.
27.11.2015
The Ins and Outs of NASA’s First Launch of SLS and Orion
NASA is hard at work building the Orion spacecraft, Space Launch System (SLS) rocket and the ground systems needed to send astronauts into deep space. The agency is developing the core capabilities needed to enable the journey to Mars.
Orion’s first flight atop the SLS will not have humans aboard, but it paves the way for future missions with astronauts. Ultimately, it will help NASA prepare for missions to the Red Planet. During this flight, currently designated Exploration Mission-1 (EM-1), the spacecraft will travel thousands of miles beyond the moon over the course of about a three-week mission.
It will launch on the most powerful rocket in the world and fly farther than any spacecraft built for humans has ever flown. Orion will stay in space longer than any ship for astronauts has done without docking to a space station and return home faster and hotter than ever before.
“This is a mission that truly will do what hasn’t been done and learn what isn’t known,” said Mike Sarafin, EM-1 mission manager at NASA Headquarters in Washington. “It will blaze a trail that people will follow on the next Orion flight, pushing the edges of the envelope to prepare for that mission.”
SLS and Orion will blast off from Launch Complex 39B at NASA’s modernized spaceport at Kennedy Space Center in Florida. The spacecraft will deploy its solar arrays and the SLS upper stage, called the Interim Cryogenic Propulsion Stage (ICPS). This will give Orion the big push needed to leave Earth’s orbit and travel toward the moon. From there, Orion will separate from the ICPS. The ICPS will then deploy a number of small satellites, known as CubeSats, to perform several experiments and technology demonstrations.
As Orion continues on its path from Earth orbit to the moon, it will be propelled by a service module provided by the European Space Agency, which will supply the spacecraft’s main propulsion system and power (as well as house air and water for astronauts on future missions). Orion will pass through the Van Allen radiation belts, fly past the Global Positioning System (GPS) satellite constellation and above communication satellites in Earth orbit. To talk with mission control in Houston, Orion will switch from NASA’s Tracking and Data Relay System satellites and, for the first time for a human spaceflight vehicle in decades, communicate through the Deep Space Network.
The outbound trip to the moon will take several days, during which time engineers will evaluate the spacecraft’s systems and, as needed, correct its trajectory. Orion will fly about 62 miles (100 km) above the surface of the moon, and then use the moon’s gravitational force to propel Orion into a new deep retrograde, or opposite, orbit about 40,000 miles (70,000 km) from the moon.
The spacecraft will stay in that orbit for approximately six days to collect data and allow mission controllers to assess the performance of the spacecraft. During this period, Orion will travel in a direction around the moon retrograde from the direction the moon travels around Earth.
For its return trip to Earth, Orion will do another close flyby that takes the spacecraft within about 60 miles of the moon’s surface, the spacecraft will use another precisely timed engine firing of the European-provided service module in conjunction with the moon’s gravity to accelerate back toward Earth. This maneuver will set the spacecraft on its trajectory back toward Earth to enter our planet’s atmosphere traveling at 25,000 mph (11 kilometers per second), producing temperatures of approximately 5,000 degrees Fahrenheit (2,760 degrees Celsius) – faster and hotter than Orion experienced during its 2014 flight test. The spacecraft will splashdown in the Pacific Ocean off the San Diego coast.
This first exploration mission will allow NASA to use the lunar vicinity as a proving ground to test technologies farther from Earth, and demonstrate it can get to a stable orbit in the area of space near the moon in order to support sending humans to deep space, including for the Asteroid Redirect Mission. NASA and its partners will use this proving ground to practice deep-space operations with decreasing reliance on the Earth and gaining the experience and systems necessary to make the journey to Mars a reality.
.
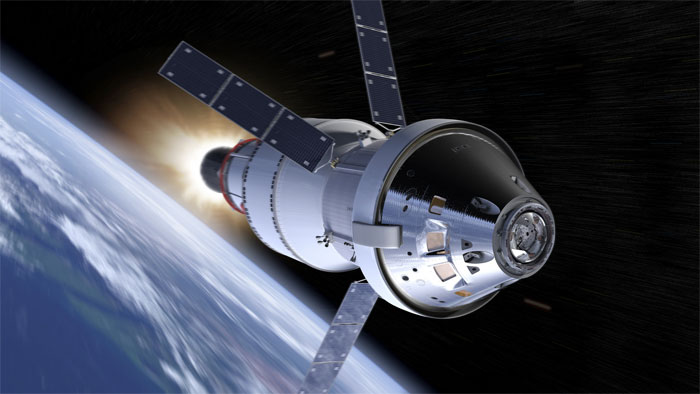
During Exploration Mission-1, Orion will venture thousands of miles beyond the moon during an approximately three week mission.
---
NASA TV to Air Event Marking Arrival of Test Orion Powerhouse
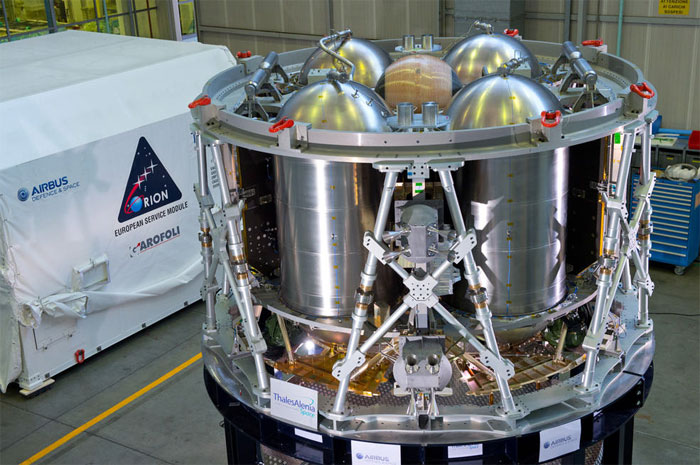
The structural test article of the European service module for Orion is being assembled at Airbus Defence and Space. Airbus is building the module, which will supply the spacecraft’s power, in-space propulsion and air and water for the crew, on behalf of ESA (European Space Agency) for Orion. The STA is being transported to Glenn Research Center's Plum Brook station for testing.
Credits: NASA
---
NASA Television will broadcast an event marking the arrival of a full-size test version of the service module provided by the European Space Agency (ESA) for NASA’s Orion spacecraft at 12:30 p.m. EST on Monday, Nov. 30 at the agency’s Plum Brook Station in Sandusky, Ohio.
Event participants will be:
Jim Free, director of NASA’s Glenn Research Center in Cleveland
Greg Williams, deputy associate administrator for Human Exploration and Operations at NASA Headquarters in Washington
Mark Kirasich, manager for the Orion Program at the agency’s Johnson Space Center in Houston
Mike Hawes, program manager for Orion at Lockheed Martin
Nico Dettmann, development department head at ESA
Oliver Juckenhoefel, vice president and head of the European Service Module program at Airbus Defence and Space
A brief question-and-answer session will take place during the event with media on site and by phone. Media that wish to ask questions on the phone must email their name, media affiliation and phone number to Jan Wittry at jan.m.wittry-1@nasa.gov by noon EST on Fri., Nov. 27. The public also can ask questions during the briefing on social media using #AskNASA.
The Orion spacecraft is being developed to help send astronauts to deep space destinations, such as an asteroid placed in lunar orbit and Mars. It will launch on the agency’s Space Launch System rocket. ESA, along with its contractor Airbus Defence and Space, is providing the service module for Orion’s next mission, a partnership that will bring international cooperation to the journey to Mars. The service module will supply power and propulsion to the Orion spacecraft for Exploration Mission-1.
