.
The XCOR Lynx Mark I vehicle being fabricated at the Mojave Air and Space Port in Mojave, Calif. Photo: Mike Massee / XCOR Aerospace
.
XCOR Aerospace proudly announced continued progress on its Lynx spaceplane, a suborbital spacecraft designed to take humans and payloads to the edge of space. The Lynx strakes, a major portion of the Lynx aerodynamic shell, were successfully bonded to the fuselage of the Lynx Mark I spacecraft on April 30, marking a major milestone for the company as they can now begin the electric wiring and installing process on the Lynx reusable launch vehicle (RLV).
The Lynx is the company’s two-seat, piloted space transport vehicle and its entry into the competitive commercial RLV market. Lynx will take off and land horizontally, like an aircraft, but instead of a jet or piston engine the Lynx will use its own reusable rocket propulsion system of four XR-5K18 engines to safely depart and return on a runway. The vehicle will take humans and payloads on a 30-minute journey to the edge of space, topping out at 330,000 feet (100 km).
.
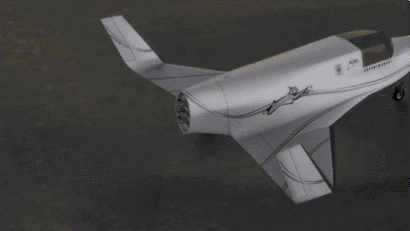
Four XR-5K18 rocket engines will power XCOR’s Lynx launch vehicles. Credit: XCOR Aerospace
.
The first XCOR Lynx suborbital vehicle is currently undergoing production at XCOR Aerospace Hangar 61 in Mojave, Calif. The 10,375-square-foot hangar houses their team of more than fifty skilled employees at the Mojave Air and Space Port. Rapid development on the Lynx Mark I spacecraft means that the company is coming closer and closer to Lynx full assembly and first flight. The vehicle will take a pilot and a participant to the edge of space and provide inexpensive suborbital launch services to numerous markets. The Lynx Mark I is the company’s initial flight test vehicle and is expected to begin a flight test program later this year.
The integration of the strakes to the Lynx Mark I spacecraft marks a big step toward final vehicle assembly for the growing aerospace company.
“Today marks another solid milestone in our progress toward first flight, clearing the path for a series of important moments that will accelerate Lynx development,” said XCOR President and Chief Executive Officer Jay Gibson.
Each strake is subdivided into four separate fuel tanks. They are pressurized during flight and provide the engines with a combustible hydrocarbon liquid used in jet engines called kerosene. Two reaction control thrusters and a main landing gear assembly are stored inside each strake. The lynx will use the reaction control thrusters while it is out of the atmosphere and making altitude changes.
Now that the strakes are successfully bonded to the vehicle, Chief Technology Officer Jeff Greason described the next steps for Lynx development: “We have an open path toward the integration of a number of subsystems, and this means we will now start electrical wiring, plumbing, installing the control system, and populating the landing gear bays.”
Last December, just five months ago, XCOR reached a significant milestone after it bonded the cockpit and the carry-through spar on to the back end of the Lynx fuselage. This crucial step had to be completed before the strakes were to be attached.
In order to carefully place the spar, the Lynx rocket truss was removed from its test stand and placed on the vehicle. Composite technicians worked tirelessly to perfectly align the spar and bond it in place.
“The carry-through spar is the heart of the loading structure on any winged craft – it supports the primary load of the wings and carries that load through the fuselage,” explained Jeff Greason. “Attaching the spar on a composite vehicle is a one-way operation, so it has to be done right the first time.”
.
