.
17.10.2015
The Orion space capsule with the Launch Abort System - designed by Aerojet Rocketdyne of Rancho Cordova. Picture courtesy: NASAPhoto courtesy of NASA
.
New abort system gives new level of safety to astronauts
Rancho Cordova's Aerojet makes abort system that launches in a millisecond
RANCHO CORDOVA, Calif. (KCRA) —It’s easy to think that being in outer space is dangerous.
“It was on the top of my mind,” said astronaut Steve Robinson, who is now a professor at UC Davis, “All of our minds, really.”
One of the most dangerous times in any space flight is from “T-minus five, four, three two, one, and liftoff” and past the point of the now tragic phrase, “Challenger, go with throttle-up.” It is the point where the first tragedy in the shuttle program happened.
“You have to accept significant risk when you fly into space,” Robinson said. “We felt that it was worthwhile. I still feel that it's worthwhile.”
He has been through those dangerous experience four times.
“In the back of your mind you're going, 'I'm on a rocket,'” Robinson said laughing. “We're shaking around. I'm being smashed into the seat, (and) things are bouncing around.”
Robinson was the flight engineer on several missions. His job was to keep an eye on all the instruments, think about all the systems and wait for something to fail or malfunction.
NASA’s next manned space mission, Orion, might help those astronauts breathe a little easier.
“If anything were to go wrong, what we'd want to do is get the crew away from the launch vehicle,” said Sam Wiley, head of human space development for Aerojet Rocketdyne.
Wiley’s job is a launch abort system that will actually yank the capsule off the launch system.
“It's your ejection seat,” Robinson said.
An ejection seat on steroids.
“It's a heck of a ride. It puts the astronauts under about 13 G's of acceleration,” Wiley said. That’s 13 times the force of gravity on a body standing on the ground.
The ride from that Launch Abort System, or LAS, will engage in a millisecond if anything goes wrong during launch.
“Once the capsule's away, this jettison motor, this thing applies about 40,000 pounds of thrust in about a second and a half,” Wiley said.
The LAS was already tested a couple of years ago.
“It snapped [the crew capsule] off the ground, flew it up in the air, this motor fired, separated the launch abort system from the capsule and went through its whole landing sequence and safely landed,” Wiley said.
They tested it again in December when the full Orion rocket and capsule were launched, unmanned.
Every launch has to eject the LAS once they leave the atmosphere, so it has to operate correctly for every single launch.
“This is actually going back to some of the things in Apollo,” Wiley said.
But it may go back even farther. One of the Gemini missions used a Launch Abort System to remove the crew capsule from a malfunctioning rocket.
“It's a way to protect the crew. So, yes, it's all about safety, and safety of the crew and making sure that they're good on their way,” Wiley said.
None of the shuttle missions, however, had this system.
“If something went wrong during the rocket-powered ascent through the atmosphere, then you had to deal with it in very complicated ways. You could not escape the spacecraft,” Robinson said.
.
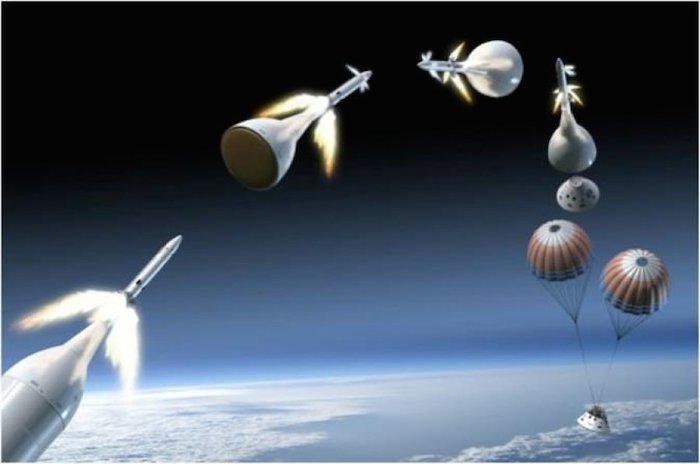
That will change during what NASA is calling the “Journey to Mars." It’s a mission both Wiley and Robinson are excited about, even if they are both down here on the ground.
