.
NASA Administrator Charles Bolden Visits Northrop Grumman to View Space Agency's James Webb Space Telescope
REDONDO BEACH, Calif. – June 8, 2015 – NASA Administrator Charles Bolden visited Northrop Grumman Corporation's (NYSE:NOC) Redondo Beach facility May 28 to see the progress on the agency's James Webb Space Telescope. Northrop Grumman is under contract to NASA's Goddard Space Flight Center in Greenbelt, Maryland, and leads the industry team that designs and develops the Webb Telescope's optics, sunshield and spacecraft.
"When it launches in 2018, the James Webb Space Telescope will allow us to peer deeper into the universe than ever before. NASA's exploration spans the universe, and the people of Northrop Grumman are great partners in our work to extend humanity's reach into space while strengthening America's leadership here on Earth," Bolden said.
Bolden addressed Redondo Beach Space Park Facility employees working on the Webb Telescope, personally thanking them for their effort and taking questions on a variety of topics.
"We are proud to be a partner, leading the industry team responsible for building NASA's next great observatory," said Tom Vice, corporate vice president and president, Northrop Grumman Aerospace Systems. "We share a deep appreciation for science, which is incredibly important to our future and under NASA's leadership the James Webb Space Telescope will inspire future generations of scientists and engineers. Administrator Bolden's presence today reinforces the necessity of space exploration and leading the way to the frontiers of space."
Hosted by Vice and Scott Willoughby, vice president and James Webb Space Telescope program manager, Northrop Grumman, Bolden saw the spacecraft's backplane, its sunshield, the spacecraft bus and the cryocooler for the telescope's Mid-Infrared Instrument. The backplane holds the spacecraft's hexagonal mirrors that will give this unique telescope an aperture of 6.5 meters. The backplane will be shipped in August to Goddard Spaceflight Center for the integration of the 18 mirrors. The sunshield, which is nearly the size of a tennis court, is responsible for shielding the telescope from sunlight. The tour also included viewings of the spacecraft bus, which will take the telescope to its ultimate destination 1 million miles from Earth and the cryocooler for the telescope's Mid Infrared Instrument (MIRI). The cryocooler will chill MIRI to a temperature just barely above absolute zero.
The James Webb Space Telescope is the world's next-generation space observatory and successor to the Hubble Space Telescope. The most powerful space telescope ever built, the Webb Telescope will observe the most distant objects in the universe, provide images of the first galaxies formed and see unexplored planets around distant stars. The Webb Telescope is a joint project of NASA, the European Space Agency and the Canadian Space Agency.
Quelle: Northrop-Grumman
-
Update: 25.06.2015
.
NASA Technology Protects Webb Telescope from Contaminatio
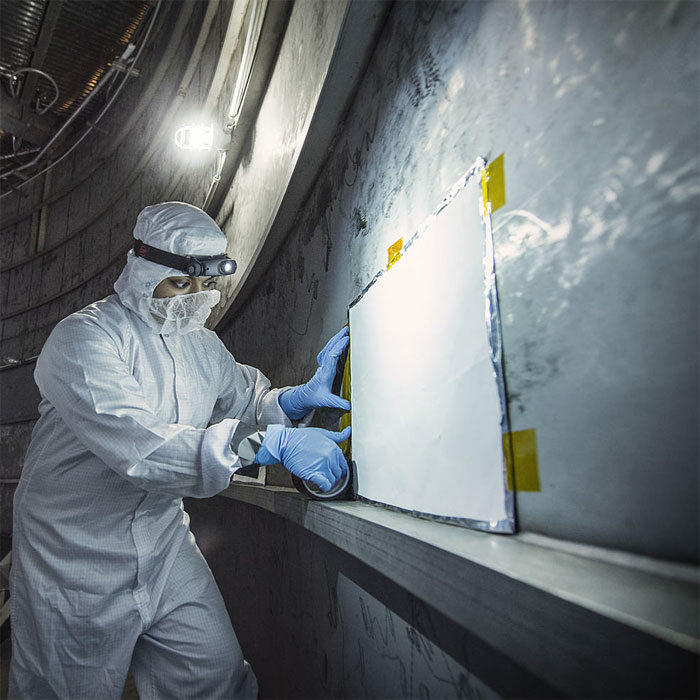
Thermal Coatings Engineer Nithin Abraham places a MAC panel at the very bottom of the Chamber A where the Webb telescope will be tested.
Credits: NASA/Chris Gunn
-
Contamination from organic molecules can harm delicate instruments and engineers are taking special care at NASA to prevent that from affecting the James Webb Space Telescope (and all satellites and instruments). Recently, Nithin Abraham, a Thermal Coatings Engineer placed Molecular Adsorber Coating or "MAC" panels in the giant chamber where the Webb telescope will be tested.
This contamination can occur through a process when a vapor or odor is emitted by a substance. This is called "outgassing." The "new car smell" is an example of that, and is unhealthy for people and sensitive satellite instruments. So, NASA engineers have created a new way to protect those instruments from the damaging effects of contamination coming from outgassing.
