.
10.03.2015
When NASA’s heavy-lift Space Launch System (SLS) rocket launches the agency’s Orion deep-space crew capsule for the first time in late 2018, it will mark the beginning of a new chapter in America’s human spaceflight efforts, aiming for destinations beyond low-Earth orbit (LEO) for the first time in four decades by employing the largest and most powerful launch vehicle mankind has ever created. The colossal 321-foot-tall SLS will thunder toward space on the power of four former (upgraded) liquid-fueled space shuttle RS-25 engines, but even with a combined thrust of nearly 2.5 million pounds those four engines alone won’t be enough to provide the 70-metric-ton (77-ton) lift capacity the initial SLS configuration promises.
The rocket needs more power at launch to make NASA’s ambitious deep-space human exploration plans a reality, and this Wednesday, at 9:30 a.m. MDT (11:30 a.m. EDT), Orbital ATK is expected to test fire the largest and most powerful solid rocket booster ever built to help get the job done.
Bookmark our “Launch and Events Tracker” to WATCH the test fire live!
The company’s 154-foot-tall, five-segment solid rocket booster (SRB) has been in development for years, having been initially designed to launch NASA’s Ares rockets for the agency’s cancelled Constellation program. The booster is similar to the four-segment SRBs that helped launch the space shuttle fleet, but it’s larger and incorporates several upgrades and improvements. Now, after a lengthy investigation and trouble-shooting effort to determine root cause(s) and corrective actions for the existence of small voids previously discovered between the propellant and outer casing of the booster’s aft segment, Orbital ATK is ready to move forward with their full-scale test fire of the company’s SLS booster test article, Qualification Motor-1 (QM-1).
“Years of extensive work and testing have gone into preparing us for this qualification test,” said Alex Priskos, manager of the SLS Boosters Office at NASA’s Marshall Space Flight Center. “We can’t stress enough what a big deal this is in preparing the rocket for flight.”
“Testing before flight is critical to ensure reliability and safety when launching crew into space,” said Charlie Precourt, vice president and general manager of the company’s Space Launch division. “The QM-1 static test is an important step in further qualifying this new five-segment solid rocket motor for the subsequent planned missions to send astronauts to deep space.”
Three fully developed, five-segment SRBs have been fired up on Orbital ATK’s Promontory, Utah, T-97 test stand since 2009, with the most recent having been conducted in 2011, and all performed fine. Those tests, known as the Development Motor test series (DM-1, DM-2, and DM-3), helped engineers measure the new SRB’s performance at low temperature, verify design requirements of new materials in the motor joints, and gather performance data about upgrades made to the booster since the shuttle program.
Once ignited the five-segment SLS booster will deliver an incredible 3.6 million pounds of thrust, which is equivalent to 22 million horsepower—each—and the SLS will employ two of the 1.6 million pound boosters (1.4 million is propellant) to help NASA’s future deep-space crew missions escape the pull of Earth’s gravity to reach destinations such as an asteroid and, eventually, Mars. The five-segment SLS boosters will burn for the same amount of time as the old shuttle boosters—two minutes—but they will provide 30 percent more power.
For Wednesday’s QM-1 test fire more than 500 instrumentation channels will be used to help evaluate over 100 defined test objectives, some of which are as follows:
Hot conditioned to upper limit for propellant mean bulk temperature
Ballistic performance data
Nozzle vectoring parameters
Insulation performance factors (asbestos-free design)
Ablative nozzle erosion
Vibration, acoustic, and heat flux data to support definition of environments
Command and control using flight-like avionics subsystem
Nozzle plug debris characterization
Analysis of instrumentation data and post-test hardware evaluation used to show compliance to objectives
Daily countdown test runs have been conducted for the past couple weeks to verify all systems are ready for Wednesday’s QM-1 test fire. According to company spokesperson Kay Anderson, the dry runs went very smoothly and served their purpose, which was to find any bugs or discrepancies and resolve them long before test day.
To help put the power of Orbital ATK’s five-segment SRB into perspective, consider this: If the heat energy of the booster could be converted to electric power, the two SRBs firing for two minutes would produce 2.3 million kilowatt hours of power, enough to supply the entire power demand of over 92,000 homes for a full day.
QM-1 will support qualification of the booster design for performance at the highest end of the motor’s accepted propellant temperature range, some 90 degrees Fahrenheit. In order for engineers to specifically assess this the booster has been housed for some time inside a 100 degree Fahrenheit movable structure, conditioning QM-1 daily in order to reach a propellant mean bulk temperature of 90 (+/- 5) degrees Fahrenheit.
The “test window” is available until 2:00 p.m. MDT (4:00 p.m. EDT); if they cannot fire the booster by that time they will stand down for crew rest requirements and try again March 12, assuming the delay was something minor that would not require an extended delay (of course, that cannot be determined until it happens).
Once the test is complete, a post-fire disassembly inspection will be conducted. It will take approximately six weeks to disassemble and remove the QM-1 booster from the test stand, and detailed inspections will take another several months.
