.
9.08.2014
Aerojet Rocketdyne hot-fires a launch abort engine for Boeing’s CST-100 spacecraft for NASA’s Commercial Crew Program. This week Aerojet announced they have fulfilled their commitment to Boeing for CCiCap.
.
This week Aerojet Rocketdyne announced it has completed its Commercial Crew Integrated Capability (CCiCap) commitment in support of Boeing’s Crew Space Transportation (CST-100) “space taxi,” one of three low-Earth ORBIT (LEO) spacecraft being developed with NASA funds, and competing for a NASA contract, to return LEO human spaceflight capability to the United States by 2017.
Since the RETIREMENT of NASA’s space shuttle fleet in 2011, the U.S. has been forced to buy seats for our astronauts to fly to and from the $100 billion International Space Station (ISS) from the Russians, on their Soyuz spacecraft, at a cost of over $70 million per seat. The CST-100 is Boeing’s answer at ending our nation’s dependence of Russia for crewed LEO transportation, and the work Aerojet Rocketdyne has done with Boeing on CST-100 since 2010 has continued the development of the CST-100′s service module and launch abort propulsion system, and will help return astronauts to LEO from U.S. soil soon.
“Over the past year, we’ve achieved major milestones that are paving the way for CST-100 to take FLIGHT,” said Terry Lorier, Aerojet Rocketdyne’s CST-100 service module propulsion system program manager. “In total, during the CCiCap contract period of performance, Aerojet Rocketdyne conducted eight Launch Abort Engine (LAE), 49 Orbital Maneuvering and Attitude Control (OMAC) system and 33 Reaction Control System (RCS) hot fire tests, all of which helped mature the system design to position Aerojet Rocketdyne to be ready to move into qualification testing early in the next phase of the program.”
Boeing’s capsule-shaped CST-100 is designed to take up to seven people, or a combination of people and cargo, to LEO and the ISS. Its service module and integrated launch abort propulsion system are designed to “push” the crew capsule to safety if an abort becomes necessary during the launch or ascent. If an abort is not necessary, which hopefully will always be the case, the propellant and propulsion system could instead be used to re-boost the orbit of the ISS, or be used to complete the spacecraft’s nominal mission through separation of the crew module from the service module as it begins re-entry back into the Earth’s atmosphere.
“The LAE test series saw the engine successfully operate at twice its mission life, producing 39,700 pounds force thrust,” said Lorier. “The four LAEs are derived from proven hardware based on heritage designs.”
The CST-100′s service module propulsion system will be powered by 24 1,500-pound thrust class OMAC engines, which are positioned in four clusters of six on the service module. They will provide low-altitude launch abort attitude control, maneuvering, and stage separation functions, high-altitude direct abort capability, and help the CST-100 to REFINE its orbit and “brake” at the end of a mission to slow down for re-entry.
.
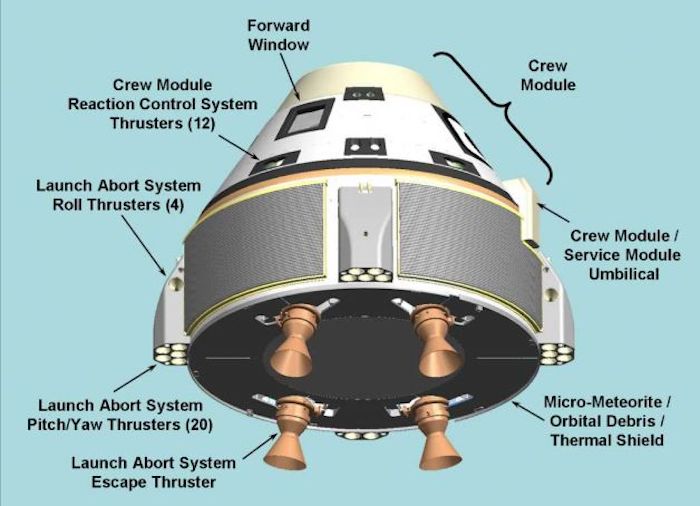
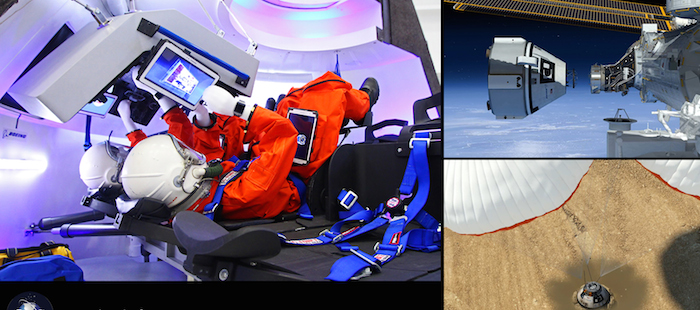
The Boeing Crew Space Transportation spacecraft, or CST-100 for short
.
The OMAC tests Aerojet carried out for Boeing’s CST-100 verified their durability in extreme heat, evaluated the opening and closing of their valves, and confirmed continuous combustion and performance. The thrusters were outfitted with numerous instruments and were fired in a VACUUM chamber that simulated the space-like environment at an altitude of 100,000 feet, giving engineers a chance to evaluate the thrusters through the burns and stresses they would encounter during a real FLIGHT.
“Boeing’s unique service-module propulsion system combines on-orbit propulsion with ascent abort capability into a SINGLE system, allowing the OMAC engine and the majority of the propellant feed and pressurization hardware to perform dual roles,” said John Mulholland, Boeing vice president and program manager, Commercial Programs. “This dual-role feature reduces the number of parts and provides operational flexibility, increasing system reliability and improving crew safety.”
According to Aerojet, the 28 100-pound thrust class RCS engines are adapted from a similar engine design currently in production. These engines provide high-altitude abort attitude control, on-orbit low delta-v maneuvering functions, and space station re-boost capability.
Boeing must pass two reviews coming up later this summer before completing their CCiCap agreement with NASA. A full critical design review (CDR) will examine the detailed plans for the spacecraft, launch vehicle, and a host of ground support, processing, and operations designs. The second review will come soon after, the Spacecraft Safety Review, which is meant to show the design of the CST-100 and its systems are in line with Boeing’s CDR-level design.
NASA is expected to announce which of the three companies it has funded to participate in CCiCap (Boeing, SpaceX, and Sierra Nevada) will advance to the next round of spacecraft development, known as Commercial Crew Transportation Capability (CCtCap), as soon as the end of this summer. If NASA selects Boeing to continue with CST-100 development, then the company would immediately move their operations to the Kennedy Space Center to manufacture, assemble, and test the actual CST-100 FLIGHT article.
Boeing, in PARTNERSHIP with Space Florida, is already leasing the former space shuttle Orbiter Processing Facility Bay-3 to do this, modernizing the facility (now known as the Commercial Crew and Cargo Processing Facility, or C3PF) to provide an environment for efficient production, testing, and operations for the CST-100 similar to Boeing’s satellite, space launch vehicle, and commercial airplane production programs.
Since 2010 NASA has given $1.5 billion to foster the development of a commercial crew spaceflight capability, and between the three companies competing for the ultimate contract Boeing has received the biggest chunk of change ($600 million so far). The space agency has expressed its wishes to AWARD commercial crew contracts to at least two companies, but that will be dependent on whether or not Congress provides adequate funding.
NASA is expected to announce the WINNERS of their Commercial Crew Program by September, which will pave the way to the final lap toward launching U.S. astronauts from American soil once more by 2017.
.
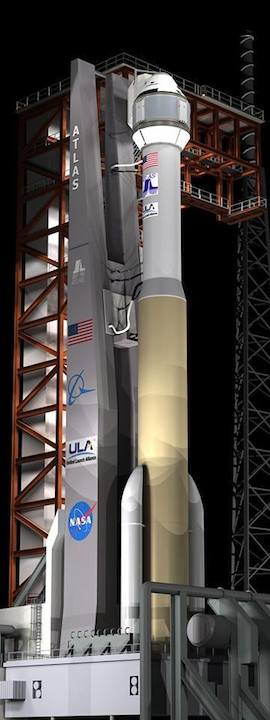
Quelle: AS
.
