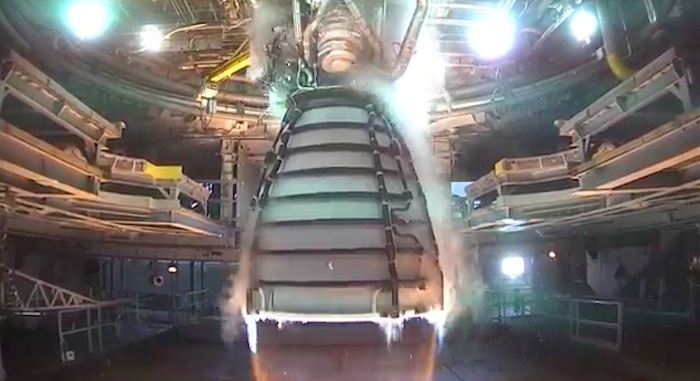
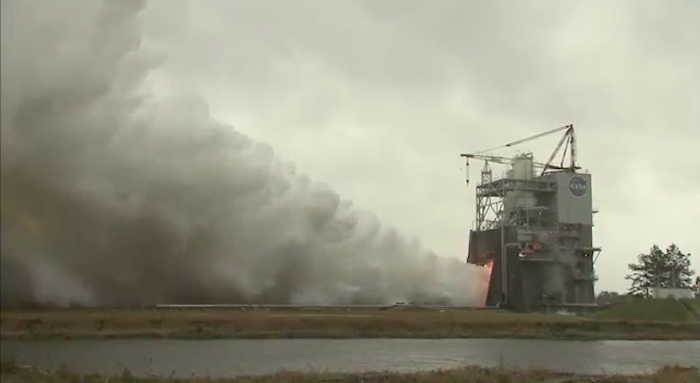
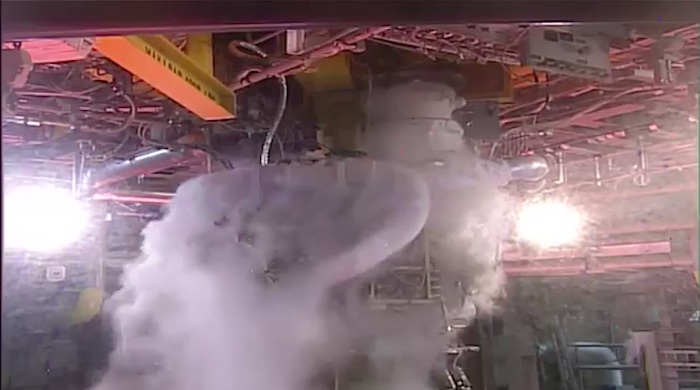
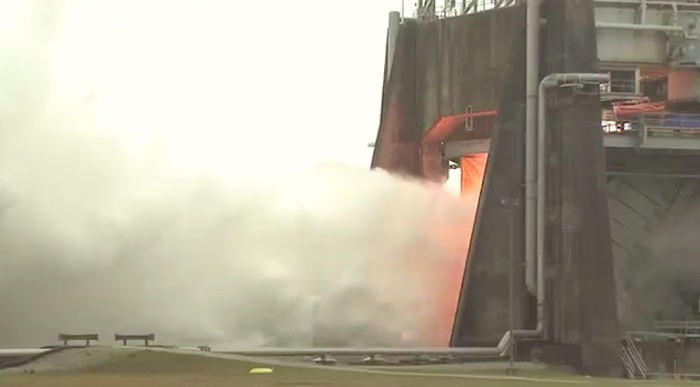
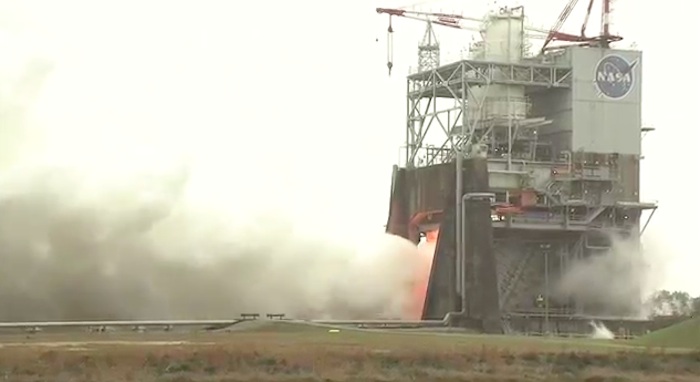
Quelle: AS
4613 Views