"The Molecular Adsorber Coating (MAC) is a NASA Goddard coatings technology that was developed to adsorb or entrap outgassed molecular contaminants for spaceflight applications," said Nithin Abraham, Thermal Coatings Engineer at NASA's Goddard Space Flight Center in Greenbelt, Maryland. MAC is currently serving as an innovative contamination mitigation tool for Chamber A operations at NASA Johnson Space Center in Houston, Texas.
MAC can be used to keep outgassing from coming in from outside areas or to capture outgassing directly from hardware, components, and within instrument cavities.
In this case, MAC is helping by capturing outgassed contaminants outside the test chamber from affecting the Webb components. MAC is expected to capture the outgassed contaminants that exist in the space of the vacuum chamber (not from the Webb components).
"Although we cannot stop contaminants within the vacuum chamber from outgassing, we can try to capture them with MAC before it tries and reaches the expensive hardware, which are housed inside the test chamber," Abraham said.
In May 2015, several test panels spray coated with MAC were custom designed and fabricated for use in Chamber A in preparation for the arrival of the James Webb Space Telescope's first Optical Ground Support Equipment (OGSE-1).
"The MAC panels were installed in very strategic locations within Chamber A to capture vacuum chamber contamination originating from persistent sources, such as silicone pump oil residue and hydrocarbons," Abraham said.
Some silicone based contaminants are known to outgas and spread easily, even at ambient temperatures, and are extremely difficult to remove and clean. The use of MAC panels during the OGSE-1 test would lower the contamination risk and prevent these harmful outgassed components from migrating and depositing onto highly sensitive Webb telescope optical hardware surfaces during testing.
The walls of the chamber have a matte finish, which give them the ironic appearance of looking unclean, since keeping contaminants out is critical. Some areas in the chamber also have markings which indicate where there's been rubbing from a tool that has slightly burnished the surface.
The new, patent-pending sprayable paint that adsorbs these gaseous molecules and stops them from affixing to instrument components was created by a team at NASA's Goddard Space Flight Center in Greenbelt, Maryland. Made of zeolite, a mineral widely used in industry for water purification and other uses, and a colloidal silica binder that acts as the glue holding the coating together, the new molecular adsorber is highly permeable and porous — attributes that trap the outgassed contaminants.
Webb will be tested in "Chamber A," the thermal-vacuum test facility at NASA's Johnson Space Center in Houston, Texas. Chamber A is now the largest high-vacuum, cryogenic-optical test chamber in the world, and made famous for testing the space capsules for NASA's Apollo mission, with and without the mission crew. It is 55 feet (16.8 meters) in diameter by 90 feet (27.4 meters) tall. The door weighs 40 tons and is opened and closed hydraulically.
Webb is an international project led by NASA with its partners the European Space Agency and the Canadian Space Agency.
The James Webb Space Telescope is the successor to NASA's Hubble Space Telescope. It will be the most powerful space telescope ever built.
Quelle: NASA
-
Update: 28.07.2015
-
Round of Testing Completed on Webb Telescope Flight Mirrors
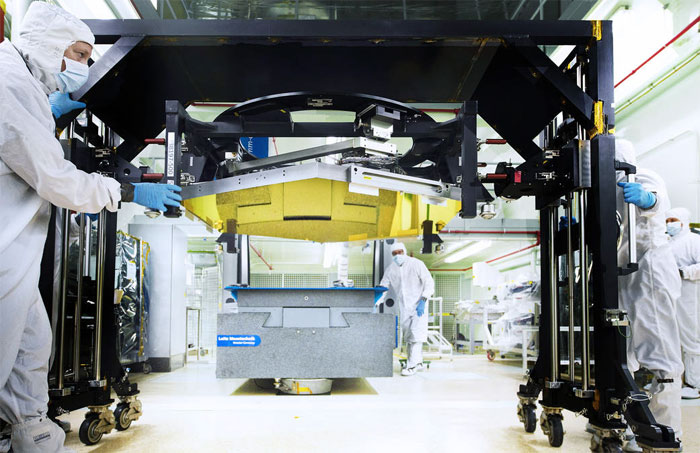
This July 11, 2015 photograph captures one of the final, if not the final, James Webb Space Telescope flight primary mirror segments to be processed through NASA Goddard Space Flight Center's Calibration, Integration and Alignment Facility (CIAF).
The mirror is seen here on the Configuration Measurement Machine (CMM), which is used for precision measurements of the backs of the mirrors. These precision measurements must be accurate to 0.1 microns or 1/400th the thickness of a human hair.
The James Webb Space Telescope is the scientific successor to NASA's Hubble Space Telescope. It will be the most powerful space telescope ever built. Webb is an international project led by NASA with its partners, the European Space Agency and the Canadian Space Agency.
Image Credit: NASA/Chris Gunn
Last Updated: July 28, 2015
Quelle: NASA
.