Update: 23.08.2014
.
Engineers and Technicians Install Protective Shell on NASA’s Orion Spacecraft
The heat shield on NASA’s Orion spacecraft gets all the glory when it comes to protecting the spacecraft from the intense temperature of reentry. Although the blunt, ablative shield will see the highest temperatures – up to 4,000 degrees Fahrenheit on its first flight this December – the rest of the spacecraft is hardly left in the cold.
Engineers and technicians at NASA’s Kennedy Space Center have finished installing the cone-shaped back shell of Orion’s crew module – the protective cover on the sides that make up Orion’s upside down cone shape. It’s made up of 970 black tiles that should look very familiar – the same tiles protected the belly of the space shuttles as they returned from space.
But the space shuttles traveled at 17,000 miles per hour, while Orion will be coming in at 20,000 miles per hour on this first flight test. The faster a spacecraft travels through Earth’s atmosphere, the more heat it generates. So even though the hottest the space shuttle tiles got was about 2,300 degrees Fahrenheit, the Orion back shell could get up to 3,150 degrees, despite being in a cooler area of the vehicle.
And heat isn’t the only concern. While in space, Orion will be vulnerable to the regular onslaught of micrometeoroid orbital debris. Although micrometeoroid orbital debris is too tiny to track, and therefore avoid, it can do immense damage to a spacecraft – for instance, it could punch through a back shell tile. Below the tiles, the vehicle’s structure doesn’t often get hotter than about 300 degrees Fahrenheit, but if debris breeched the tile, the heat surrounding the vehicle during reentry could creep into the hole it created, possibly damaging the vehicle.
Debris damage can be repaired in space with techniques pioneered after the space shuttle Columbia accident. A good deal of information was gathered then on what amount of damage warranted a repair. But the heating environment Orion will experience is different than the shuttle’s was, and the old models don’t apply.
Engineers will begin verifying new models when Orion returns from its first flight test this December. Before installing the back shell, engineers purposely drilled long, skinny holes into two tiles to mimic damage from a micrometeoroid hit. Each 1 inch wide, one of the holes is 1.4 inches deep and the other is 1 inch deep. The two tiles with these mock micrometeoroid hits are 1.47 inches thick and are located on the opposite side of the back shell from Orion’s windows and reaction control system jets.
“We want to know how much of the hot gas gets into the bottom of those cavities,” said Joseph Olejniczak, manager of Orion aerosciences. “We have models that estimate how hot it will get to make sure it’s safe to fly, but with the data we’ll gather from these tiles actually coming back through Earth’s atmosphere, we’ll make new models with higher accuracy.”
A better understanding of the heating environment for damage on Orion’s heat shield will inform future decisions about what kind of damage may require a repair in space.
.
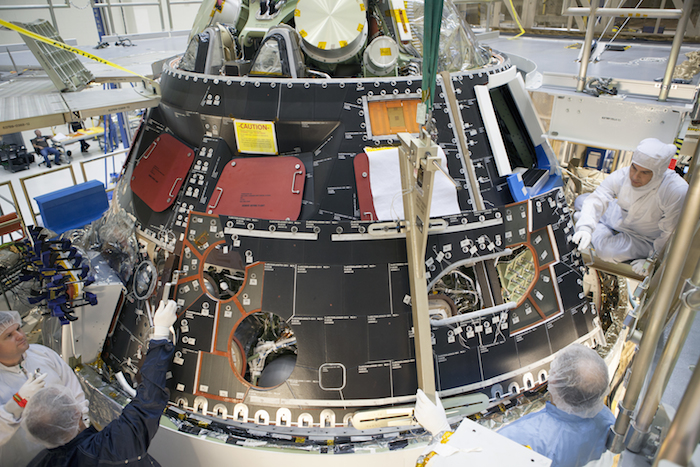
Inside the Operations and Checkout Building high bay at NASA's Kennedy Space Center in Florida, technicians dressed in clean-room suits install a back shell tile panel onto the Orion crew module.
Image Credit: NASA/Dimitri Gerondidakis
.
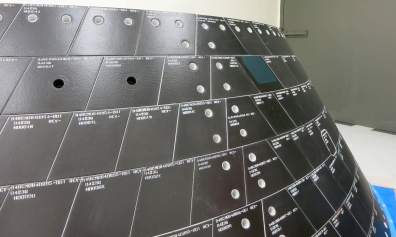
Two one-inch-wide holes have been drilled into tiles on Orion’s back shell to simulate micrometeoroid orbital debris damage . Sensors on the vehicle will record how high temperatures climb inside the hole during Orion’s return through Earth’s atmosphere following its first flight in December.
Quelle: NASA
.
Update: 9.09.2014
.
Orion’s First Crew Module Complete
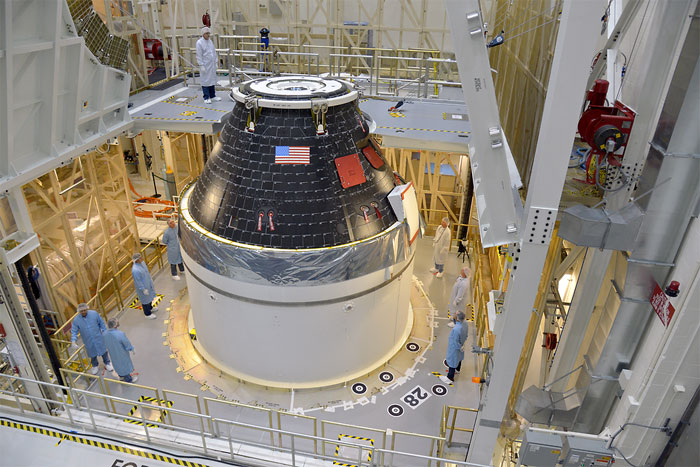
NASA’s first completed Orion crew module sits atop its service module at the Neil Armstrong Operations and Checkout Facility at Kennedy Space Center in Florida. The crew and service module will be transferred together on Wednesday to another facility for fueling, before moving again for the installation of the launch abort system. At that point, the spacecraft will be complete and ready to stack on top of the Delta IV Heavy rocket that will carry it into space on its first flight in December. For that flight, Exploration Flight Test-1, Orion will travel 3,600 miles above the Earth – farther than any spacecraft built to carry people has traveled in more than 40 years – and return home at speeds of 20,000 miles per hour, while enduring temperatures near 4,000 degrees Fahrenheit.
Quelle: NASA
.
Update: 12.09.2014
.
NASA’s Orion Spacecraft Nears Completion, Ready for Fueling
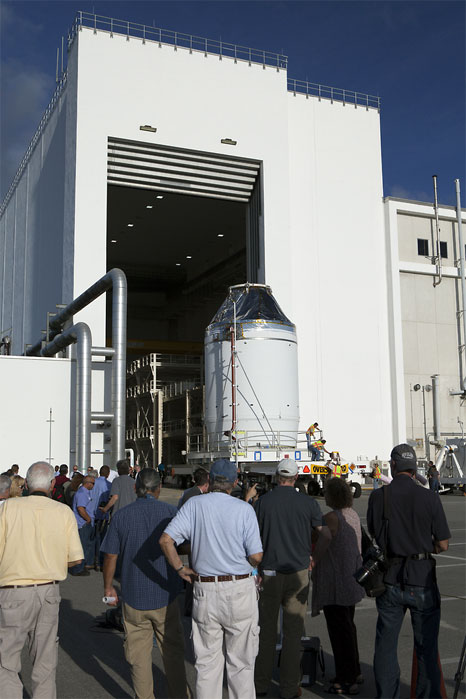
The Orion crew module, stacked atop its service module, moved out of the Neil Armstrong Operations and Checkout Building at NASA’s Kennedy Space Center in Florida on Sept 11. Orion was transported to the Payload Hazardous Servicing Facility at Kennedy where it will be fueled ahead of its December flight test. During the flight, Orion will travel 3,600 miles into space to test the spacecraft systems before humans begin traveling in Orion on future missions.