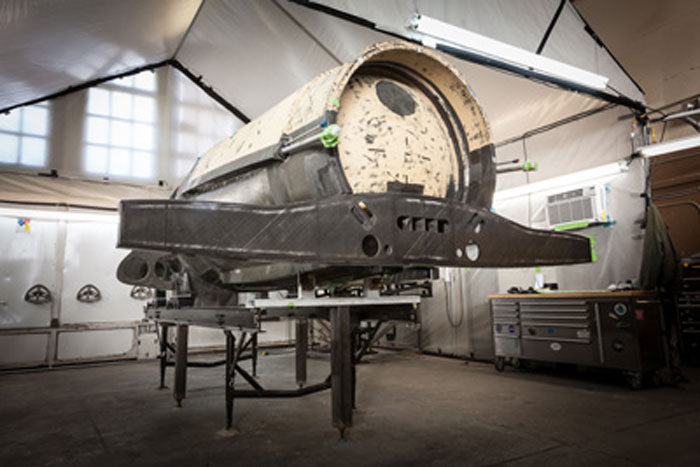
The fuselage and cockpit with carry-through spar mounted. Photo Credit: XCOR Aerospace
.
The entire structure was put under a pressure test after the spar was successfully installed. It experienced pressure equivalent to a 6 g re-entry with the cabin pressured to 11 PSI.
The XCOR Lynx RLV is unique in many aspects. Unlike vertical rocket launches and air-launched rocket vehicles, the aircraft-like abilities allow for much more flexibility and re-use. The Lynx will provide up to four flights per day from a licensed spaceport with a 2,400-meter (7,900-ft) runway. It will have a quick turnaround of just two hours and go on 40 flights before needing routine maintenance. It will be affordable to operate and maintain and be heavily focused on providing safe and reliable flights to space.
An all-composite airframe makes the Lynx lightweight and incredibly sturdy. It is able to withstand the fiery re-entry from space because it is protected by a thermal protection system (TPS) on its nose and leading edges. Its wing area is structured for landing at average speeds around 90 knots. The entire spacecraft measures to be about 9 meters (~30 ft) in length with a double-delta wing, stretching out to a wide 7.5 meters (~24 ft) in length.
XCOR has several models of Lynx production vehicles that each serves a particular set of needs and/or markets.
The Lynx Mark I, as described above, is the prototype test vehicle currently under development at XCOR Aerospace Hangar 61. It will be used to test the various sub-systems within the aircraft such as structure, aeroshell, tanks, life support, propulsion, aerodynamics, and re-entry heating. It is designed to reach an altitude of 200,000 feet (~61 km). Eventually Lynx Mark I will be used to train pilots and crew for the Lynx Mark II.
The Lynx Mark II is designed to service both the space tourism market and markets that will utilize the payload capacity for microgravity research and experiments. The Mark II uses the same propulsion and avionics systems as its predecessor (Mark I) but give higher performance because of its lower dry weight. This vehicle has a lightweight composite LOX tank and other key components that are exclusive to the company. It is designed to fly up to 328,000 feet (~100 km) and take payloads and participants on suborbital trips to the edge of space.
Passengers can hitch an out-of-this-world experience aboard the Lynx for $95,000 a flight. Prior to the flight, participants will go through medical screenings, seminars, and g-force training to familiarize them with the suborbital spaceflight experience. The participant will sit to the right of the pilot inside the pressurized cabin and wear a pressure suit for added safety. Pilot and passenger will take off from a runway into the black sky. They will view the curvature of Earth and enjoy about 4.6 minutes in microgravity at apogee (328,000 ft). The spaceplane will then descend to lower altitudes and land on the same runway it took off from.
The Lynx Mark III is a more advanced version of the Mark II. It comes with the capability to carry an external dorsal pod with a total payload capacity of 650kg. The pod can host either a payload research experiment or an upper stage to launch a satellite into low earth orbit (LEO). The Mark III encompasses upgraded landing gear, aerodynamics, core structural improvements, and more, over the Mark II. The Lynx Mark III features a power-packed propulsion package to transport heavier payloads into space.
Four XR-5K18 rocket engines will power XCOR’s Lynx launch vehicles, each producing 12.9 kN (2900 lbf) thrust by burning a concoction of liquid oxygen and kerosene. The first hot fire of this rocket engine was in December 2008 and continues to be tested today.
XCOR is currently building a Research and Development Center in Midland, Texas, at Midland International Airport. The aerospace company plans on opening an operational and manufacturing site at NASA’s Kennedy Space Center in Florida, with the aid of Space Florida.
Quelle: AS
4671 Views