ESA and Airbus also provided the structural representation of the service module so that NASA may conduct rigorous tests to ensure the module can withstand the trip to space. The multi-month test campaign will take place at Plum Brook’s Space Power Facility. Plum Brook is home to some of the largest testing structures in the world, including one of the world’s largest vacuum chamber, the world's most powerful spacecraft acoustic test chamber, and the world's highest capacity and most powerful spacecraft vibration table.
Quelle: NASA
-
Update: 30.11.2015
.
Orion’s Power System To Be Put To the Test
NASA is about to begin testing the heart of Orion’s power systems at the world’s largest, most powerful space environment simulation facility early next year. Test engineers at NASA Glenn Research Center’s Space Power Facility (SPF) in Sandusky, Ohio, are preparing to put a full-size test version of the European Service Module (ESM) for the spacecraft through a series of crucial tests to verify the structural integrity of the hardware to withstand the dynamic environment of launch into space atop the agency’s Space Launch System (SLS) rocket.
.
ESA’s European Service Module arrived in Cleveland in November and was transported to NASA Glenn’s Plum Brook Station for testing in the Space Power Facility in 2016.
Credits: NASA
.
Engineers will begin to evaluate the integrated stack hardware provided by ESA (European Space Agency) and its partners in February 2016. The hardware brings together new technology and lightweight materials while also taking advantage of spaceflight-proven elements.
“We added new facility capabilities for environmental testing over the last several years to meet the demands of validating the systems on the Orion ESM,” says Jerry Carek, SPF facility manager.
The first test will focus on the deployable solar array wing. Built by ESA partner Airbus DS, the solar arrays span 62 feet and engineers want to ensure the wing fully extends and retracts on command in the proper configuration.
During March and April, the test article will move into the world’s most powerful spacecraft acoustic test chamber to be pummeled with noise equivalent to 20 jet engines at full thrust. Each element of the ESM, at times separately and then fully assembled, will be blasted with at least 152 decibels and 20-10,000 hertz of sound pressure and vibration.
Moving into the Mechanical Vibration Facility, from May through July, the test article will be placed on a vibration table that simulates the shaking the spacecraft will expect when launching on top of its rocket. The table is attached to a 4.5 million pound concrete seismic mass anchored 50 feet into bedrock using 106 tension anchors.
“A series of repeated configuration tests will vibrate the stacked parts of the ESM from every possible angle,” says Robert Overy, chief engineer of the ESM Integration Office at NASA Glenn. “We want to push it past the extremes it might experience in the launch environment.”
The ESM is fitted with three protective fairings built by NASA’s prime contractor for Orion, Lockheed Martin. The fairings protect the avionics and electronics during ascent into space, but will eventually jettison off the spacecraft by a series of pyrotechnic shocks. Engineers will test the effectiveness of the pyro-shock action near the end of August. They will also conduct a pyro-shock test of the spacecraft adaptor to simulate the shock the service module will experience during separation.
Finally, the solar array deployment test will be conducted once again on the fully stacked ESM.
The test campaign aims to analyze and validate every element and function of the structural test article, which represents Orion’s power and life support systems. The tests are critical to ensuring the flight readiness and structural integrity of the module containing all the air, nitrogen and water for the astronaut crew, as well as in-space propulsion, batteries and solar arrays to generate power during deep space missions.
The Orion spacecraft is being developed to send astronauts to destinations including an asteroid placed in lunar orbit and on a journey to Mars. It will launch on the agency’s SLS rocket from a modernized spaceport at the NASA’s Kennedy Space Center in Florida. The first exploration mission of Orion and SLS will allow NASA to use the lunar vicinity as a proving ground to test technologies farther from Earth, and demonstrate it can get to a stable orbit in the area of space near the moon in order to support sending humans to deep space.
Quelle: NASA
-
Update: 5.12.2015
.
Engineers Prepare for Orion Water-Impact Testing with Precision to Protect Future Astronauts
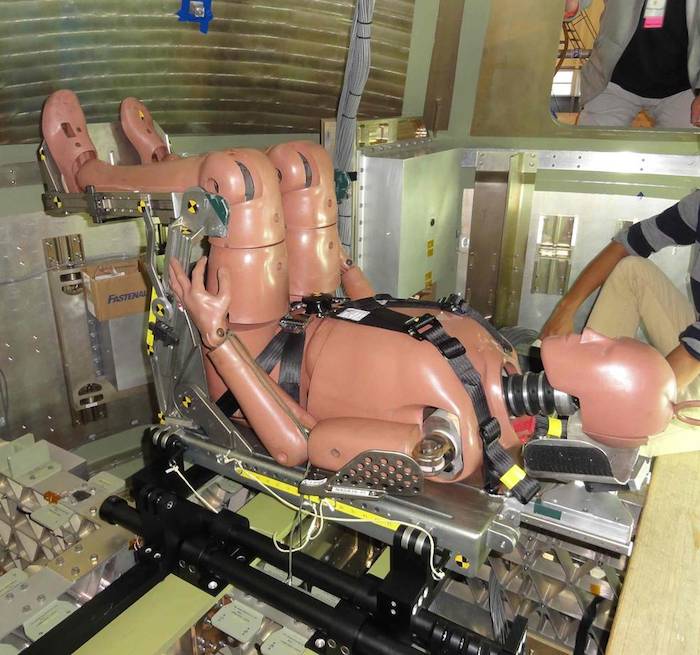
Engineers at NASA’s Langley Research Center in Hampton, Virginia, placed a test dummy inside a NASA Orion crew module mockup in preparation for next year’s water impact testing, which will simulate the spacecraft splashing down in the Pacific Ocean during future crewed missions.
Credits: NASA
-
When astronauts return to Earth in the Orion spacecraft, they will reenter on an extremely hot and fast journey through the atmosphere before splashing down in the Pacific Ocean. To protect the crew on landing, NASA will evaluate how the spacecraft may behave in parachute-assisted landings in different wind conditions and wave heights by conducting water-impact testing.
NASA’s Orion spacecraft will carry humans farther into space than ever before and provide emergency abort capability, sustain the crew during the space travel, and provide safe re-entry from deep space.
“The tests are designed to produce some of the most stressful water landing conditions that the spacecraft and crew may experience when returning to Earth from actual missions,” said Ellen Carpenter, project manager.
To prepare for this testing, the first major step at NASA’s Langley Research Center in Hampton, Virginia, was to couple an Orion crew module mockup with the heat shield from the spacecraft’s first flight test, Exploration Flight Test 1 (EFT-1).
"It is important to use a heat shield that is similar to what will be used on future Orion flights so the data obtained from these tests can be used to validate computer models,” Carpenter explained.
However, the heat shield, which fit perfectly with the EFT-1 Orion crew module, was not designed to mate with the mockup.
“It was challenging in the fact that we had to make sure the pieces were aligned horizontally, vertically, rotationally and then angularly,” Carpenter said.
To create perfect unity, the team had to design and fabricate integration hardware to connect the two pieces. With an accuracy of four thousandths of an inch, a laser tracker located several positions along the Orion mockup and heat shield in order to achieve nearly perfect alignment.
“This was crucial so that the integration hardware could be match drilled” Carpenter said. Match drilling is the process of precisely drilling holes through hardware components and ensures that the parts align properly in the final assembly.