Image Credit: NASA/Dan Casper
.
NASA is making steady progress on its Orion spacecraft, completing several milestones this week at NASA's Kennedy Space Center in Florida in preparation for the capsule's first trip to space in December.
Engineers finished building the Orion crew module, attached it and the already-completed service module to the adapter that will join Orion to its rocket and transported the spacecraft to a new facility for fueling.
"Nothing about building the first of a brand new space transportation system is easy," said Mark Geyer, Orion Program manager. "But the crew module is undoubtedly the most complex component that will fly in December. The pressure vessel, the heat shield, parachute system, avionics -- piecing all of that together into a working spacecraft is an accomplishment. Seeing it fly in three months is going to be amazing."
Finishing the Orion crew module marks the completion of all major components of the spacecraft. The other two major elements -- the inert service module and the launch abort system -- were completed in January and December, respectively. The crew module was attached to the service module in June to allow for testing before the finishing touches were put on the crew module.
The adapter that will connect Orion to the United Launch Alliance (ULA) Delta IV Heavy rocket was built by NASA's Marshall Space Flight Center in Huntsville, Alabama. It is being tested for use on the agency's Space Launch System rocket for future deep space missions.
NASA, Orion's prime contractor Lockheed Martin, and ULA managers oversaw the move of the spacecraft Thursday from the Neil Armstrong Operations and Checkout Building to the Payload Hazardous Servicing Facility at Kennedy, where it will be fueled with ammonia and hyper-propellants for its flight test. Once fueling is complete, the launch abort system will be attached. At that point, the spacecraft will be complete and ready to stack on the Delta IV Heavy.
Orion is being built to send humans farther than ever before, including to an asteroid and Mars. Although the spacecraft will be uncrewed during its December flight test, the crew module will be used to transport astronauts safely to and from space on future missions. Orion will provide living quarters for up to 21 days, while longer missions will incorporate an additional habitat to provide extra space. Many of Orion's critical safety systems will be evaluated during December's mission, designated Exploration Flight Test-1, when the spacecraft travels about 3,600 miles into space.
.
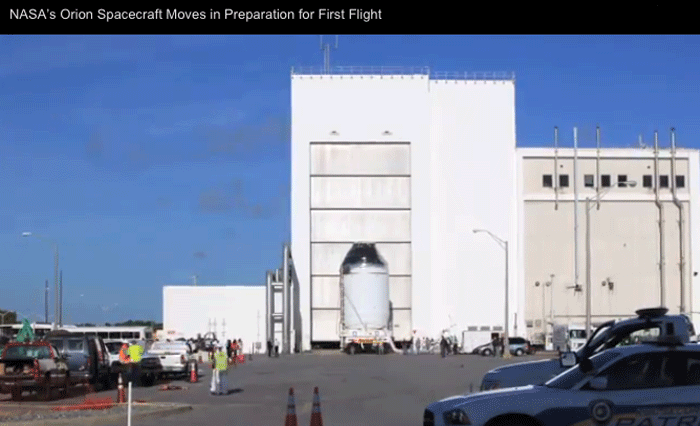
.
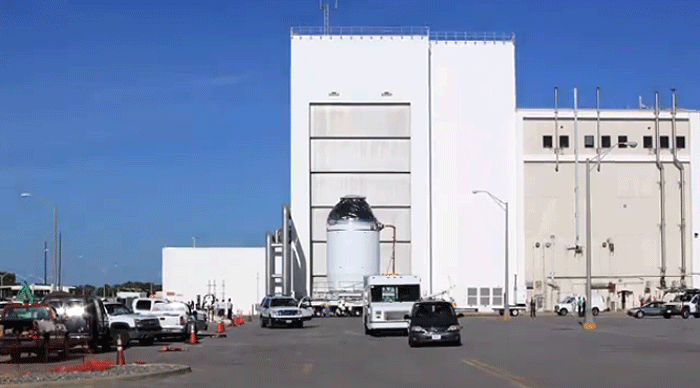
.
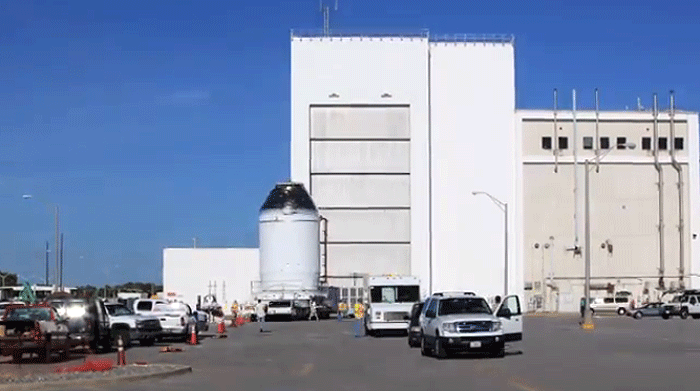
.
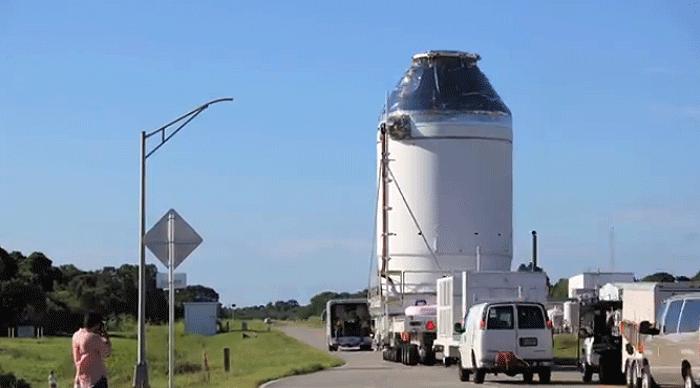
.
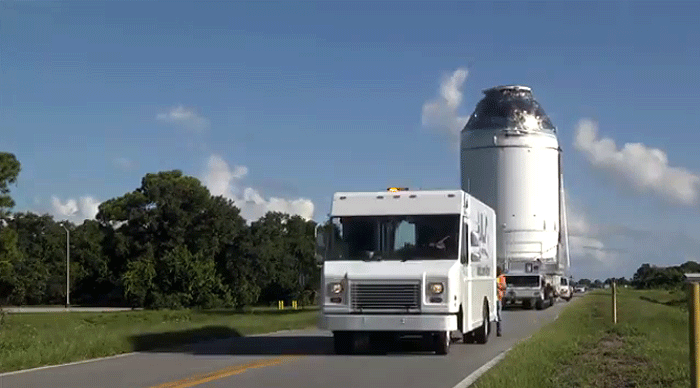
.
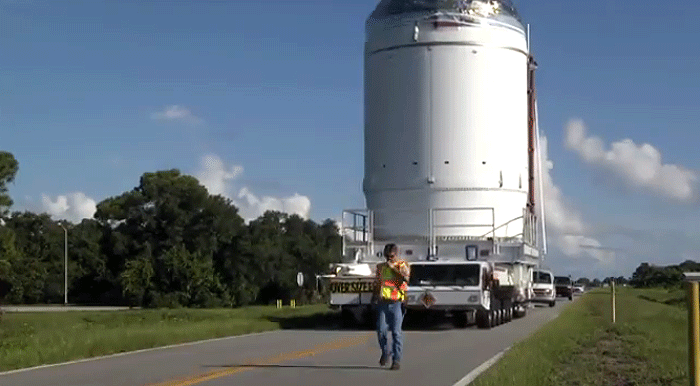
.