“It's going to be great to be back in the business of launching American citizens on American-made hardware,” Robinson said. His successors in the space program can know that this most dangerous part of the mission might just be a little safer.
“We hope that we never have to use it, but it's there in case something goes wrong. We can save the crew,” Wiley said.
“I flew high-performance jet aircraft for 17 years, and I always had an ejector seat,” Robinson said. “That made me feel good. I never used it, but it always made me feel very secure.”
Orion is set for an unmanned mission to orbit the moon sometime after 2017.
Quelle: 3KCRA
---
Update: 18.11.2015
.
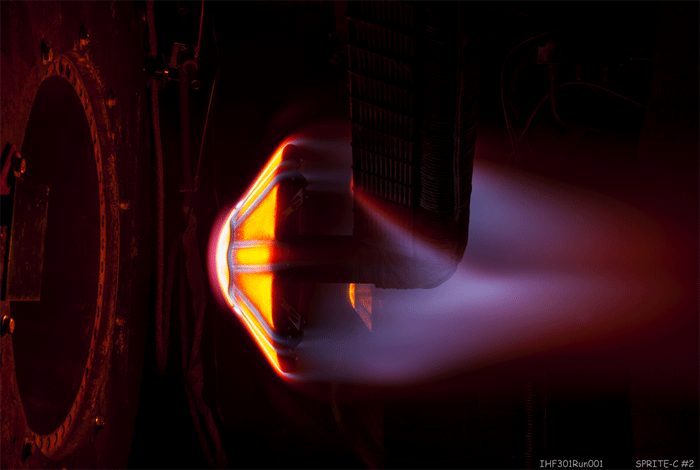
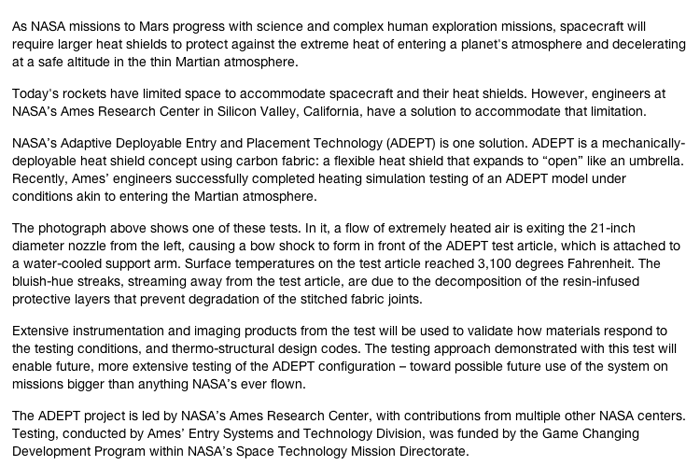
Quelle: NASA
.
Orion Ingenuity Improves Manufacturing While Reducing Mass
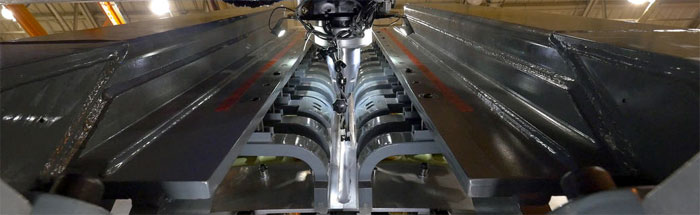
How do you reduce the weight of a spacecraft’s underlying structure, while using the same materials as the heavier version and still hold to the same manufacturing schedule?
This month, the engineers who helped answer that question are seeing their hard work pay off. Technicians have finished welding together three cone panels that make up a section of the Orion crew module that will fly beyond the moon on Exploration Mission-1 (EM-1).