Update: 12.08.2015
.
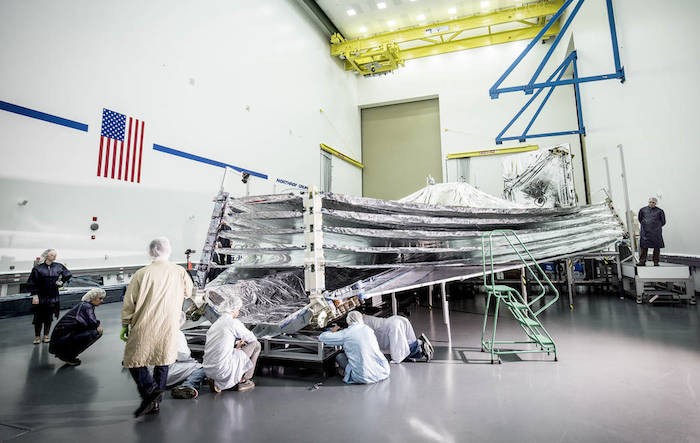
The sunshield on NASA's James Webb Space Telescope is the largest part of the observatory—five layers of thin, silvery membrane that must unfurl reliably in space. The precision in which the tennis-court sized sunshield has to open must be no more than a few centimeters different from its planned position.
In this photo, engineers and scientists examine the sunshield layers on this full-sized test unit.
Because there's a layer of the shiny silver material on the base under the five layers of the sunshield, it appears as if the sunshield has a mouth that is "open wide" while engineers take a look. The photo was taken in a clean room at Northrop Grumman Corporation, Redondo Beach, California.
The sunshield separates the observatory into a warm sun-facing side and a cold side where the sunshine is blocked from interfering with the sensitive infrared instruments. The infrared instruments need to be kept very cold (under 50 K or -370 degrees Fahrenheit) to operate. The sunshield protects these sensitive instruments with an effective sun protection factor, or SPF, of 1,000,000. Sunscreen generally has an SPF of 8 to 50.
In addition to providing a cold environment, the sunshield provides a thermally stable environment. This stability is essential to maintaining proper alignment of the primary mirror segments as the telescope changes its orientation to the sun.
Earlier this year, the first flight layer of the sunshield was delivered to Northrop Grumman. Northrop Grumman is designing the Webb Telescope’s sunshield for NASA’s Goddard Space Flight Center, in Greenbelt, Maryland. Innovative sunshield membranes are being designed and manufactured by NeXolve Corporation of Huntsville, Alabama.
The James Webb Space Telescope is the successor to NASA's Hubble Space Telescope. It will be the most powerful space telescope ever built. Webb is an international project led by NASA with its partners, the European Space Agency and the Canadian Space Agency.
Quelle: NASA
-
Update: 27.08.2015
.
Northrop Grumman Delivers Telescope Structure for NASA's James Webb Space Telescope
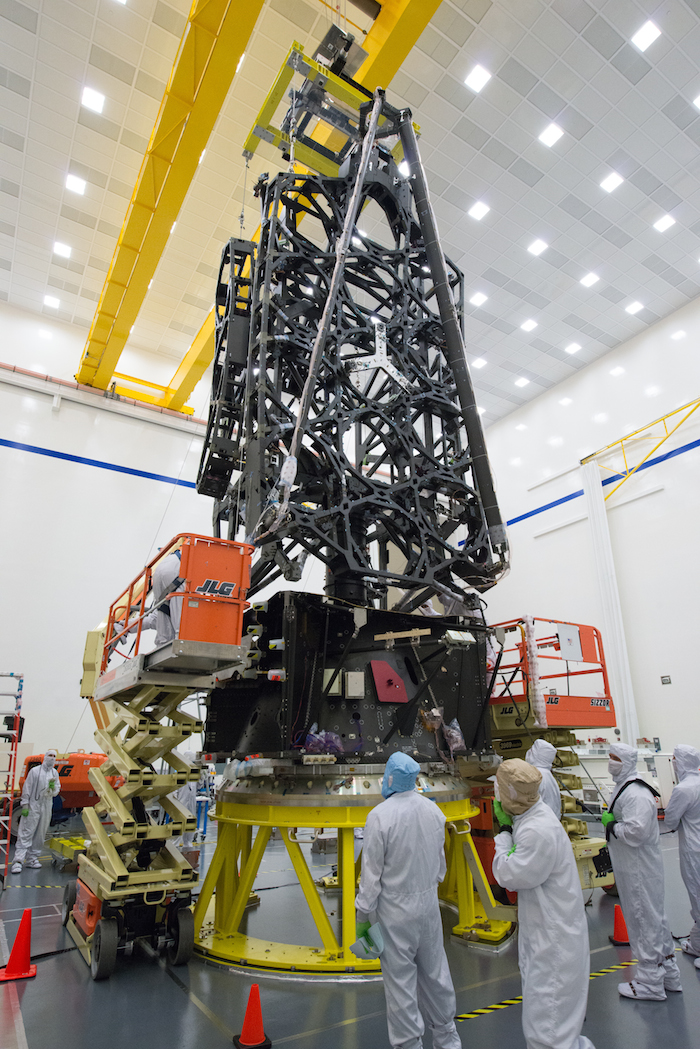
Northrop Grumman Corporation (NOC) delivered on schedule the telescope structure for NASA's James Webb Space Telescope Aug. 24 to Goddard Space Flight Center in Greenbelt, Maryland, paving the way for the integration of the 18 hexagonal mirrors that will help scientists observe the formation of the first stars and galaxies over 13.5 billion years ago.