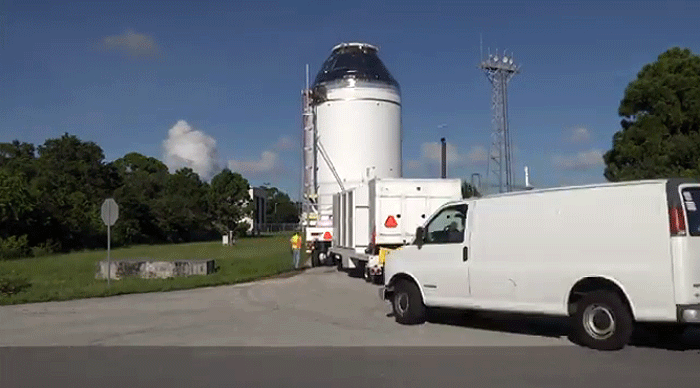
.
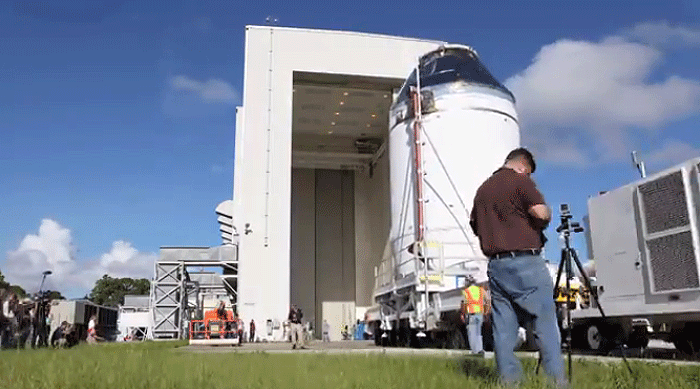
.
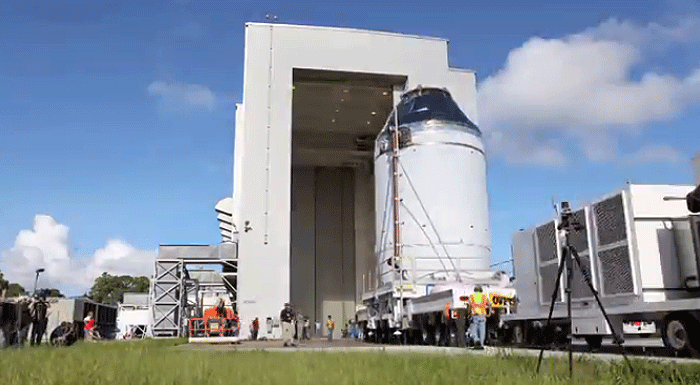
.
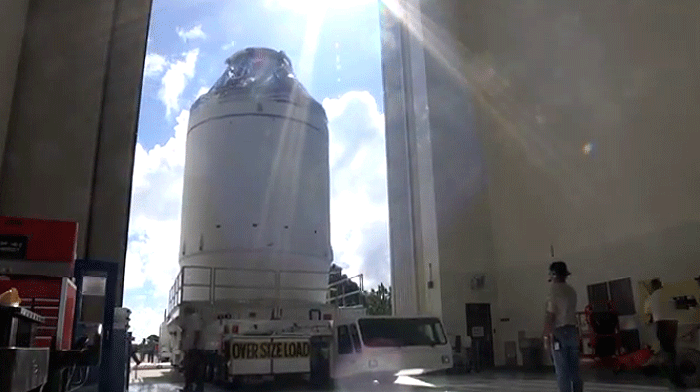
.
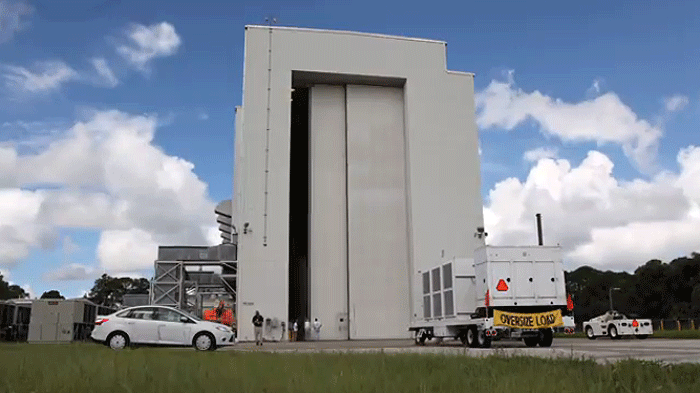
Quelle: NASA
.
Update: 25.09.2014
.
Third Round of Orion Underway Recovery Tests Help Teams Prepare for December Flight
.
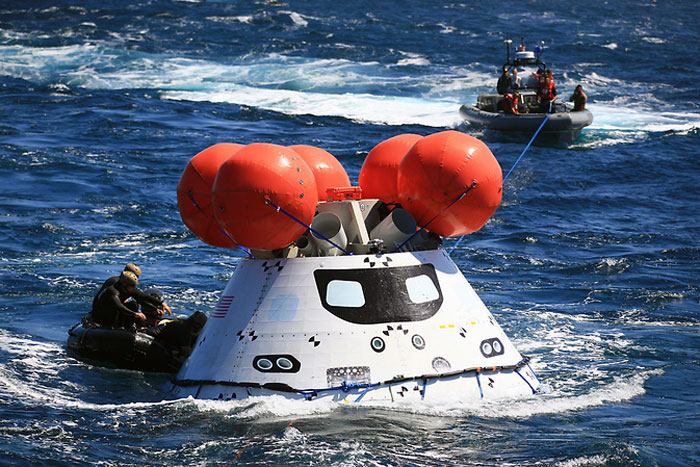
The Orion boilerplate test vehicle floated in the Pacific Ocean, near the USS Anchorage on Sept. 17, during the third day of Underway Recovery Test 3. U.S. Navy divers in a Zodiac boat, at left, and other team members in a rigid hull inflatable boat prepared the test vehicle for return to the ship.
.
NASA's John F. Kennedy Space Center
NASA, Orion prime contractor Lockheed Martin and the U.S. Navy successfully completed the third round of tests to practice recovering Orion when it splashes down off the coast of San Diego at the end of its December flight test. The mid-September test series, led by NASA's Ground Systems Development and Operations (GSDO) Program, continued to perfect techniques and ensure the full team and all equipment are ready when Orion returns to Earth after traveling more than 3,600 miles in altitude away from the planet.
Two Navy ships, a test version of Orion, several support boats, two helicopters and associated hardware and equipment were used for the tests.
The teams practiced two methods for recovering Orion. The first test began Sept. 11 at Naval Base San Diego, with loading of the test vehicle, equipment and hardware aboard the USNS Salvor (T-ARS 52), a safeguard-class rescue and salvage ship. Also on board were Navy radiomen and a civilian crew. The ship headed out to sea Sept. 12 to test a backup recovery method using the ship's stationary crane.
"The test was a success thanks to the expertise of the Salvor crew, Navy divers and the Department of Defense," said Marcos Pena, GSDO Technical Integration lead for crane recovery. "Recovery of the Orion crew module is essential to the success of Orion's flight test and subsequent Orion and Space Launch System missions in the years to come."
Starting in calm seas, the team used a 40-ton aft boom crane attached to the Navy ship to retrieve the 20,000 pound Orion test vehicle from the water. They continued recovery efforts in more challenging waters to determine recommended weather and sea condition limits for crane recovery.
During this test, Navy divers practiced attaching a “horse collar” around Orion and four tending lines that helped control lateral and longitudinal motion during crane recovery. The team also evaluated a basket lift rigging, consisting of 10 slings that were placed around Orion during crane lift operations.
"The basket lift rigging was tested previously on the USS Anchorage," said Pena. "We were able to take the next step and demonstrate that the basket lift rig and horse collar can be used to lift the test vehicle over the side of the ship and set it on a cradle on the ship's deck, all while maintaining motion control."
Tether lines from the ship were attached to Orion for towing tests at various speeds and can be used to bring the capsule to calmer waters for recovery.
On Sept. 15, the USNS Salvor rendezvoused with the USS Anchorage in the open sea and handed off the Orion test vehicle for the next portion of the recovery test.