Orion’s pressure vessel is composed of seven large pieces of aluminum, three of which are the cone panels. The pressure vessel holds the atmosphere astronauts will breathe against the vacuum of deep space, forming the crew compartment. The three panels together form the angled mid-section around the crew module where the windows and hatch are located. While technicians have been joining other elements of the structure together since early September, the cone panels have presented a unique challenge for NASA and Lockheed Martin, the agency’s prime contractor for Orion. Engineers who have sought to reduce the crew module’s overall weight have encountered and overcome technical challenges.
“When you look at the Orion crew module for EM-1 from the outside, it will look like the spacecraft we flew on Exploration Flight Test-1,” said Charlie Lundquist, Orion crew and service module manager. “But the spacecraft we’re building for our next mission incorporates a lot of engineering ingenuity and improved manufacturing processes. These improved processes have also contributed to a reduction in weight of the overall spacecraft.”
When the test version of Orion’s underlying structure was first constructed, it was heavy. The original conical section was made of six panels and six longerons (thin strips of metal) that required 12 welds to bind them together. Manufacturing the panels took considerable time. The welds also added considerable weight to ensure the seams were strong enough.
As engineers refined Orion’s design, building on lessons learned from constructing the initial test article and capsule for EFT-1, followed by diligent analysis and iterative design evaluations, engineers found ways to reduce the number of cone panels and welds, resulting in a needed weight reduction for EM-1.
But reducing the structure’s number of cone panels has required considerable resourcefulness and skill on the part of Orion’s engineering team.
When technicians began manufacturing the three new cone panels for EM-1, each comprising one-third of the circumference of the crew compartment and each made from a single piece of metal, they encountered an issue during the machining process. The large, curved panels had a tendency to flatten out or relax more than expected.
“When you form something from a six-inch thick metal plate, what holds it in shape is the metal itself,” said Jim Bray, Orion crew module director for Lockheed Martin. “When you need it to bend even more, but start to remove metal from it, and make it thinner, it starts to lose its shape.”
The Orion team knew the relaxation of the panels posed a threat to the manufacturing process and to Orion’s schedule, so they developed a new plan to keep the process on track.
Engineers first standardized the technical steps to make the pieces to exact specifications and divided manufacturing of the three panels among three different expert machining companies. The revised plan enabled unprecedented collaboration across the industry while working on all three panels in parallel, ultimately saving time.
“The modifications didn’t end with the machining techniques,” said Bray. “We also had to make sure the actual welding process would perform as expected on these new pieces.”
Engineers had to redefine the specific conditions under which welding operations must occur. These included the temperature and humidity in the room, the rotational speed of the weld head and how quickly it moves to join two pieces of metal.
This revised cone panel process isn’t the only weight-saving measure being incorporated into future Orion Crew Modules. Besides the reduced number of pieces and welds making up the pressure vessel, Orion’s thermal protection system, which protects the spacecraft during its extremely hot and fast reentry through Earth’s atmosphere, will be approximately 1,200 pounds lighter during EM-1 than it was during its maiden voyage to space. When completed, the crew module will be approximately 20 percent (4,000 pounds) lighter than it was during EFT-1.
Technicians will perform two final welds to integrate the other elements of the primary structure. After completion, it will be shipped to NASA’s Kennedy Space Center in Florida, where it will be outfitted and processed in preparation for its launch atop the agency’s Space Launch System (SLS) rocket. Boosted by the power of the SLS rocket, Orion will travel farther into deep space than a spacecraft built to carry humans has ever been.