Northrop Grumman is under contract to NASA's Goddard Space Flight Center and leads the industry team that designs and develops the Webb Telescope, its sunshield and spacecraft. Northrop Grumman has completed the integration and testing of the telescope structure, which holds optical assemblies of the telescope including its instruments and mirrors.
"The telescope's beryllium mirrors are held together nearly motionlessly in space by the telescope structure, which also acts as a stable platform during ground test operations and launch," said Scott Texter, telescope manager, Northrop Grumman Aerospace Systems. "The stability of this hardware contributes to the Webb Telescope's ability to provide an unprecedented look at our own solar system as well as discover exoplanets well beyond this solar system."
The highly efficient telescope structure will also meet first-time thermal stability requirements to minimize thermal distortion. While the telescope is operating at a range of extremely cold temperatures as low as 389 degrees below Fahrenheit, the backplane portion of the telescope structure must not vary more than 38 nanometers (approximately a thousandth the diameter of a human hair). Additionally, the breakthrough folding design of the transformer-like telescope structure enables it to fit inside the 15-foot-diameter fairing of the launch vehicle.
The Webb Telescope's secondary mirror support structure and deployable tower assembly (DTA) also contribute to how the telescope and instruments fit into the rocket fairing in preparation for launch. The graphite DTA was designed, built and tested by Astro Aerospace, a Northrop Grumman company. Additionally, the DTA is responsible for lifting the telescope mirrors and instruments away from the heat of the main spacecraft after deployment.