During this effort, more than 400 holes were match drilled to assemble the mockup to the heat shield. At the same time, the team prepared the remainder of the mockup for water-impact testing. These preparations included placing instruments and sensors inside the structure and installing the system that will be used to store the sensor data from the water impact tests. The team then installed the crew seats and the crew impact attenuation system that is designed to lessen the shock load on astronauts during landing.
“In basic terms, it’s like a shock absorber on your car,” clarified Chris Tarkenton, design engineer.
Two test dummies were also installed in the crew seats. Data retrieved from sensors inside the dummies during testing will be used to evaluate the loads the crew may experience during an actual mission, which will aid in designing the systems to protect the crew from injury during water landings.
After the thorough work of joining the mockup and the heat shield for the first time, the team then disassembled the hardware to install sensors on the heat shield and conduct static tests. A static test applies a simple force to the heat shield structure while it is not in motion to verify that the sensor readings are consistent with the computer models.
“Preliminary static testing gives us the necessary confidence to calibrate the computer analytical models that simulate landing in the ocean,” Tarkenton said. “Then we’ll take the data collected from the actual water impact testing and use it to validate the models."
Following static testing, the team can move onto final vehicle assembly and ultimately to water-impact testing. During final assembly, the team will reattach the heat shield to the mockup, waterproof the entire assembly, complete final sensor checks, and then conduct the drop tests into the Hydro Impact Basin at Langley’s Landing and Impact Research Facility.
Engineers have developed numerous models to anticipate possible wave and wind conditions, but full-scale testing provides insights that can't be gained from models in the laboratory. Water-impact testing will improve the accuracy of computer models that will be used to design the crew module for future Orion missions.
Nine drop tests of the integrated Orion mockup and EFT-1 heat shield will be conducted at Langley next year. These tests are but one of the many steps necessary to ensure that NASA’s new spacecraft will meet the demands of sending humans to deep space for the first time and in the future on the journey to Mars.
.
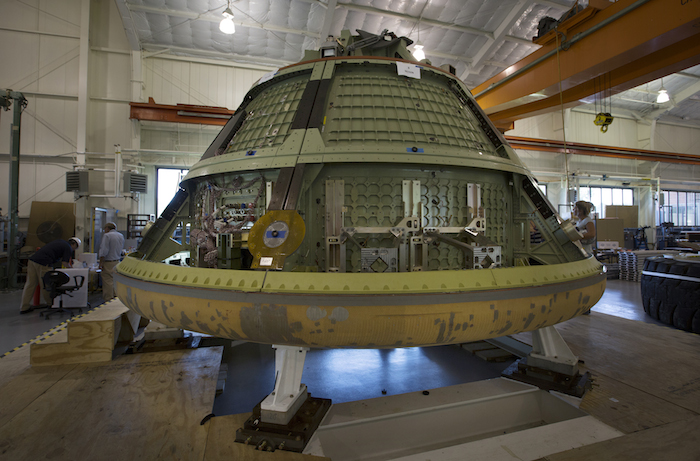
Engineers at NASA’s Langley Research Center in Hampton, Virginia, coupled a NASA Orion crew module mockup with the heat shield from the spacecraft’s first flight test, Exploration Flight Test 1 (EFT-1) . The integrated Orion mockup and EFT-1 heat shield will be tested next year to simulate water landings during actual missions.
Quelle: NASA
-
Update: 10.01.2016
.
Six Orion Milestones to Track in 2016
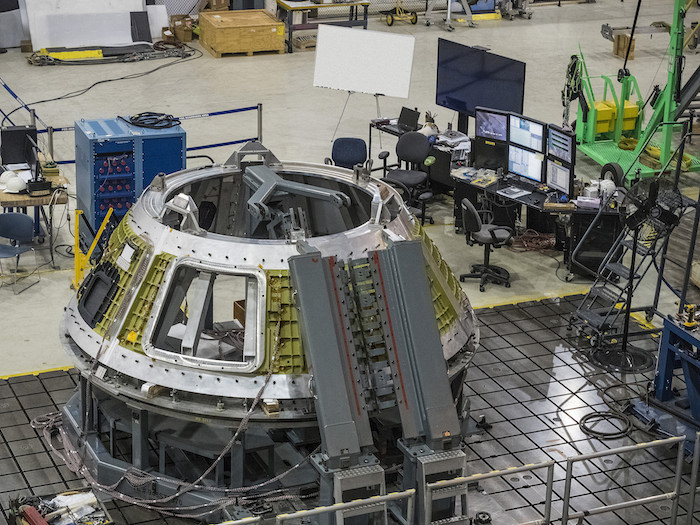
In November 2015, the cone panel section of the crew module pressure vessel was welded together, ahead of its shipment to Kennedy.
This year, engineers will make important progress developing and testing the Orion spacecraft that will send astronauts to deep space destinations on the journey to Mars. NASA will mark critical steps necessary in preparation for both the spacecraft's first mission to deep space atop the agency's Space Launch System (SLS) rocket, and for future missions with astronauts. Here's a look at some of the significant milestones and testing set for 2016.
Early in 2016, technicians at NASA's Michoud Assembly Facility in New Orleans will finish welding together Orion's pressure vessel, which will provide a sealed environment for astronaut life support in future human-rated crew modules, before shipping it to Kennedy Space Center in Florida.
Once there, engineers will start testing it to make sure the structure is sound and can endure the harsh conditions of deep space it will endure when it travels thousands of miles beyond the moon on the first integrated mission of Orion and SLS, known as Exploration Mission-1 (EM-1). Following a pressure proof test, the team will outfit the crew module with all of the avionics and systems the spacecraft needs before it can be integrated with the SLS rocket and processed for launch.
In Colorado, at the facilities of Orion prime contractor Lockheed Martin Space Systems Company, engineers will evaluate a new acoustic technology called Direct Field Acoustic Testing. The test will use customized, high-energy speakers configured in a circle around the crew module flown in space in 2014 to control how much energy reaches the vehicle.
The evaluation of the acoustic testing will determine if the method can produce enough energy to simulate the acoustic loads Orion will experience during launch and ascent on the SLS rocket. If the method proves to be an accurate representation of launch and ascent acoustic loads, it will be used to evaluate and verify Orion's ability to withstand those loads for EM-1.
NASA marked the arrival in November 2015 to NASA Glenn Research Center's Plum Brook Station of a structural representation of the Orion service module provided by ESA and built by Airbus. In 2016, engineers will put the test article through a series of crucial tests to verify the structural integrity and ability to withstand the dynamic launch environment atop the SLS rocket. In February, one of the service module's solar array wings will be deployed to make sure it unfurls and retracts properly.
After that, the test article will move to an acoustic chamber at Plum Brook to be pummeled with noise that simulates acoustic energy seen during launch, and then moved to a mechanical vibration facility to simulate the shaking it will experience atop its rocket. For the testing, the ESA-provided test article will be mated to a structural representation of the crew module adapter provided by Lockheed Martin.
Engineers will make strides in 2016 to build the Orion for the first integrated mission of the spacecraft atop SLS, but they'll also continue making progress preparing for future flights with astronauts.
In the spring, at NASA Langley Research Center's Hydro Impact Basin, NASA will mimic some of the most stressful water landing conditions Orion could experience with it returns from deep space and splashes down in the Pacific Ocean. Langley engineers have outfitted a test version of the crew module with Orion's heat shield that flew in space and two test dummies strapped inside to evaluate loads the crew may experience during real missions.