During the week, the team performed an end-to-end recovery simulation using the ship's well deck, two of the Navy's Zodiac boats, four rigid hull inflatable boats, two helicopters and equipment and procedures that were used during August testing.
U.S. Navy divers in Zodiac boats and other team members in rigid hull inflatable boats were stationed in the water near the test vehicle. Orange stabilizers on the top of the test vehicle were inflated to simulate the system that will be used to upright Orion in the water after splashdown.
Using tether lines attached to the test vehicle, the team guided Orion back to the ship. In the well deck, NASA and Lockheed Martin workers set up a capture net, crew module recovery cradle, wing well fenders, speed bumps, and used a recovery winch, horse collar and Kevlar tending lines to stabilize Orion in the well deck.
During the week, they also practiced retrieving a mock-up of Orion's forward bay cover, a shell that fits over Orion’s crew module to protect the spacecraft during launch, orbital flight and reentry.
“Successful completion of this test series marks a significant milestone in NASA's partnership with the Navy to recover the Orion crew module after it splashes down in the Pacific Ocean in December,” said Jeremy Graeber, GSDO NASA Recovery director. "The integrated team has done an amazing job working to refine the procedures to make this mission a success. I feel confident that our team and hardware are ready to support Exploration Flight Test-1.”
Other goals of the test were to assess on-ship communications and ship-to-shore communications, as well as recording timing data for recovery activities to help provide future recovery methods for crewed missions.
The USS Anchorage returned to Naval Base San Diego on Sept. 19. The Orion test vehicle and recovery equipment were offloaded from the ship.
.
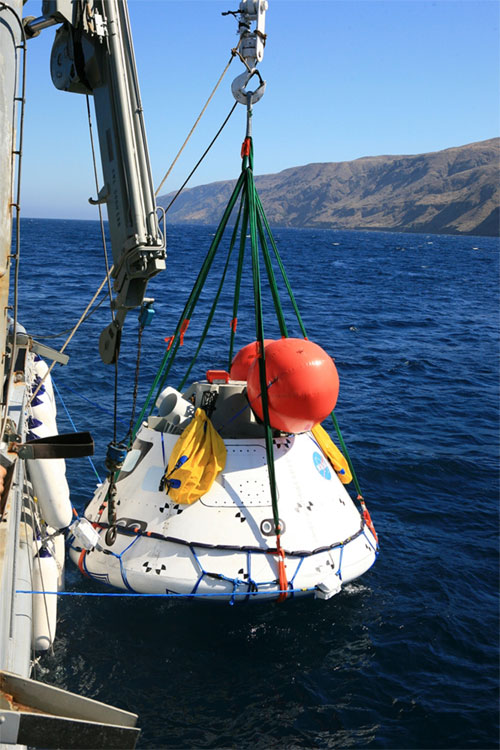
The Orion boilerplate test vehicle was lifted by stationary crane off the side of the USNS Salvor, a safeguard-class rescue and salvage ship, during Underway Recovery Test 4A in the Pacific Ocean on Sept. 14.
Quelle: NASA
,
Update: 29.09.2014
.
Delta IV Booster Integration Another Step Toward First Orion Flight
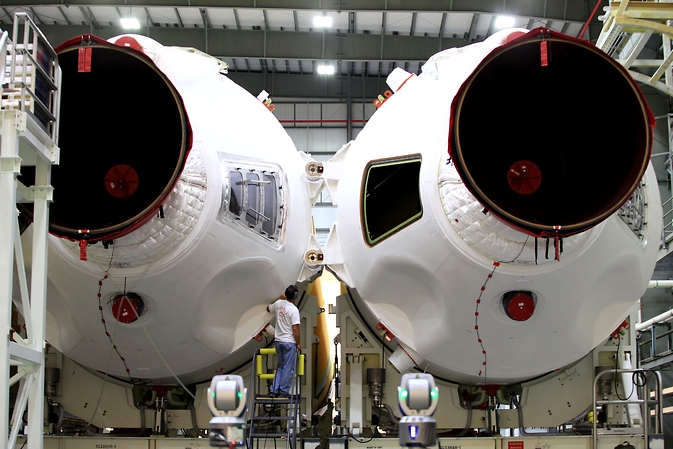
A United Launch Alliance technician monitors progress as core booster elements of a Delta IV Heavy rocket are being integrated in preparation for Exploration Flight Test-1.
.
Engineers took another step forward in preparations for the first test flight of NASA’s new Orion spacecraft, in December. The three primary core elements of the United Launch Alliance (ULA) Delta IV Heavy rocket recently were integrated, forming the first stage of the launch vehicle that will send Orion far from Earth to allow NASA to evaluate the spacecraft’s performance in space.
The three Delta IV Common Booster Cores were attached in ULA’s Horizontal Integration Facility (HIF), at Cape Canaveral Air Force Station in Florida. The HIF building is located at Space Launch Complex 37 where the mission will lift off.
The first booster was attached to the center rocket in June with the second one was attached in early August.
"The day-to-day processing is performed by ULA," said Merri Anne Stowe of NASA's Fleet Systems Integration Branch of the Launch Services Program (LSP). "NASA’s role is to keep a watchful eye on everything and be there to help if any issues come up."
Stowe explained that during major testing experts from NASA’s Launch Services Program monitor the work on consoles in Hanger AE at Cape Canaveral Air Force Station. Hangar AE is home to the Kennedy Space Center’s upgraded Launch Vehicle Data Center. The facility allows engineers to monitor voice, data, telemetry and video systems that support expendable launch vehicle missions. NASA’s Florida spaceport is also where Orion was built and is being processed.
The Delta IV rocket stages were assembled at the ULA plant in Decatur, Alabama, about 20 miles west of Huntsville. After completion, the rocket components were shipped down the Tennessee River and Tombigbee Waterway, a canal, to the Gulf of Mexico. From there they traveled to Cape Canaveral, arriving on May 6. The elements of the rocket's first stage were then transported to the HIF for preflight processing.
"After the three core stages went through their initial inspections and processing, the struts were attached, connecting the booster stages with the center core," Stowe said. "All of this takes place horizontally."
The three common booster cores are 134 feet in length and 17 feet in diameter. Each has an RS-68 engine that uses liquid hydrogen and liquid oxygen propellant producing 656,000 pounds of thrust. All totaled, the three Delta IV boosters collectively generate 1.96 million pounds of thrust.
The second stage of the Delta IV rocket is 45 feet in length and 17 feet in diameter. It uses one RL10-B-2 engine, also burning liquid hydrogen and liquid oxygen propellant creating 25,000 pounds of thrust.
"The second stage was taken to the Delta Operations Center for processing after it arrived," said Stowe. "The second stage was moved to the HIF on Aug. 29 and is scheduled to be horizontally mated to the first stage on Sept. 12."
The same upper stage will be used on the block 1 version of NASA's new heavy-lift rocket, the Space Launch System (SLS). More powerful than any rocket ever built, SLS will be capable of sending humans aboard Orion to deep-space destinations such as an asteroid and Mars.
"The hardware for Exploration Flight Test-1 is coming together well," Stowe said. "We haven't had to deal with any serious problems. All of the advance planning appears to be paying off."
Once all the launch vehicle stages are mated and thoroughly checked out, the next step is the Test Readiness Review.
"These meetings are held to bring together all the interested parties to be sure the Delta IV rocket is ready for the move to the launch pad where the Orion spacecraft will be mated," Stowe said.
The upcoming flight test will use the Delta IV Heavy to launch the Orion and send it 3,600 miles in altitude beyond the Earth's surface. During the two-orbit, four-hour mission, engineers will evaluate the systems critical to crew safety, the launch abort system, the heat shield and the parachute system. The data gathered during the mission will influence design decisions and validate existing computer models. The flight also will reduce overall mission risks and costs for later Orion flights.