Completing and delivering the structure to NASA marks an important milestone in the journey of the Webb Telescope, which is the world's next-generation space observatory and successor to the Hubble Space Telescope. The Webb Telescope, the most powerful space telescope ever built, will observe the most distant objects in the universe, provide images of the first galaxies formed and see unexplored planets around distant stars. The Webb Telescope is a joint project of NASA, the European Space Agency and the Canadian Space Agency.
Northrop Grumman is a leading global security company providing innovative systems, products and solutions in unmanned systems, cyber, C4ISR, and logistics and modernization to government and commercial customers worldwide. Please visit www.northropgrumman.com for more information.
Quelle: Northrop Grumman
-
Update: 31.08.2015
.
James Webb Space Telescope - the Flight Telescope Structure
Just arrived at NASA Goddard - the flight telescope structure of the James Webb Space Telescope. This is like the "bones" of the telescope - it will hold the mirrors and the instruments. It is at NASA Goddard for this assembly. The long struts to the left are the boom that holds the secondary mirror. The whole structure is folded up in a similar configuration to how it will look in the rocket for launch.
.
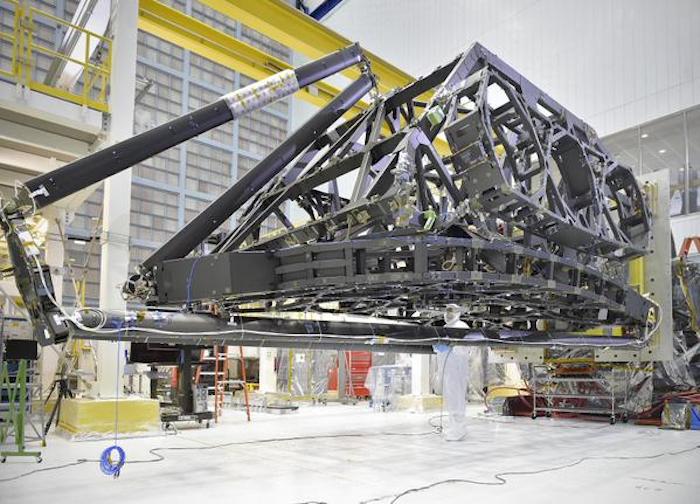
-
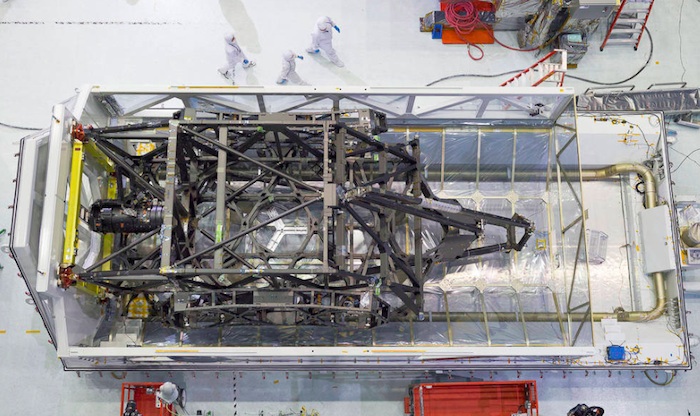
-
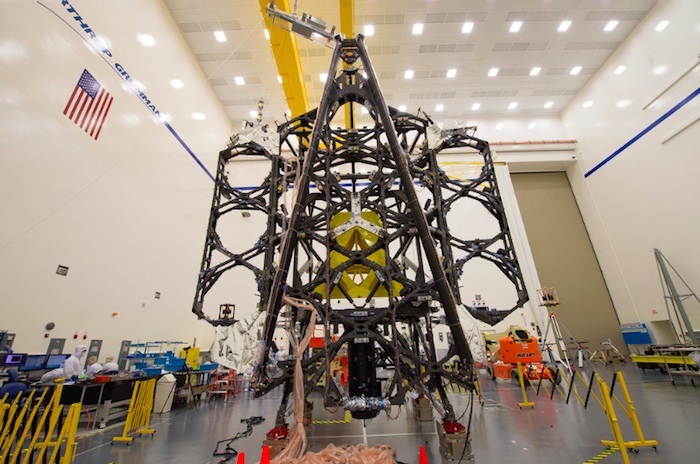
-

-
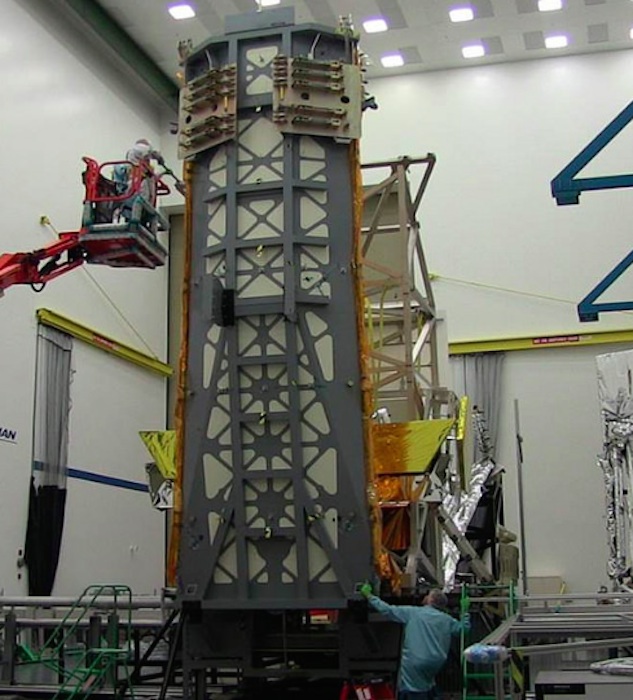
-
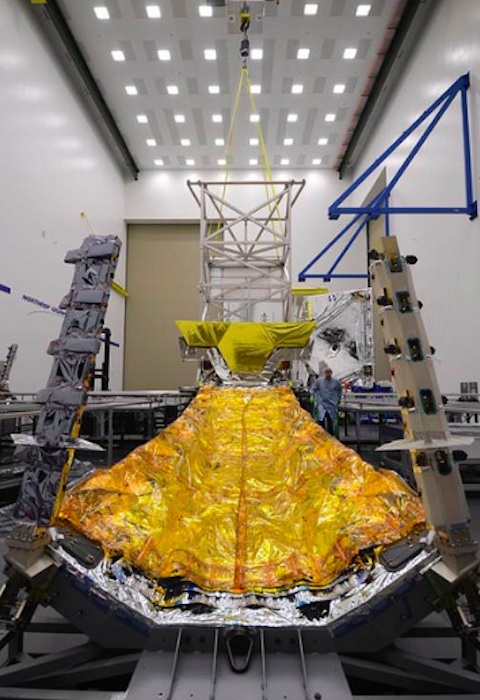
Quelle: NASA
-
Update: 4.09.2015
.
NASA Webb Telescope
The long booms on the front of the #JWST telescope structure will hold our secondary mirror
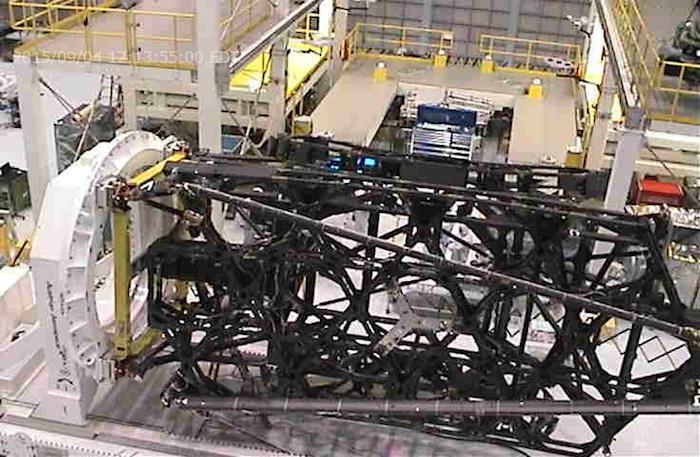
Quelle: NASA
-
Update: 9.09.2015
.