-
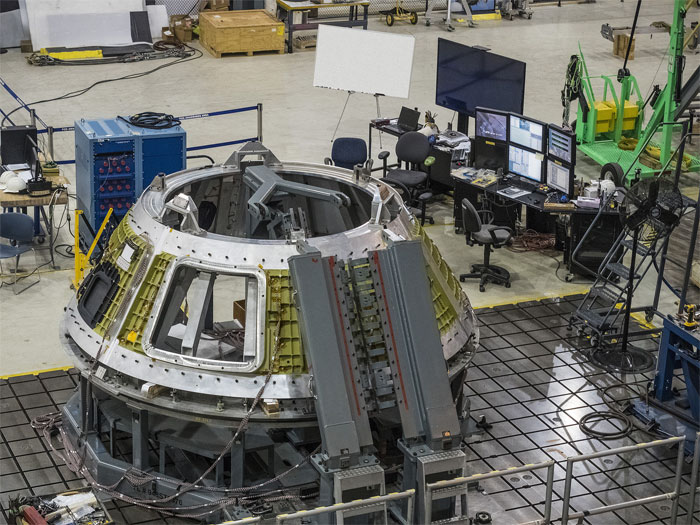
Technicians with Lockheed Martin, NASA’s prime contractor for Orion, are welding together the pieces of the spacecraft's pressure vessel at Michoud Assembly Center in New Orleans.
-
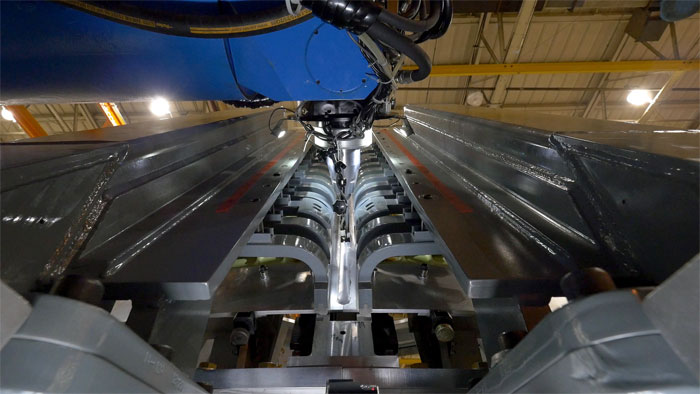
At NASA’s Michoud Assembly Facility in New Orleans, engineers used large tooling structures to help them weld together Orion’s cone panels using a process called friction-stir welding.
Quelle: NASA
-
Update: 20.11.2015
.
Engineers Refine Thermal Protection System for Orion’s Next Mission
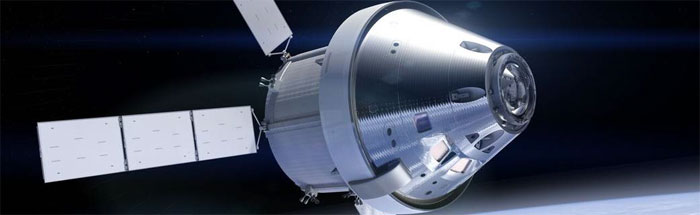
When it comes to a spacecraft enduring the extremely hot and fast journey from deep space back to Earth, NASA’s Orion can withstand the heat. Engineers developing Orion’s thermal protection system have been improving the spacecraft’s heat shield design and manufacturing process since the vehicle successfully traveled to space for the first time last year. They are now enhancing the overall system in advance of the spacecraft’s next mission – a flight that will put Orion through the harshest set of conditions yet.
Orion’s thermal protection system is one of the most critical parts of the spacecraft and is responsible for protecting it and the future astronauts it will carry home from deep space destinations. It consists of the spacecraft’s main heat shield that faces into the atmosphere on reentry to slow the spaceship down and also the grid of tiles known as the back shell. During Orion’s next mission atop the agency’s Space Launch System rocket, called Exploration Mission-1 (EM-1), the spacecraft will be in space for more than three weeks and return to Earth under even faster and hotter conditions than during its last flight.
“Orion’s thermal protection system is essential to successful future missions,” said John Kowal, NASA’s thermal protection system lead for Orion. “As we move toward building the system for EM-1, we’ve been able to take advantage of what we learned from building and flying Orion to refine our processes going forward.”