The capsule will re-enter Earth’s atmosphere at speeds approaching 20,000 mph, generating temperatures as high as 4,000 degrees Fahrenheit, before splashing down in the Pacific Ocean.
The Lockheed Martin-built Orion is designed to take humans farther than ever before. The spacecraft will serve as the exploration vehicle that will carry astronauts to space and provide safe re-entry from deep-space missions. Orion currently is undergoing final assembly in Kennedy's Neil Armstrong Operations and Checkout Building.
Stowe is especially invested in a successful outcome for the flight test.
.
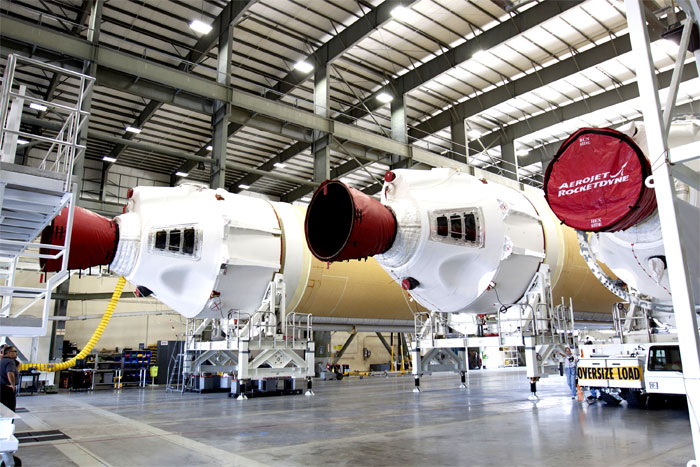
A transporter for oversize loads delivers the port, or left, booster for the United Launch Alliance Delta IV Heavy for Exploration Flight Test-1 into the Horizontal Integration Facility, or HIF, on May 7. The port booster joins the other two boosters of the Delta IV Heavy already in the HIF.
.

In the Horizontal Integration Facility at Cape Canaveral Air Force Station, two core elements of a Delta IV Heavy rocket are brought together in preparation for Exploration Flight Test-1.
.
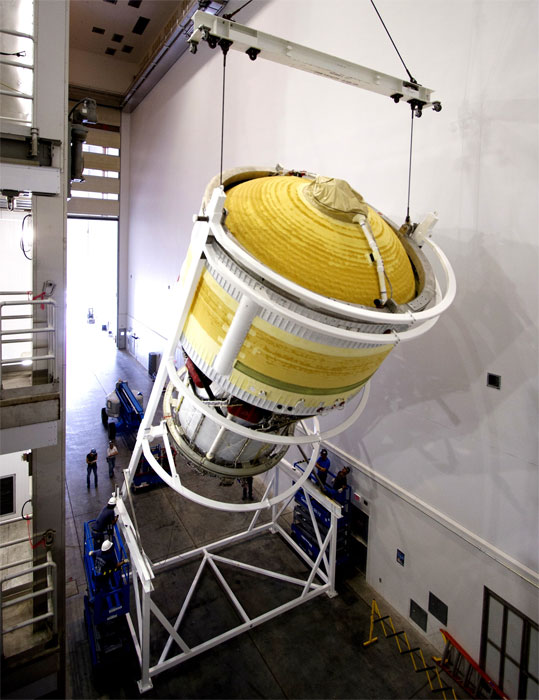
Inside the Delta Operations Center near Space Launch Complex 37 on Cape Canaveral Air Force Station, the second stage for the United Launch Alliance Delta IV Heavy for Exploration Flight Test-1 is lifted high by crane for the move to a test cell.
.
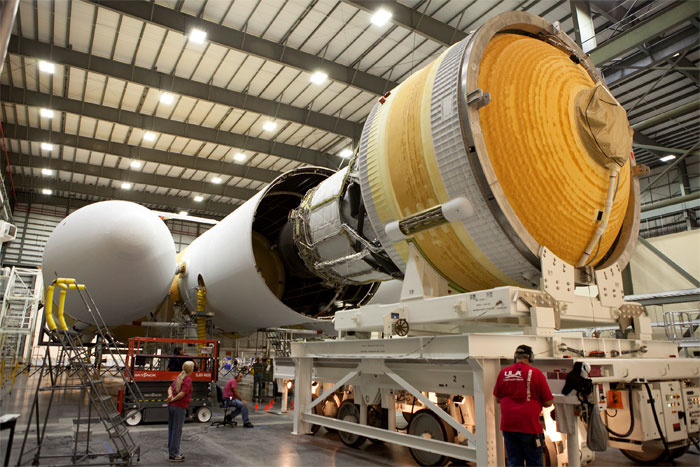
Inside the Horizontal Integration Facility at Space Launch Complex 37 at Cape Canaveral Air Force Station, United Launch Alliance technicians prepare the second stage of a Delta IV Heavy rocket for mating to the central core booster of the three booster stages for the unpiloted Exploration Flight Test-1.
Quelle: NASA
.
Update: 2.10.2014
.
NASA’s Orion Spacecraft, Rocket Move Closer to First Flight
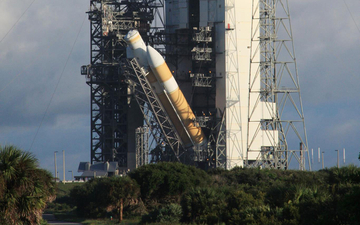
NASA’s new Orion spacecraft and the Delta IV Heavy rocket that will carry it into space are at their penultimate stops in Florida on their path to a December flight test.
Orion was moved Sunday out of the Payload Hazardous Servicing Facility at NASA’s Kennedy Space Center in Florida and the Delta IV Heavy rocket, built by United Launch Alliance, made its move Tuesday night, to nearby Space Launch Complex 37 at Cape Canaveral Air Force Station. It was raised Wednesday from the horizontal position into its vertical launch configuration.
“We’ve been working toward this launch for months, and we’re in the final stretch,” said Kennedy Director Bob Cabana. “Orion is almost complete and the rocket that will send it into space is on the launch pad. We’re 64 days away from taking the next step in deep space exploration.”
Orion now is ready for the installation of its last component -- the launch abort system. This system is designed to protect astronauts if a problem arises during launch by pulling the spacecraft away from the failing rocket. During the December, uncrewed flight, the jettison motor, which separates the launch abort system from the crew module in both normal operations and emergency, will be tested.
Once the launch abort system is stacked on the completed crew and service modules, and the three systems are tested together, the Orion spacecraft will be considered complete. It then will wait inside the launch abort system facility until mid-November, when the Delta IV Heavy rocket is ready for integration with the spacecraft.
The rocket’s three Common Booster Cores were tested, processed and attached to each other to form the first stage that will connect to Orion’s service module.
Following its targeted Dec. 4 launch, the Delta IV Heavy will send Orion 3,600 miles above Earth to test the spacecraft’s systems most critical to crew safety. After orbiting Earth twice, Orion will reenter Earth’s atmosphere at 20,000 miles per hour, generating temperatures near 4,000 degrees Fahrenheit, before it splashes down in the Pacific Ocean.
Orion is being built to send humans farther than ever before, including to an asteroid and Mars. Although the spacecraft will be uncrewed during its December flight, which is designated Exploration Flight Test-1, the crew module will be used to transport astronauts safely to and from space on future missions. Orion will provide living quarters for up to 21 days, while longer missions will incorporate an additional habitat to provide extra space.
.