Orion's parachutes are essential to a successful mission, ensuring the capsule can slow down from its high-speed reentry to a relatively gentle 20 mph before splashdown. The Orion team has long been developing and conducting successful testing of the system of 11 parachutes in the skies above the U.S. Army Yuma Proving Ground and will begin qualifying the parachute system for crewed flights. The parachute team will begin the qualification tests this summer, which encompass eight integrated drop tests over a three-year period.
More than 30 flight-subsystem deliveries to Kennedy are planned in 2016 for installation into Orion: antennas, beacons, navigation equipment, vision processing, power management, data processing and vehicle management components all will complete manufacturing and testing this year to support the initial power-on of the EM-1 Orion spacecraft at Kennedy in early 2017.
The hardware is undergoing many "test like you fly" demonstrations to ensure the success during EM-1, including tests of the most challenging mission and environmental requirements the spacecraft has ever seen. At Lockheed Martin's Orion Test Lab in Littleton, Colorado, a full-scale Orion mockup is being used for integrated system level testing. The lab contains development copies of all EM-1 avionics, power and wiring hardware and will provide over a year's worth of mission simulation testing and debugging prior to Orion's power on at Kennedy.
The tests highlighted in 2016 are only part of the overall test plan for Orion and SLS in preparation for their first exploration mission. With the progress made so far, and tests planned at Kennedy in 2017 and 2018 when the rocket and ground systems are ready, NASA is on a path to be ready to launch EM-1 in 2018.
Quelle: SD
-
Update: 15.01.2016
.
NASA completes Orion parachute development tests

Orion's parachute system is a critical part of returning future crews who will travel to deep space on the journey to Mars and return to Earth in the spacecraft. The first parachutes deploy when the crew module is traveling more than 300 mph, and in a matter of minutes, the remaining parachute system slows the vehicle and enables it to splash down in the ocean at about 20 mph.
.
A dart-shaped test vehicle descended from the skies above the Arizona desert under Orion's parachutes Wednesday, Jan. 13, successfully completing the final development test of the parachute system. NASA engineers evaluated modifications to the system for the last time before the start of qualification testing for Orion missions with astronauts.
During the test, engineers demonstrated that when the spacecraft is traveling faster during descent than in previous tests, Orion's parachutes can properly deploy and withstand high-inflation loads. The dart-shaped vehicle allows engineers to simulate faster descent conditions than the capsule-shaped test article that has been used in many previous evaluations. The test also evaluated new, lighter-weight suspension line material for the parachutes saving a significant amount of mass.
"The completion of this last development test of the parachute system gives us a high degree of confidence that we'll be successful in certifying the system with the remaining qualification tests for flights with astronauts," said CJ Johnson, project manager for Orion's parachute system.
"During our development series, we've tested all kinds of failure scenarios and extreme descent conditions to refine the design and ensure Orion's parachutes will work in a variety of circumstances. We'll verify the system is sound during our qualification tests."
During Wednesday's test, a C-17 aircraft dropped the test vehicle from its cargo bay while flying 30,000 feet over the U.S. Army Yuma Proving Ground in Yuma, Arizona. NASA conducts the tests at the proving ground because of the capabilities of airdrop testing that exists there, and the ability for engineers to gather detailed video and photo imagery from chase aircraft to analyze how all of the parachute system's mechanisms work, including how mortars fire and the parachutes unfurl and descend.
Orion's parachute system is a critical part of returning future crews who will travel to deep space on the journey to Mars and return to Earth in the spacecraft. The first parachutes deploy when the crew module is traveling more than 300 mph, and in a matter of minutes, the remaining parachute system slows the vehicle and enables it to splash down in the ocean at about 20 mph.
The system is composed of 11 total parachutes that deploy in a precise sequence. Three parachutes pull off Orion's forward bay cover, which protects the top of the crew module - where the packed parachutes reside - from the heat of reentry through Earth's atmosphere.
Two drogues then deploy to slow the capsule and steady it. Three pilot parachutes then pull out the three orange and white mains, on which Orion rides for the final 8,000 feet of its descent. Orion's main parachutes are packed to the density of oak wood to fit in the top part of the spacecraft, but once fully inflated cover almost an entire football field.
The test was the seventh in the developmental series. In July, engineers will begin qualifying Orion's parachute system for flights with astronauts. The series will encompass eight drop tests over a three year-period.
Quelle: SD
-
Update: 17.01.2016
.
Engineers Mark Completion of Orion’s Pressure Vessel
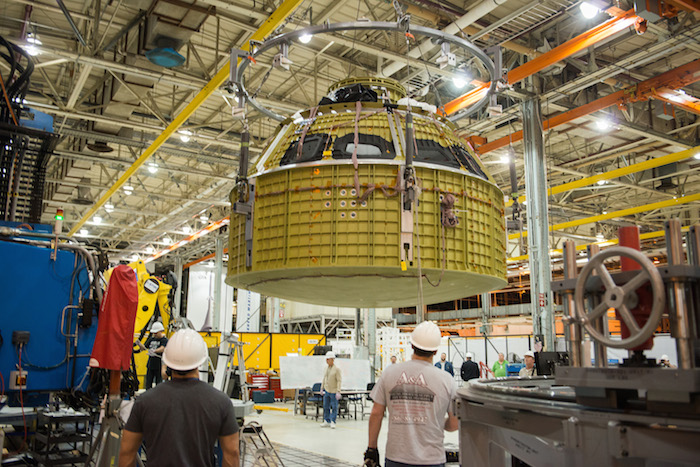
NASA’s Orion spacecraft is another step closer to launching on its first mission to deep space atop the agency’s Space Launch System (SLS) rocket. On Jan. 13, technicians at Michoud Assembly Facility in New Orleans finished welding together the primary structure of the Orion spacecraft destined for deep space, marking another important step on the journey to Mars.
“We’ve started off the year with an key step in our process to get ready for Exploration Mission-1, when together Orion and SLS will travel farther than a spacecraft built for humans has ever traveled,” said Mike Sarafin, Exploration Mission-1 manager at NASA Headquarters in Washington. “This brings us closer to our goal of testing our deep space exploration systems in the proving ground of lunar space before we begin sending astronauts days to weeks from Earth.”
Welding Orion’s seven large aluminum pieces, which began in September 2015, involved a meticulous process. Engineers prepared and outfitted each element with strain gauges and wiring to monitor the metal during the process. The pieces were joined using a state-of-the-art process called friction-stir welding, which produces incredibly strong bonds by transforming metals from a solid into a plastic-like state, and then using a rotating pin tool to soften, stir and forge a bond between two metal components to form a uniform welded joint, a vital requirement of next-generation space hardware.
“The team at Michoud has worked incredibly hard produce a lightweight, yet incredibly durable Orion structure ready for its mission thousands of miles beyond the moon,” said Mark Kirasich, Orion program manager. “The work to get us to this point has been essential. Orion’s pressure vessel is the foundation on which all of the spacecraft’s systems and subsystems are going to be built and integrated.”
The pressure vessel provides a sealed environment for astronaut life support in future human-rated crew modules. After final checkouts, technicians will prepare the pressure vessel for shipment to NASA’s Kennedy Space Center in Florida in the agency’s Super Guppy aircraft. At Kennedy, it will undergo several tests to ensure the structure is sound before being integrated with other elements of the spacecraft.