During EM-1, Orion will endure a more intense re-entry environment. While the spacecraft encountered speeds of 30,000 feet per second during Exploration Flight Test-1 and temperatures of approximately 4,000 degrees Fahrenheit, it will experience a faster return from lunar velocity of about 36,000 feet per second. While the speed difference may seem subtle, the heating the vehicle sees increases exponentially as the speed increases. The work engineering teams across the country are doing prepares Orion’s heat shield to perform re-entry during any of missions planned near the moon or in high lunar orbit (NASA’s “Proving Ground”) in the coming years.
For these future Orion missions, a silver, metallic-based thermal control coating will also be bonded to the crew module’s thermal protection system back shell tiles. The coating, similar to what is used on the main heat shield, will reduce heat loss during phases when Orion is pointed to space and therefore experiencing cold temperatures, as well as limit the high temperatures the crew module will be subjected to when the spacecraft faces the sun. The coating will help Orion’s back shell maintain a temperature range from approximately -150 to 550 degrees Fahrenheit prior to entry and also will protect against electrical surface charges in space and during re-entry.
“You’re trying to hit this sweet spot because when you’re looking at the sun, you don’t want to get too hot, and then when you’re not looking at the sun and instead in darkness, you don’t want to lose all the heat that the spacecraft generates,” said Kowal.
Engineers have also refined the design in ways that improve the manufacturing process and reduce the mass of the spacecraft for the upcoming exploration missions. Instead of a monolithic outer layer, the heat shield will be made of approximately 180 blocks that can be made simultaneously with the other heat shield components to streamline the labor-and-time-intensive manufacturing process.
In addition, engineers have found ways to reduce the mass of the heat shield’s underlying structure, which is composed of a titanium skeleton and carbon fiber skin. Teams have optimized the thickness of the skeleton and the skin based on the pressures that different areas will experience during flight and reentry, adding more fidelity to the overall structure while allowing it to be lighter.
NASA’s prime contractor for Orion, Lockheed Martin, recently completed a heat shield manufacturing development unit that engineers will use to verify the improved manufacturing process before it is used on hardware for flight. Teams have already begun building Orion’s heat shield for EM-1.
Quelle: NASA
-
Update: 24.11.2015
.
Raumanzüge für Orion wurden in reduzierter Schwerkraft Umgebung getestet
.
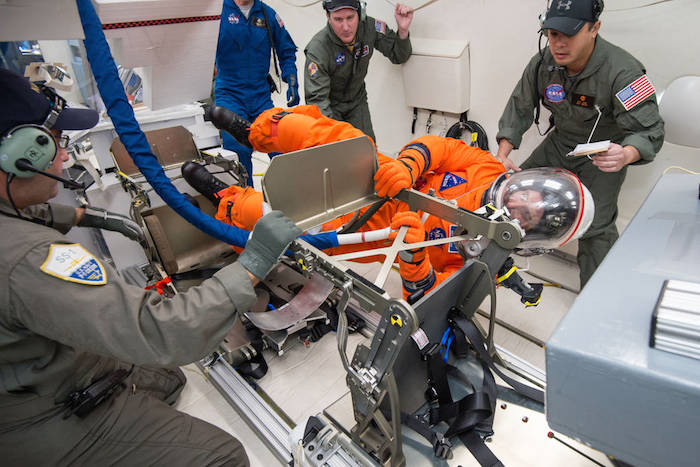
NASA is testing the spacesuits being developed for Orion on the agency’s C9 aircraft, which can fly a series of parabolas to simulate a weightless environment for brief periods. Engineers are using a mockup of Orion’s cabin in the aircraft to evaluate how astronauts can get into their seats during various operational scenarios, perform tasks at different suit pressures, and to test seat hardware. The suit, known as the Modified Advanced Crew Escape Suit, is an upgraded version of the launch and entry suits worn by space shuttle astronauts. The crew escape suit, along with Orion, will contain all the necessary functions to support life and is being designed to enable spacewalks and sustain the crew in the unlikely event the spacecraft loses pressure.
Quelle: NASA
5120 Views