A second, low-temperature test (QM-2) is planned for early 2016 before the hardware testing to support qualification of the boosters will be complete, at which point they will then be ready to proceed toward the first flight of SLS, currently scheduled to fly on the Exploration Mission-1 (EM-1) in late 2018.
Orbital ATK has set up public viewing areas for the test fire, so anyone wanting to witness it in person is welcome to make their way to Promontory, Utah, to see another big milestone on the road toward the first launch of NASA’s SLS.
Quelle: AS
-
Update: 11.03.2015
.
SLSFiredUp
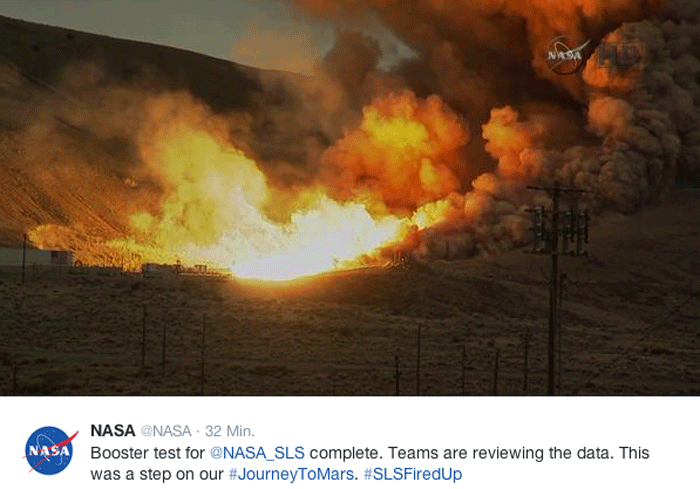
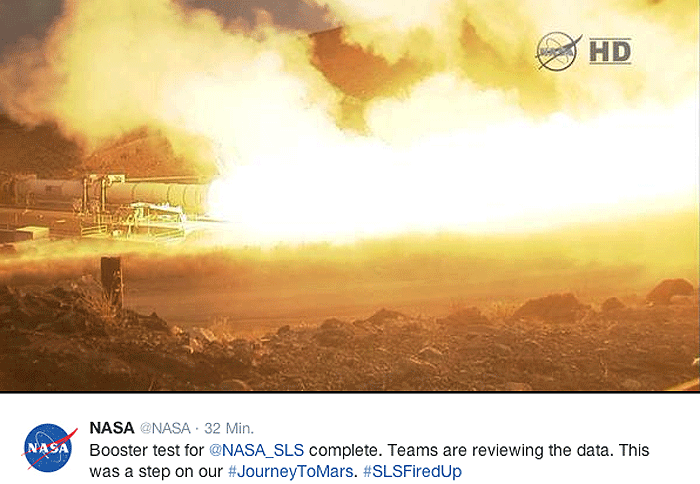
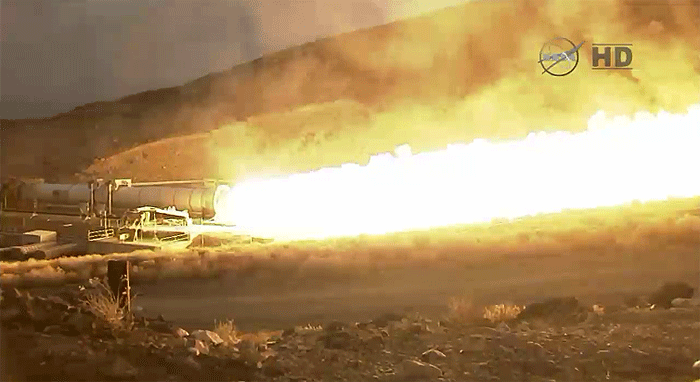
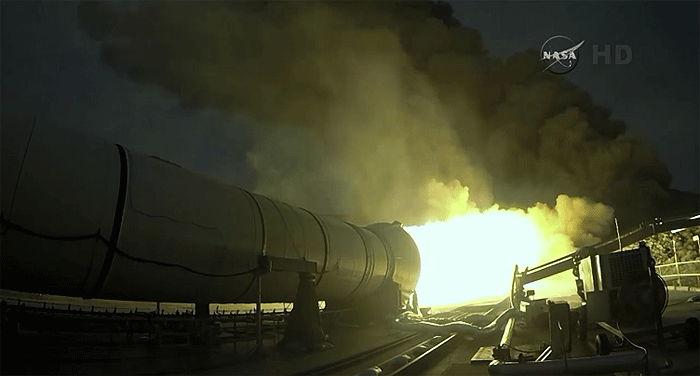
Quelle: NASA
-
Update: 13.05.2015
.
QM-1 Static Test – One Step Closer to Flight
NASA’s Space Launch System (SLS) is one step closer to flight following Orbital ATK’s March 11 successful five-segment rocket motor qualification ground test. Immediately following the spectacular two-minute test, it appeared that everything went exactly as expected. More significant is that two months later, now that disassembly has begun and engineers have reviewed and analyzed miles of data, it is clear that the test was a resounding success.