The uncrewed Exploration Mission-1 will pave the way for future missions with astronauts. During the flight, in which SLS and Orion will launch from NASA’s modernized spaceport at Kennedy, the spacecraft will venture to a distant retrograde orbit around the moon. This first exploration mission will allow NASA to use the lunar vicinity as a proving ground to test technologies farther from Earth, and demonstrate it can get to a stable orbit near the moon in order to support sending humans to deep space.
.
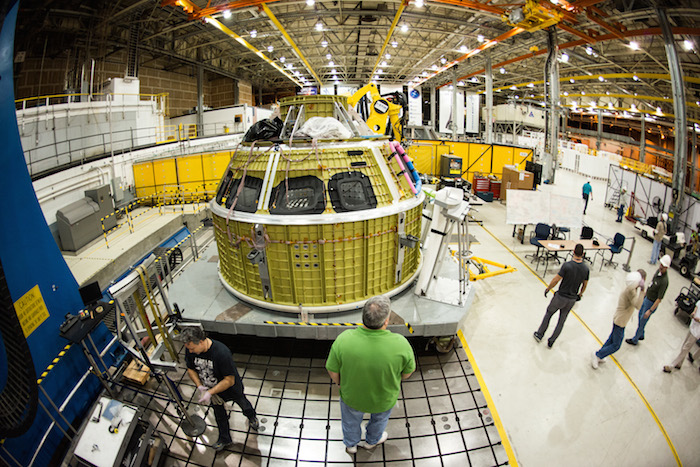
Quelle: NASA
-
Update: 24.01.2016
.
Media Invited to Orion Crew Module Arrival Events at Kennedy Space Center
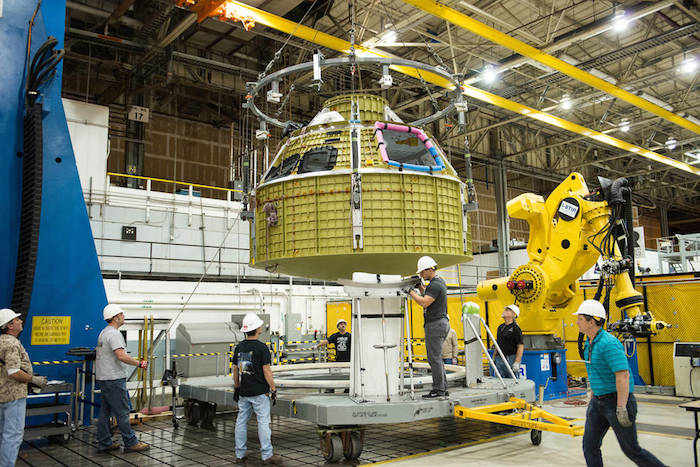
Welding work on the pressure vessel, or underlying structure, of the Orion crew module was completed at NASA’s Michoud Assembly Facility in New Orleans. It will be shipped to the agency’s Kennedy Space Center in Florida Feb. 1 for outfitting and processing.
Credits: NASA
-
Media representatives are invited to attend two events at Kennedy Space Center in Florida marking the arrival of the Orion crew module pressure vessel that will fly atop the Space Launch System rocket on the first integrated flight test, Exploration Mission-1, (EM-1). Delivery of this major Orion hardware marks an important milestone as NASA continues making progress on its journey to Mars.
At 3 p.m. EST, Monday, February 1, Orion’s recently completed pressure vessel, or underlying structure of the crew module, is scheduled to arrive at Kennedy’s Landing Facility aboard NASA’s Super Guppy cargo aircraft. Members of the news media will have the opportunity to photograph the arrival and unloading of the spacecraft.
At 10 a.m. EST, Wednesday, February 3, media may view the spacecraft in the Neil Armstrong Operations & Checkout Facility and conduct interviews with NASA and Lockheed Martin representatives.
NASA and Lockheed Martin are tracking several milestones for Orion in 2016. The processing of Orion for flight at Kennedy will include outfitting the crew module with the spacecraft’s heat-shielding thermal protection systems, avionics and other subsystems including electrical power storage and distribution, thermal control, cabin pressure control, command and data handling, communications and tracking, guidance, navigation and control, reaction control system propulsion and flight software and computers.
To attend the event, media accreditation requests should be submitted online at:
https://media.ksc.nasa.gov
International media accreditation for this event is closed. U.S. must apply for accreditation by 4 p.m. January 29. Two forms of government-issued identification are required to receive a badge, one of which must be a photo ID such as a driver’s license or passport. Badges will be available for pick up at the Kennedy Badging Office on State Road 405 east of the Kennedy Space Center Visitor Complex. Hours for the Kennedy Badging Office are 6 a.m. to 3 p.m. Questions concerning accreditation may be addressed to Jennifer Horner at 321-867-6598 or jennifer.p.horner@nasa.gov.
For the February 1 event, media should arrive at the press site by 2 p.m. for transportation to the landing facility.
Media should arrive at the press site by 9 a.m. for transportation to the event Feb. 3.
For both events, all participants must be dressed in full-length pants and shirts with sleeves, and wear flat shoes that cover the feet entirely.
Dates and times are subject to change. Updates for events are available at 321-867-2525.
The Orion spacecraft will carry astronauts farther into the solar system than ever before. It will provide emergency abort capability, sustain the crew during the space travel and provide safe re-entry from deep space.
Quelle: NASA
.
Update: 3.01.2016
.
The Orion Crew Module Pressure Vessel
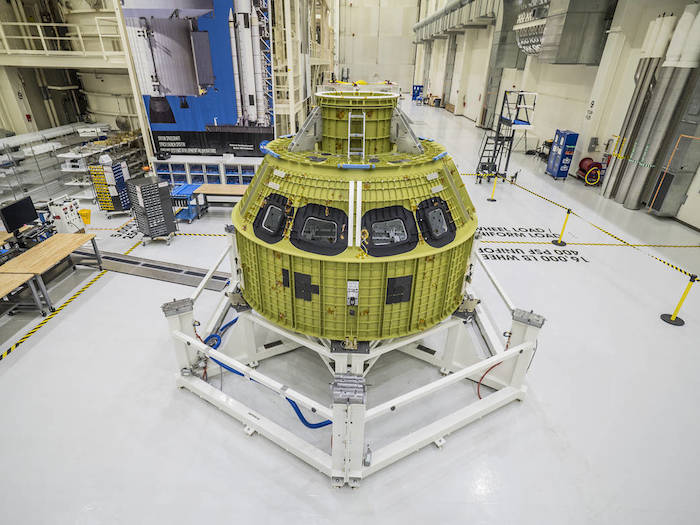
The Orion crew module pressure vessel for NASA’s Exploration Mission-1 (EM-1) is secured in an upgraded version of a test stand called the birdcage in the high bay inside the Neil Armstrong Operations and Checkout (O&C) Building at the agency’s Kennedy Space Center in Florida. The pressure vessel, which is the crew module’s underlying structure, arrived Feb. 1 aboard NASA’s Super Guppy aircraft at the Shuttle Landing Facility operated by Space Florida at Kennedy. The module was transported from the agency's Michoud Assembly Facility in New Orleans, where its seven large pieces were welded together over the course of several months. At Kennedy, it was offloaded from the aircraft and transported to the O&C. In the high bay, Orion will be prepared for its mission. It will be outfitted with the systems and subsystems necessary for flight, including its heat-shielding thermal protection system. The Orion spacecraft will launch aboard NASA’s Space Launch System rocket on a test flight that will take it thousands of miles beyond the moon over the course of about a three-week mission.