The Secrets of NASA's Webb Telescope’s "Deployable Tower Assembly"
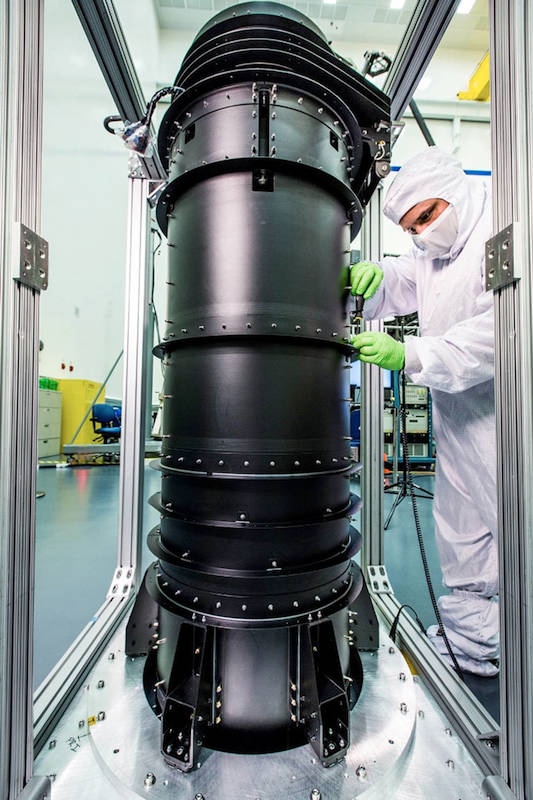
Recently, engineers at Northrop Grumman Corporation in Redondo Beach, California were testing the DTA to ensure it worked properly.
Credits: Northrop Grumman Corp.
.
Building a space telescope to see the light from the earliest stars of our universe is a pretty complex task. Although much of the attention goes to instruments and the giant mirrors on NASA's James Webb Space Telescope, there are other components that have big jobs to do and that required imagination, engineering, and innovation to become a reality.
For example, engineers working on the Webb telescope have to think of everything from keeping instruments from overheating or freezing, to packing up the Webb, which is as big as a tennis court, to fit inside the rocket that will take it to space. Those are two areas where the "DTA" or Deployable Tower Assembly (DTA) plays a major role.
The DTA looks like a big black pipe and is made out of graphite-epoxy composite material to ensure stability and strength with extreme changes in temperature like those encountered in space. When fully deployed, the DTA reaches ten feet in length.
The DTA interfaces and supports the spacecraft and the telescope structures. It features two large nested telescoping tubes, connected by a mechanized lead screw. It is a deployable structure that is both very light and extremely strong and stable.
The Webb telescope’s secondary mirror support structure and DTA contribute to how the telescope and instruments fit into the rocket fairing in preparation for launch. The DTA allows the Webb to be short enough when stowed to fit in the rocket fairing with an acceptably low center of gravity for launch.
Several days after the Webb telescope is launched, the DTA will deploy, or separate, the telescope mirrors and instruments from the spacecraft bus and sunshield. This separation allows the sunshield to unfurl and shade the telescope and instruments from radiant heat and stray light from the sun and Earth.
The DTA was designed, built and tested by Astro Aerospace - a Northrop Grumman Company, in Carpinteria, California.
The James Webb Space Telescope is the scientific successor to NASA's Hubble Space Telescope. It will be the most powerful space telescope ever built. The Webb telescope is an international project led by NASA with its partners, the European Space Agency and the Canadian Space Agency.
Quelle: NASA
-
Update: 9.10.2015
.
Northrop Grumman Team Successfully Completes Manufacturing of Optical Class Spacecraft Structure for NASA's James Webb Space Telescope
Manufacturing and assembly of the spacecraft structure that will take NASA's James Webb Space Telescope to its ultimate destination 1 million miles from Earth was successfully completed July 1 at Northrop Grumman Corporation's (NOC) Redondo Beach facility. Northrop Grumman is working with NASA's Goddard Space Flight Center in Greenbelt, Maryland, and leads the industry team that designs and develops the Webb Telescope's optics, sunshield and spacecraft.
The spacecraft structure, or bus, is made of carbon fiber composites and houses the spacecraft's propulsion, electrical power and communications. The bus must withstand a force equivalent to 45 tons while supporting the observatory during launch.
While in orbit the spacecraft structure will provide pointing and structural stability for the telescope down to one arcsecond. The structure also provides dynamic isolation and attenuation of vibration sources down to two milliarcseconds. This level of image stabilization is equivalent to shining a laser beam from Los Angeles to New York City, with less than 1.5 inches of motion.