NASA’s SLS will launch on its first mission, Exploration Mission-1, in just a few years, and in the future, the SLS vehicle, along with NASA’s Orion crew capsule, will take humans farther into space than ever before.
The ground test of Orbital ATK’s five-segment rocket motor, known as Qualification Motor-1 (QM-1), had 102 design objectives and was supported by more than 530 instrumentation channels. A key objective of QM-1 was to test the solid rocket motor performance at high temperature (90 degrees F mean bulk temperature). The motor’s nozzle and insulation performed as expected, ballistics performance parameters met requirements, and the thrust vector control and avionics system provided the required command and control of the motor nozzle position – exactly as planned.
“These test results, along with the many other milestones being achieved across the program, show SLS is on track to preserve our nation’s leadership in space exploration,” said Charlie Precourt, Vice President and General Manager of Orbital ATK’s Propulsion Systems Division, and four-time space shuttle astronaut.
Orbital ATK’s new five-segment boosters for SLS leverage a flight-proven four-segment design, while implementing technological and performance upgrades including: the addition of a fifth motor segment to provide increased power, an advanced avionics system, a more environmentally friendly motor insulation design, a safer flight termination system, and more efficient and modern processing techniques. These changes were designed to meet performance requirements and increase reliability, while lowering manufacturing costs.
This first test of the SLS qualification phase of testing (QM-1) was preceded by a robust three-test demonstration phase (DM-1, DM-2 and DM-3) that helped to substantiate motor design. The qualification phase will conclude with QM-2, scheduled for next spring, fully demonstrating the motor’s readiness for flight. QM-2 will test the motor performance at the lower temperature limit (40 degrees).
“Ground tests are very important – we strongly believe in testing before flight to ensure lessons-learned occur on the ground and not during a mission,” said Precourt. “With each test we have learned things that enable us to modify the configuration to best meet the needs for the upcoming first flight.”
.
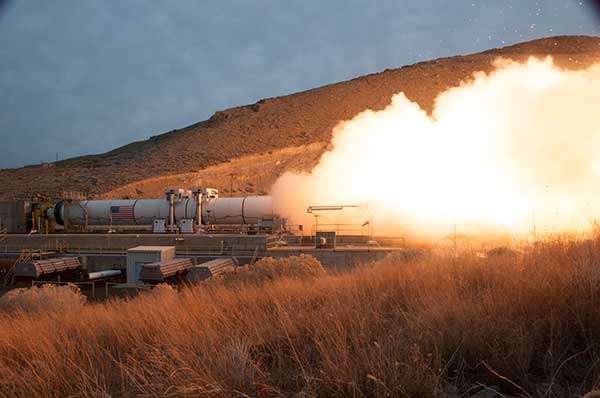
The ground test of Orbital ATK’s five-segment rocket motor, known as QM-1, ocurred on March 11, 2015.
.
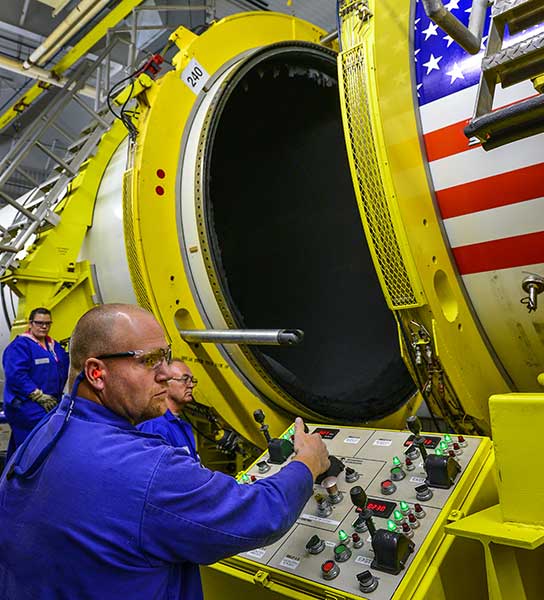
Orbital ATK technicians de-mated the QM-1 center forward segment from the forward segment as part of the qualification motor’s disassembly process.
.
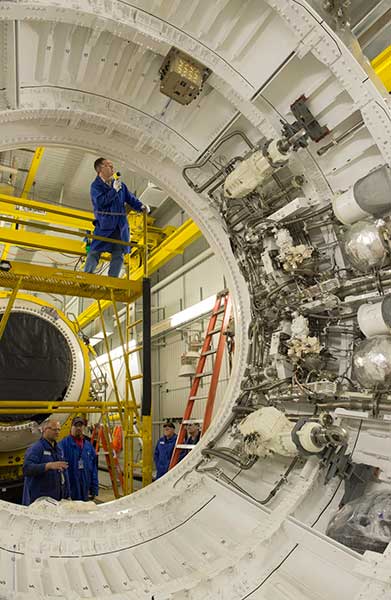
Orbital ATK technician analyze the five-segment solid rocket motor following the March 11, 2015 QM-1 test.
Quelle: Orbital
4935 Views