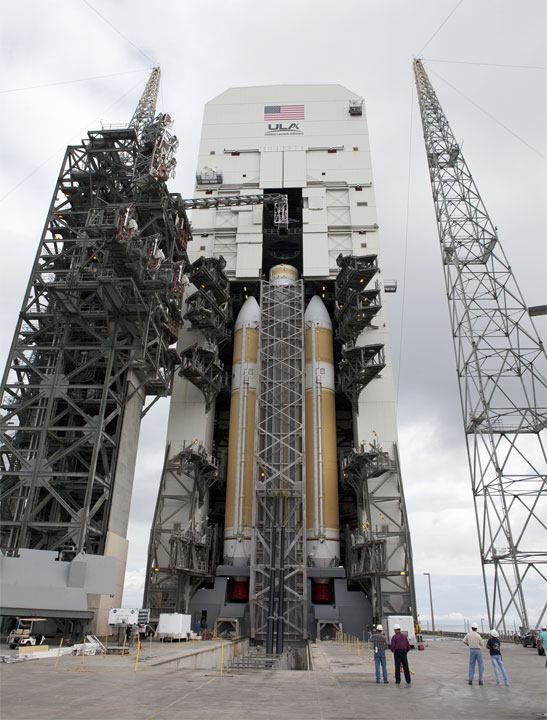
The United Launch Alliance Delta IV Heavy rocket that will send NASA’s Orion spacecraft on its first flight test in December was moved to its vertical launch position Oct. 1 at Space Launch Complex 37 at Cape Canaveral Air Force Station in Florida. The rocket is secured on the Elevated Platform Transporter.
Quelle: NASA
.
Update: 6.10.2014
.
Launch Abort System Installed for Orion Flight Test
The launch abort system for the Orion Flight Test is lowered by crane for installation on the Orion spacecraft inside the Launch Abort System Facility, or LASF, at NASA's Kennedy Space Center in Florida. The completed crew and service modules will be tested and verified together with the launch abort system. Orion will remain inside the LASF until mid-November, when the United Launch Alliance Delta IV Heavy rocket is ready for integration with the spacecraft.
Orion is the exploration spacecraft designed to carry astronauts to destinations not yet explored by humans, including an asteroid and Mars. It will have emergency abort capability, sustain the crew during space travel and provide safe re-entry from deep space return velocities. The first unpiloted test flight of the Orion is scheduled to launch in December atop the Delta IV Heavy rocket from Cape Canaveral Air Force Station in Florida to an altitude of 3,600 miles above the Earth's surface. The two-orbit, four-hour flight test will help engineers evaluate the systems critical to crew safety including the heat shield, parachute system and launch abort system.
.
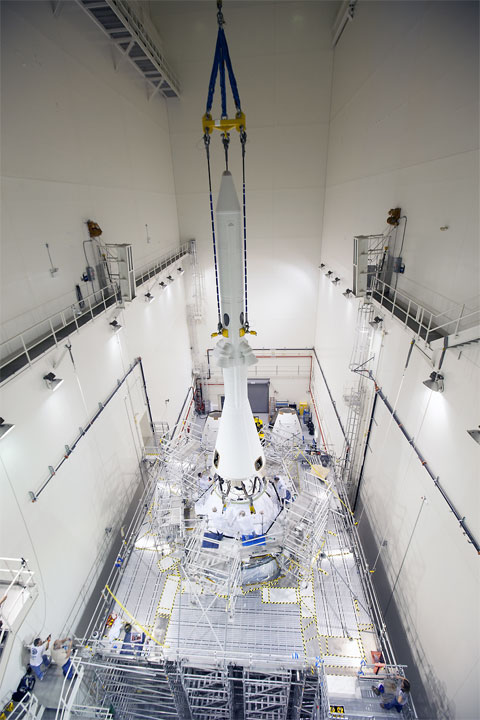
Quelle: NASA
.
Update: 4.11.2014
.
Orion Takes Big Step Before Moving to the Launch Pad
.
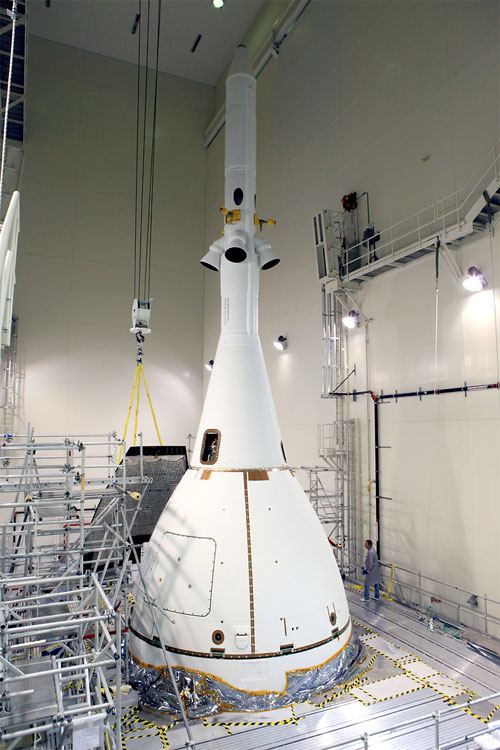
Inside the Launch Abort System Facility at NASA’s Kennedy Space Center in Florida, a crane brings the fourth and final Ogive panel closer for installation on Orion's Launch Abort System. The panels will smooth the airflow over the conical spacecraft to limit sound and vibration.
Image Credit: NASA/Kim Shiflett
.
Kevin Rivers was nothing but giddy as he stood behind the closed door of the Launch Abort System Facility at NASA’s Kennedy Space Center in Florida, waiting to see the Orion spacecraft that will one day send humans on the journey to Mars. After just a few minutes that seemed like a lifetime, Rivers, the Launch Abort System project manager, walked through the facility door.
There before him stood the 80-foot high Orion spacecraft being readied for its December flight test with the four recently-installed protective panels that make up the Ogive. The Ogive reduces drag and acoustic load on the crew module, making it a smoother ride for the spacecraft.
“What my colleagues and I were able to witness was a significant historical point in our efforts to move beyond low-Earth orbit and explore past the moon,” Rivers said.
On Dec. 4, Orion is scheduled to launch atop a United Launch Alliance Delta IV Heavy rocket from Cape Canaveral Air Force Station’s Space Launch Complex 37 in Florida. During the test, Orion will travel 3,600 miles in altitude above Earth. 4 1/2 hours later, the spacecraft will reenter the atmosphere at 20,000 mph and splash down in the Pacific Ocean. Orion’s first flight will verify launch and high-speed reentry systems such as avionics, attitude control, parachutes and the heat shield.
Barry Meredith, who works with Rivers at NASA’s Langley Research Center in Virginia, expressed a similar awe. “Orion’s flight test is a major step toward exploring beyond low-Earth orbit,” he said. “Though a crew will not occupy the first flight, it’s really critical that we test the spacecraft systems.”
The Ogive installation was one of the last pieces of the puzzle for Orion prior to its move to the launch pad on Nov. 10. There, it will be lifted and attached to the rocket for its December launch.
“There is much effort and preparation for such a momentous occasion,” said Langley engineer Jose Ortiz. “There are many disciplines, geographically dispersed specialties and developments, tests, elaborate analyses, materials characterizations, and other efforts by NASA centers and contractor partners. The nationwide effort is aimed toward one common and challenging goal in mind: human spaceflight.”
Orion is managed out of NASA’s Johnson Space Flight Center in Texas, and the Launch Abort System project is managed out of Langley. NASA centers and industry partners from across the country have also played a critical role in the design, development and testing of Orion.
Quelle: NASA
.
Update: 8.11.2014
.
NASA’s Orion to Roll out to Launch Pad for First Flight
NASA’s Orion spacecraft is set to roll out of the Launch Abort System Facility (LASF) at NASA’s Kennedy Space Center in Florida to its launch pad at nearby Cape Canaveral Air Force Station’s Space Launch Complex 37 on Monday Nov. 10, in preparation for liftoff next month on its first space flight.
At 4:30 p.m. EST, NASA Television will air a news briefing live from the LASF before Orion’s move. Participating will be Robert Cabana, Kennedy Space Center director; Ellen Ochoa, Johnson Space Center director; Mark Geyer, Orion Program manager; and Mike Hawes, Lockheed Martin Space Systems Company director of Human Space Flight Programs.
The spacecraft will start its journey to the launch pad at 8 p.m. The rollout will not be carried live on NASA TV, but highlights of the move will air on NASA TV’s Video File segments and the agency’s website starting Tuesday morning, Nov. 11. The spacecraft is expected to reach Space Launch Complex 37 at about 2 a.m., Tuesday.