The spacecraft structure integrates the system's optical telescope, sunshield, and instrument electronics and mounts the whole observatory to the Ariane 5 rocket — tasked with launching the Webb Telescope to its destination in space. To launch such a large observatory out to the L2 orbit 1 million miles away, the structure must also be very light-weight so its mass efficiency allows it to carry 64 times its own weight.
"The spacecraft structure provides state of the art capabilities to support the James Webb Space Telescope's first light mission," said Andy Cohen, manager, Webb Telescope spacecraft, Northrop Grumman Aerospace Systems. "Completing the manufacturing and assembly of the spacecraft structure was a significant achievement by many dedicated and diligent people. This milestone represents the committed collaboration between the spacecraft structure's manufacturing, engineering, integration and test teams. It also signifies the continuing progress on the Webb Telescope, and will culminate with the structure test, propulsion integration completion and delivery to spacecraft Integration and Test by July 2016."
The James Webb Space Telescope is the world's next-generation space observatory and successor to the Hubble Space Telescope. The most powerful space telescope ever built, the Webb Telescope will observe the most distant objects in the universe, provide images of the first galaxies formed and see unexplored planets around distant stars. The Webb Telescope is a joint project of NASA, the European Space Agency and the Canadian Space Agency.
Northrop Grumman is a leading global security company providing innovative systems, products and solutions in unmanned systems, cyber, C4ISR, and logistics and modernization to government and commercial customers worldwide
Quelle: Northrop Grumman
---
NASA Webb Telescope Construction Leaps Forward with Delivery of Mirror Holding Backbone Flight Structure
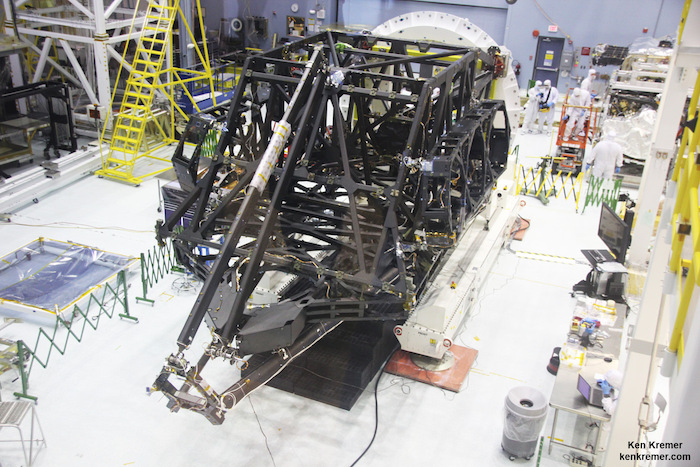
View showing actual flight structure of mirror backplane unit for NASA’s James Webb Space Telescope (JWST) that holds 18 segment primary mirror array and secondary mirror mount at front, in stowed-for-launch configuration. JWST is being assembled here by technicians inside the world’s largest cleanroom at NASA Goddard Space Flight Center, Greenbelt, Md. Credit: Ken Kremer/kenkremer.com
-
NASA GODDARD SPACE FLIGHT CENTER, MD – The construction pace for NASA’s James Webb Space Telescope (JWST) took a major leap forward with delivery of the actual flight structure that serves as the observatory’s critical mirror holding backbone – to NASA’s Goddard Space Flight Center in Greenbelt, Maryland and observed by Universe Today.
“We are in good shape with the James Webb Space Telescope,” said Dr. John Mather, NASA’s Nobel Prize Winning scientist, in an exclusive interview with Universe Today at NASA Goddard during a visit to the flight structure – shown in my photos herein.
And the mammoth $8.6 Billion Webb telescope has mammoth scientific objectives as the scientific successor to NASA’s Hubble Space Telescope (HST) – now celebrating its 25th anniversary in Earth orbit.
“JWST has the capability to look back towards the very first objects that formed after the Big Bang,” Mather told Universe Today.
How is that possible?
“James Webb has a much bigger mirror than Hubble. So its resolution is much better,” said astronaut and NASA science chief John Grunsfeld, during an exclusive interview at NASA Goddard. Grunsfeld flew on a trio of Hubble servicing missions aboard the Space Shuttle, including the final one during STS-125 in 2009.
“JWST can look back further in time, and a greater distance than Hubble, so we can see those first stars and galaxies formed in the Universe.”
These discoveries are only possible with Webb, which will become the most powerful telescope ever sent to space when it launches in 2018.
The massive JWST flight structure unit includes the “backplane assembly” that clasps in place all of the telescopes primary and secondary mirrors, as well as its ISIM science module loaded with the observatory’s quartet of state-of-the-art research instruments.
“The backplane looks really great,” Grunsfeld told me.
Numerous NASA centers and aerospace companies are involved in building the observatory and its backplane structure holding the mirrors that will search back some 13.4 billion years.