Quelle: NASA
.
Update: 1.03.2016
.
Orion Solar Array Wing Deployment Test is a Success
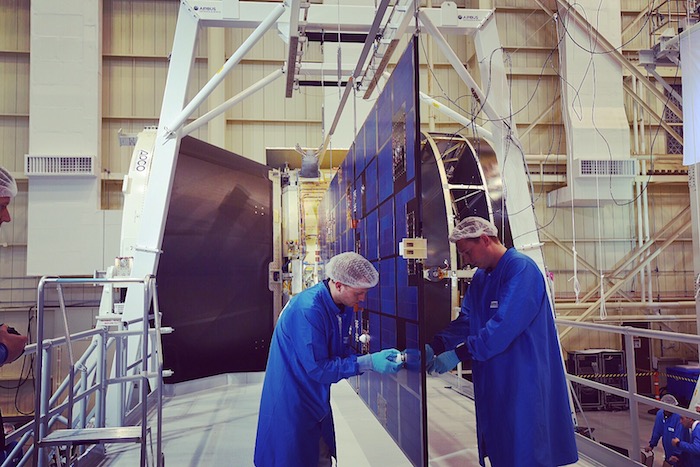
Engineers examine one of Orion’s solar array wing after a test.
.
An international team of engineers deployed an Orion solar array wing inside the Space Power Facility (SPF) at NASA Glenn’s Plum Brook Station in Sandusky, Ohio on Feb. 29.
The deployment of the 24-foot wing qualification model was an important first step to verify Orion’s power system for the spacecraft’s first flight atop the agency’s Space Launch System (SLS) rocket, known as Exploration Mission-1 or EM-1, which will venture tens of thousands of miles beyond the moon.
“We check to make sure everything works exactly as it should in flight” said Meg Nazario, NASA Glenn Test and Transportation project manager. “We want to see if there are any issues now so they can be fixed before the mission.”
The solar array is based on the ESA (European Space Agency) Automated Transfer Vehicle’s X-shaped array of four panels. Together, the four panels will generate 11 kilowatts of power and span about 63 feet when extended. The array is a component of Orion’s service module, which is being provided by ESA and built by Airbus Defence and Space to supply Orion’s power, propulsion, air and water.
The first of two wing deployments to take place in SPF this year, the test confirmed that the array unfurled properly and locked into place and that all of the mechanisms functioned as expected.
Prior to deployment, the wing was held in a stowed position by four Kevlar straps. When an Airbus Netherlands test engineer issued the command for the wing to deploy, thermal knives cut the straps to release the array wing. The design includes two thermal knives for each strap for redundancy. After the wing deployed, Airbus engineers performed what they call a “glow test” to make sure the thermal knives heated as they should and activated simultaneously.
The successful deployment was the first in a series of crucial tests being performed at SPF to verify the Orion service module can withstand the harsh conditions of launch and ascent into deep space. SPF is the only place in the world that can subject the full-scale, flight-like test article to the conditions of launch and ascent. It is home to the world’s largest mechanical vibration table and most powerful acoustic chamber.
Throughout spring and fall, engineers will use those facilities to mimic the shaking and noise the service module will experience during its ascent into space. They also will use pyrotechnics to simulate the shock the service module will experience during separation from the SLS rocket. In early fall, they’ll conclude the campaign with another solar array wing deployment test.
“Today’s deployment kicked off our test campaign and set a baseline for the second array test. It proved that everything was shipped and installed correctly and that the array is functional,” said Nazario. “The second one will show that it withstood the launch environment. That is when everyone will be holding their breath.”
Months of preparation led to the successful deployment. As parts of the test article arrived from across Europe and the United States, the team meticulously inspected, stacked and assembled them. On Feb. 20, they carefully tilted the test article -- which includes structural representations of the service module, crew module adapter, and spacecraft adapter -- to a 90 degree angle to position it for the deployment test. Last week, they attached the test wing, instrumentation and mass simulators to represent the other wings.
“For Orion, this test was also important because it was the first time we integrated NASA and Lockheed Martin hardware with hardware from our European partners,” said Ben Van Lear, NASA Glenn assembly and integration lead for the test campaign. “We are proving out our planning, assembly and integration together. It is really a pathfinder for the EM-1 flight.”
With the first solar array wing test complete, engineers will waste no time preparing for the next test. This week, they will begin stacking the Orion crew module and launch abort system mass simulator on top of the test article and attaching the outer fairings in preparation for acoustic tests to begin this spring.
The Orion spacecraft is being developed to send astronauts to deep space destinations, such as an asteroid placed in lunar orbit and on a journey to Mars.
.
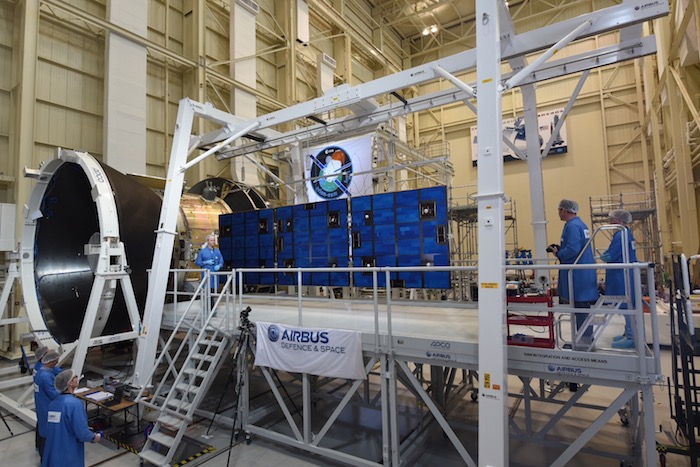
One of Orion’s solar arrays was successfully deployed in a Feb. 29 test at NASA Glenn’s Plum Brook Station to ensure it can properly unfurl.
.
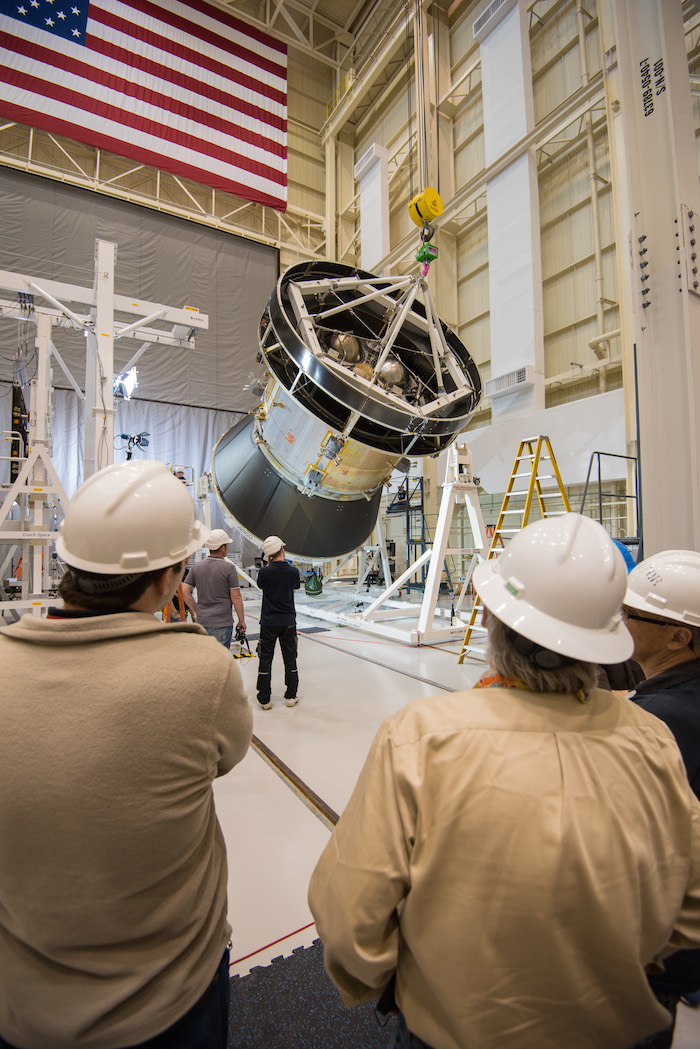
A representative structure of Orion’s service module, which is being testing at Plum Brook Station, was tilted to a 90 degree angle in preparation for the solar array deployment test.