.

Quelle: NASA
.
Update: 11.11.2014
.
NASA's Orion spacecraft rollout rescheduled for 8:30 p.m. Tuesday
CAPE CANAVERAL --
NASA is postponing the rollout of its Orion spacecraft.
NASA announced Monday evening that the Delta IV Heavy rocket carrying the test capsule will not go to the launch pad because of weather. The rollout has been rescheduled for 8:30 p.m. Tuesday, Nov. 11.
The rocket was set to roll out of the Launch Abort System Facility at the Kennedy Space Center Monday to its launch pad at Cape Canaveral Air Force Station's Space Launch Complex 37.
NASA has targeted Dec. 4 for the first test flight of Orion.
Tickets for launch viewing at the Kennedy Space Center Visitor Complex are available online. Admission is $50 for adults and $40 for children. Launch transportation costs an additional $20 per person.
The uncrewed flight test will take the spacecraft 3,600 miles above Earth on a more than four hour flight to test many of the systems critical for future human missions into deep space.
NASA says after two orbits and 60,000 miles, Orion will re-enter Earth's atmosphere at almost 20,000 mph before its parachute system deploys to slow the spacecraft for a splashdown in the Pacific Ocean. On future missions, the Orion spacecraft will help carry astronauts farther into the solar system than ever before, including to an asteroid and Mars.
Quelle: NEWS13
.
Update: 12.11.2014
.
Orion Passes LC-39B
The Orion spacecraft passed by the launch pad that will launch future Orion missions to deep space. Launch Complex 39B has been refurbished and modified to host Orion and the massive Space Launch System rocket. It will be used for the first time to launch Exploration Mission-1, the second flight for Orion, and the first for the Space Launch System, before the two carry astronauts into deep space on later flights.
.

.
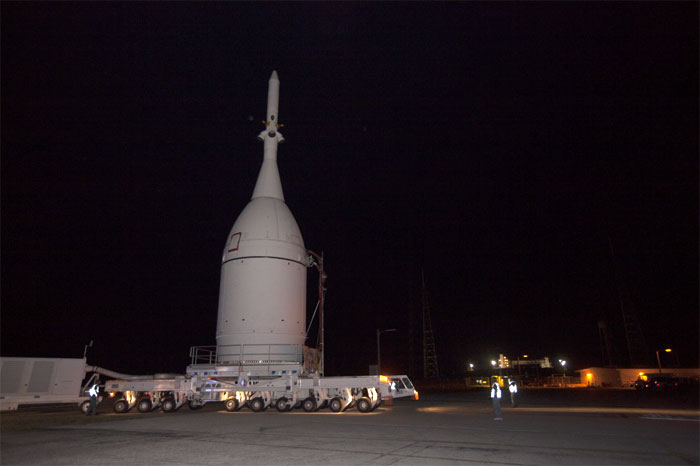
Quelle: NASA
.
Update: 13.11.2014
.
Orion Spacecraft Arrives To Cape Canaveral’s Launch Pad 37
Orion Ready for Integration with Delta IV Heavy Rocket
CAPE CANAVERAL, Nov. 12, 2014 –The Lockheed Martin [NYSE: LMT] built Orion spacecraft has completed its 22-mile, 6-hour journey from the Launch Abort System Facility at Kennedy Space Center, to launch pad 37 at Cape Canaveral Air Force Station, Florida. Orion is now another step closer to its first test flight on Dec. 4, 2014.
“This spacecraft is going to push the boundaries of scientific discovery and human achievement,” said Michael Hawes, Lockheed Martin Orion program manager. “One day, not too far in the future, an astronaut will leave the first footprints in the red dust of Mars, and we’ll look back and say that journey started here.”
This morning, the 50,000 lb. spacecraft was lifted about 200 feet up and mated to the United Launch Alliance (ULA) Delta IV Heavy rocket, which Lockheed Martin contracted for the flight. Over the next few weeks, the rocket and spacecraft will be integrated and powered up, and engineers will test and verify interfaces between the two in preparation for Exploration Flight Test-1 (EFT-1).
“It has been a tremendous team effort with all of our mission partners to get us to this point just one month prior to launch,” said Jim England, ULA’s EFT-1 program manager. “We are honored to play such a critical role in this important launch for NASA and are focused on providing mission success so that Orion can complete all of its mission objectives.”
During EFT-1, the uncrewed spacecraft will travel 3,600 miles beyond Earth—15 times further than the International Space Station. That same day, Orion will return to Earth at a speed of approximately 20,000 mph for a splashdown in the Pacific Ocean. EFT-1 will provide engineers with data about systems critical to crew safety, such as heat shield performance, separation events, avionics and software performance, attitude control and guidance, parachute deployment, and recovery operations to validate designs of the spacecraft before it begins carrying humans to new destinations in deep space.
Headquartered in Bethesda, Maryland, Lockheed Martin is a global security and aerospace company that employs approximately 113,000 people worldwide and is principally engaged in the research, design, development, manufacture, integration and sustainment of advanced technology systems, products and services. The Corporation’s net sales for 2013 were $45.4 billion.
With more than a century of combined heritage, United Launch Alliance is the nation’s most experienced and reliable launch service provider. ULA has successfully delivered nearly 90 satellites to orbit that provide critical capabilities for troops in the field, aid meteorologists in tracking severe weather, enable personal device-based GPS navigation and unlock the mysteries of our solar system.
.
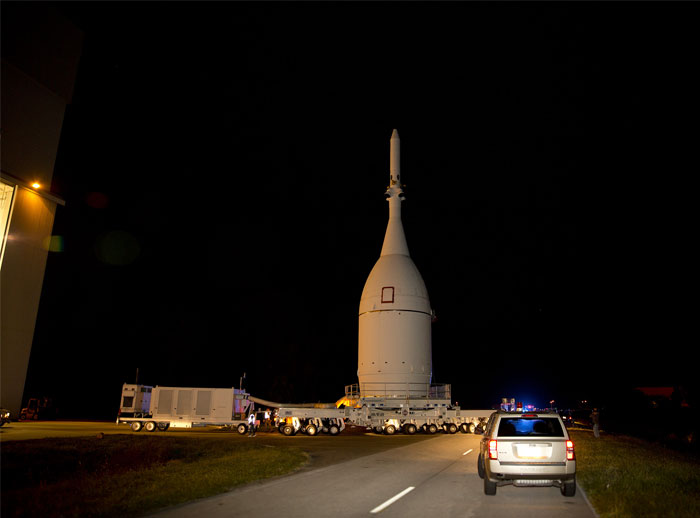
.
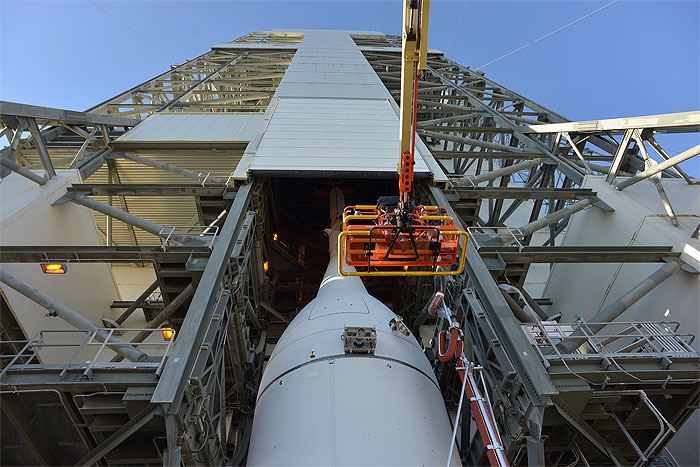
Photo Captions: The Orion spacecraft has been transported to launch pad 37 and has been lifted about 200 ft. to mate with the Delta IV Heavy rocket.
Quelle: Boeing
5821 Views