“The backplane structure just arrived in late August from Northrop Grumman Aerospace Systems in Redondo Beach, California,” said Sandra Irish, JWST lead structural engineer during an interview with Universe Today at the NASA Goddard cleanroom facility.
“This is the actual flight hardware.”
The purpose of JWST’s backplane assembly is to hold the telescopes 18 segment, 21-foot (6.5-meter) diameter primary mirror nearly motionless while floating in the utterly frigid space environment, thereby enabling the observatory to peer out into deep space for precise science gathering measurements never before possible.
The massive telescope structure “includes the primary mirror backplane assembly; the main backplane support fixture; and the deployable tower structure that lifts the telescope off of the spacecraft. The three arms at the top come together into a ring where the secondary mirror will reside,” say officials.
The backplane traveled a long and winding road before arriving at Goddard.
“The backplane structure was designed and built at Orbital ATK with NASA oversight,” Irish explained. The assembly work was done at the firms facilities in Magna, Utah.
“Then it was sent to Northrop Grumman in Redondo Beach, California for static testing. Then it came here to Goddard. Orbital ATK also built the composite tubes for the ISIM science module structure.”
The observatory’s complete flight structure measures about 26 feet (nearly 8 meters) from its base to the tip of the tripod arms and mirror mount holding the round secondary mirror.
The flight structure and backplane assembly arrived at Goddard in its stowed-for-launch configuration after being flown cross country from California.
“It is here for the installation of all the mirrors to build up the entire telescope assembly here at Goddard. It will be fully tested here before it is delivered to the Johnson Space Center in Houston and then back to California,” Irish elaborated.
The overall assembly is currently attached to a pair of large yellow and white fixtures that firmly secure the flight unit, to stand it upright and rotate as needed, as it undergoes acceptance testing by engineers and technicians before commencement of the next big step – the crucial mirror installation that starts soon inside the world’s largest cleanroom at NASA Goddard.
Overhead cranes are also used to maneuver the observatory structure as engineers inspect and test the unit.
But several weeks of preparatory work are in progress before the painstakingly precise mirror installation can begin under the most pristine cleanroom operating conditions.
“Right now the technicians are installing harnesses that we need to mount all over the structure,” Irish told me.
“These harnesses will go to our electronic systems and the mirrors in order to monitor their actuation on orbit. So that’s done first.”
What is the construction sequence at Goddard for the installation of the mirrors and science instruments and what comes next?
“This fall we will be installing every mirror, starting around late October/early November. Then next April 2016 we will install the ISIM science module inside the backplane structure.”
“The ISIM mounts all four of the telescope science instrument. So the mirrors go on first, then the ISIM gets installed and then it will really be the telescope structure.” ISIM carries some 7,500 pounds (2400 kg) of telescope optics and instruments.
“Then starting about next July/August 2016 we start the environmental testing.”
The actual flight mirror backplane is comprised of three segments – the main central segment and a pair of outer wing-like parts holding three mirrors each. They will be unfolded from the stowed-for-launch configuration to the “deployed” configuration to carry out the mirror installation. Then be folded back over into launch configuration for eventual placement inside the payload fairing of the Ariane V ECA booster rocket.
The telescope will launch from the Guiana Space Center in Kourou, French Guiana in 2018.
The telescopes primary and secondary flight mirrors have already arrived at Goddard.
The mirrors must remained precisely aligned and nearly motionless in order for JWST to successfully carry out science investigations. While operating at extraordinarily cold temperatures between -406 and -343 degrees Fahrenheit the backplane must not move more than 38 nanometers, approximately 1/1,000 the diameter of a human hair.
To account for the tiniest of errors and enhance science, each of the primary mirrors is equipped with actuators for minute adjustments.
“A beautiful advantage of Webb that’s different from Hubble is the fact that we do have actuation [capability] of every single one of our mirrors. So if we are off by just a little bit on either our calculations or from misalignment from launch or the zero gravity release, we can do some fine adjustments on orbit.”
“We can adjust every mirror within 50 nanometers.”
“That’s important because we can’t send astronauts to fix our telescope. We just can’t.”
“The telescope is a million miles away.”
NASA’s team at Goddard has already practiced mirror installation because there are no second chances.
“We only have one shot to get this right!” Irish emphasized.
Watch for more on the mirror installation in my upcoming story.
JWST is the successor to the 25 year old Hubble Space Telescope and will become the most powerful telescope ever sent to space.
Webb is designed to look at the first light of the Universe and will be able to peer back in time to when the first stars and first galaxies were forming.
The Webb Telescope is a joint international collaborative project between NASA, the European Space Agency (ESA) and the Canadian Space Agency (CSA).
NASA has overall responsibility and Northrop Grumman is the prime contractor for JWST.
“The telescope is on schedule for its launch in 2018 in October,” Mather told me.
And the payoff from JWST will be monumental!
“On everything from nearby planets to the most distant universe, James Webb will transform our view of the Universe,” Grunsfeld beams.
Watch for more on JWST construction and mirror installation in part 2 soon.
Quelle: UT
5623 Views