Quelle: NASA
-
Update: 2.03.2016
.
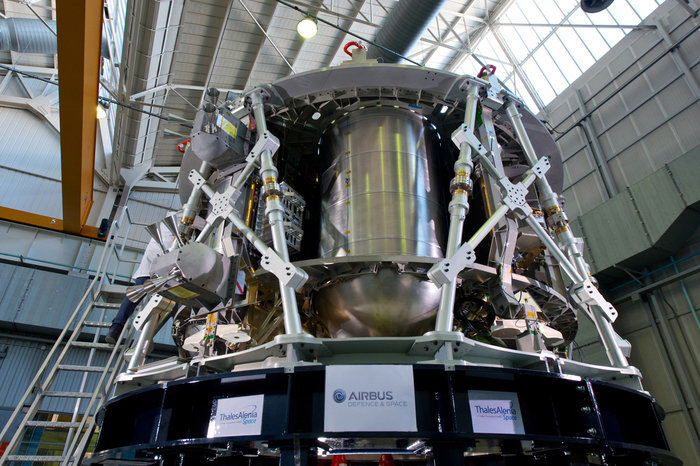
ESA's Orion structural test article assembled at Airbus Defence and Space. Airbus is building the module, which will supply NASA's Orion spacecraft’s power, in-space propulsion and air and water for the crew.
The design of the European Service Module is based on the Automated Transfer Vehicle (ATV), the European supply craft for the International Space Station. It is a cylindrical module with a diameter of 4.5 metres and a total length – main engine excluded – of 2.7 metres. It is fitted with four solar array ‘wings’ with a span of 18.8 metres.
.
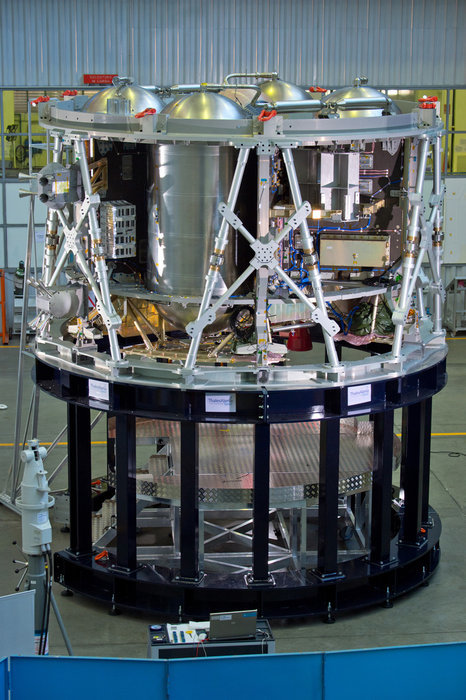
ESA's Orion structural test article assembled at Airbus Defence and Space. Airbus is building the module, which will supply NASA's Orion spacecraft’s power, in-space propulsion and air and water for the crew.
The design of the European Service Module is based on the Automated Transfer Vehicle (ATV), the European supply craft for the International Space Station. It is a cylindrical module with a diameter of 4.5 metres and a total length – main engine excluded – of 2.7 metres. It is fitted with four solar array ‘wings’ with a span of 18.8 metres.
.
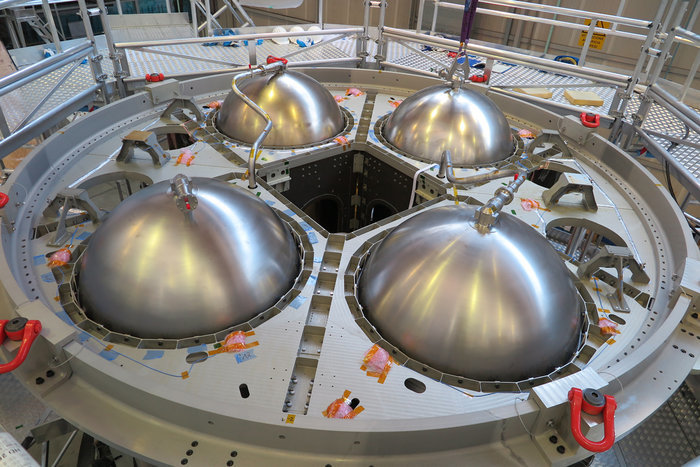
ESA's Orion structural test article assembled at Airbus Defence and Space. Airbus is building the module, which will supply NASA's Orion spacecraft’s power, in-space propulsion and air and water for the crew.
The design of the European Service Module is based on the Automated Transfer Vehicle (ATV), the European supply craft for the International Space Station. It is a cylindrical module with a diameter of 4.5 metres and a total length – main engine excluded – of 2.7 metres. It is fitted with four solar array ‘wings’ with a span of 18.8 metres.
.
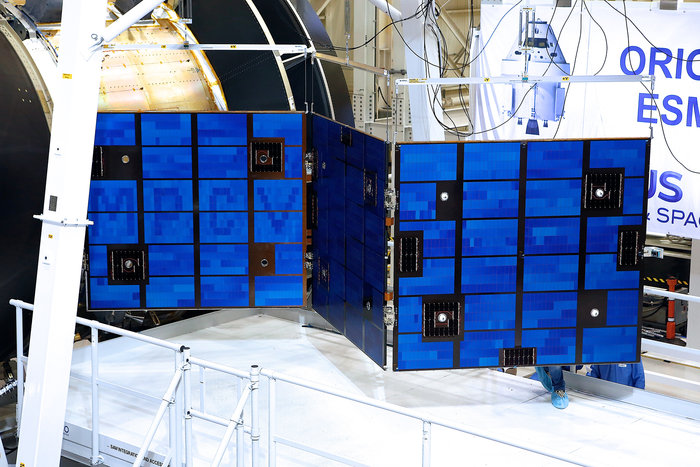
On 29 February a test model of Orion’s solar array was unfolded at NASA’s Plum Brook Station test facility in Sandusky, Ohio to check everything works as expected. The solar panels were made by Airbus Defence and Space in the Netherlands for the ESA module that will supply power and life support for up to four astronauts.
Each wing stretches more than 7 m, folded inside the Space Launch Systems rocket that will launch the spacecraft on its first unmanned mission in 2018. Orion sports four wings of three panels with 1242 cells per panel to provide 11.1 kW of power – enough to run two typical European households. The distinctive X-wings are an evolution and improvement of ESA’s Automated Transfer Vehicle.
The test was passed with flying colours as the 260 kg array unfurled into its flight configuration. The stresses of flying to the Moon and beyond – and back again – mean the array is designed to bend up to 60º forward and backward, much like a bird in flight.
“That broad movement meant we had to design the wing with thickened solar panels and reinforced hinges and beams, which required extensive testing,” says Arnaud de Jong, head of the Airbus Defence and Space Solar Array team in Leiden, the Netherlands.
The wing tips are expected to deflect more than a metre. A camera on each wing tip, looking back at the spacecraft, will closely monitor the movement.
Further tests will look at how the solar array handles acoustic shocks, vibrations and other shock tests in the following months.
Read more about Orion on ESA’s website or on the ESA’s Orion blog for regular updates, including a video of yesterday’s unfurling.
Quelle: ESA
-
Update: 29.03.2016
.
Pathfinder Operations Will Pave Way for Space Launch System Processing
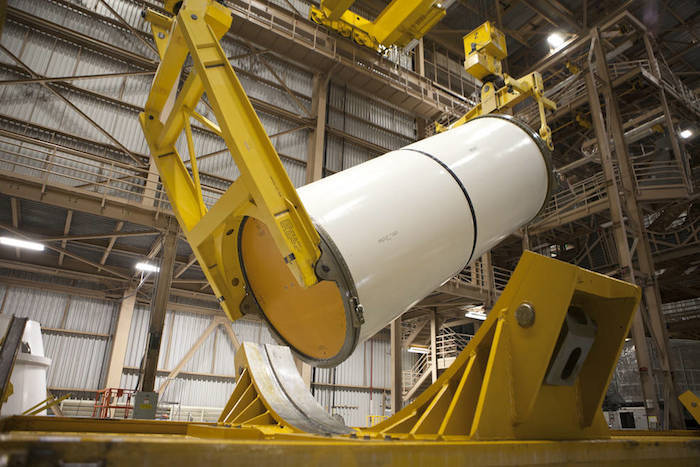
Inside the Rotation, Processing and Surge Facility high bay at NASA’s Kennedy Space Center in Florida, two cranes are used in tandem Feb. 25 to lift the first of two pathfinders, or test versions, of solid rocket booster segments for NASA’s Space Launch System rocket away from a railcar. The booster segment will be raised into the vertical position. The Ground Systems Development and Operations Program and Jacobs Engineering, on the Test and Operations Support Contract, are conducting a series of lifts, moves and stacking operations using the booster segments, which are inert, to prepare for Exploration Mission-1, deep-space missions and the journey to Mars. The pathfinder boosters arrived at Kennedy from Orbital ATK in Utah aboard an Iowa Northern train contracted by Goodloe Transportation of Chicago. Photo credit: NASA/Ben Smegelsky
-
NASA’s Space Launch System, or SLS, rocket will be the most powerful in the world, and is the vehicle that will launch humans beyond low-Earth orbit and on to deep space destinations as the agency continues its journey to Mars. The Ground Systems Development and Operations Program at Kennedy Space Center in Florida is preparing its workforce, facilities and ground support equipment to handle the processing requirements of the SLS rocket and Orion spacecraft for its first launch.
A team of NASA engineers and Jacobs Engineering technicians and crane operators on the Test and Operations Support Contract are preparing for Exploration Mission-1 (EM-1) processing activities. During EM-1, SLS will launch the Orion crew capsule that will travel thousands of miles beyond the moon over the course of about a three-week mission. No humans will be aboard, but it will pave the way for future missions with astronauts. Ultimately, it will help NASA prepare for missions to the Red Planet.
Experienced personnel are leading the preparation effort using pathfinders, or test versions, of an aft skirt and two inert segments of a solid rocket booster (SRB) inside the Rotation, Processing and Surge Facility (RPSF).The aft skirt and booster segments are similar to those that will be used on the SLS rocket. At launch, the twin SRBs will provide more than 75 percent of the total SLS thrust and operate for about two minutes before separating from the core stage. The aft skirt is at the base of the booster and contains the system that will steer the booster nozzles.
“The RPSF was used for space shuttle booster segments,” said acting NASA Integrated Operations Flow Manager David Diaz. “Upgrades and modifications to the heritage test stands and work platforms recently were completed to accommodate the new aft booster assembly, and particularly the longer nozzle.”
The SLS will use two, five-segment solid rocket boosters. Each is 177 feet long and 12 feet in diameter, with upgraded avionics and control systems. They each will provide 3.6 million pounds of thrust at launch.
The aft skirt Pathfinder was transported from the Booster Fabrication Facility, or BFF, to the RPSF on Jan. 20. The BFF is operated by Orbital ATK for NASA’s Marshall Space Flight Center in Huntsville, Alabama. The two booster Pathfinder segments arrived by train, at Kennedy’s Jay Jay railroad yard Feb. 2 from Orbital ATK in Promontory, Utah. The segments were transferred by rail to the RPSF on Feb. 23.
Technicians removed the covers from the boosters and performed a simulated grain inspection of the interiors. Crane operators used the facility’s two cranes in tandem to lift the booster segments off of the railcars, raise them to the vertical position and lower them onto test stands. Engineers then hoisted the pathfinder aft segment to the build-up stand and mated with the aft skirt. Next, the team used a modified dolly and elevator platform to lift and mate the aft exit cone to the aft skirt.
Engineers will next lift the entire aft booster assembly to check for interferences as it is moved to a pallet and then back onto the work platform. The aft assembly will be used to check for interferences with modified ground support equipment. Installation of the Core Stage Adapter ring and struts will be performed before the aft assembly is transported to the Vehicle Assembly Building for additional verification and validation.
“After we’ve completed pathfinder operations in the RPSF we will continue with additional testing operations in the Vehicle Assembly Building,” said Kerry Chreist, project flow manager with Jacobs. “The crane operators in the RPSF will operate the cranes in both facilities.”
These pathfinder operations are performed to help verify that the upgrades and modifications completed in the RPSF will support processing requirements for the aft skirt, SRB segments and the integrated aft booster assembly, to ensure a smooth liftoff at launch.
.
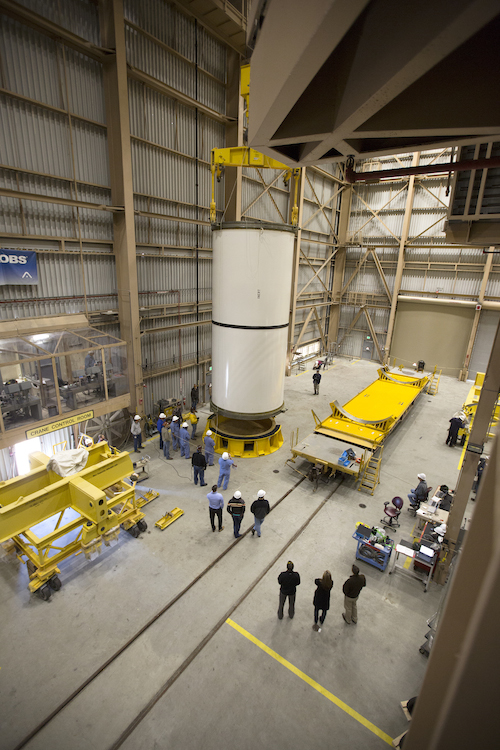
The first of two pathfinders, or test versions, of solid rocket booster segments for NASA’s Space Launch System rocket was raised into the vertical position Feb. 25 and then lowered onto a test stand. Photo credit: NASA/Ben Smegelsky
Quelle: NASA
5037 Views