.
Orion Space Capsule gears up for tests at NASA Langley
Test for Orion are taking place at NASA Langley. (March 17, 2014)
.
Hampton, Va. – NASA scientists are working to get humans back in space. But before an astronaut can be sent on a mission, a lot of testing has to be performed on a spacecraft to make sure the vehicle is safe.
A mock-up of NASA’s Orion spacecraft recently made a trip from the Kennedy Space Center in Florida to NASA’s Langley Research Center in Hampton. In the coming months, scientists will test the Orion’s crew module, which will give engineers insight into how the capsule performs under ocean and landing conditions.
“The Orion Project is our next big spacecraft that will be able to take us to deep space,” said Carrie Rhoades, SPLASH Chief Engineer at NASA Langley.
Although the full-sized test version crew module at NASA Langley will not be traveling to space, the testing done to the module will help researchers develop a safe spacecraft similar to it, that will one day in the future take astronauts to destinations never explored before.
“We want to make sure we put people up and bring them back safely,” said Rhoades.
NASA researchers will conduct static and water impact loads evaluations on the module at NASA Langley’s Landing and Impact Research Facility. The tests will simulate water landing scenarios for different velocities, parachute deployments, wave heights and wind conditions – conditions the spacecraft may encounter when it lands in the Pacific Ocean after a space mission.
“This is a huge deal to be able to test something this important to the space program because if we go out to Mars and everything, it would just be terrible to have a failure on the end as we’re coming back landing,” said Richard Boitnott, test engineer for the Orion Project.
The Orion is scheduled to go on its first test flight this September, traveling 3,600 miles above the Earth, reentering the atmosphere at 20,000 mph, with temperatures close to 4,000 degrees Fahrenheit. Although no humans will be on board the test flight, the capsule – the size of an SUV – can hold four astronauts on a real mission.
“People don’t even realize that certain things they use daily come from the space program, and we’re continually developing new things that get used out in the regular world,” said Rhoades.
If the Orion test flight goes well, the first full-scaled non-human flight is slated for 2017 – the next generation spacecraft that could take astronauts to Mars in the future.
Quelle: NewsChannel3
.
Update: 18.03.2014
.
Orion test launch slips to December
NASA today showed off recently arrived boosters that will help launch its Orion crew exploration capsule into space for the first time, hopefully before the end of this year.
The planned launch of an uncrewed Orion atop a United Launch Alliance Delta IV Heavy has slipped from September to December, allowing an Air Force satellite to precede the Orion mission, also on a Delta IV rocket.
"I assure you that Orion is going to be ready to go on time," said KSC Director Bob Cabana in the horizontal integration facility near Launch Complex 37 at Cape Canaveral Air Force Station.
Behind Cabana were the first two of the Delta IV Heavy's three core boosters that will be used for the mission called Exploration Flight Test-1, or EFT-1.
The mission will send Orion on two orbits reaching as far as 3,600 miles above Earth to set up a high-speed reentry through the atmosphere — about 85 percent of a lunar return's velocity -- and splashdown in the Pacific Ocean.
Quelle: Florida Today
.
Orion spacecraft on schedule for 2014 test flight
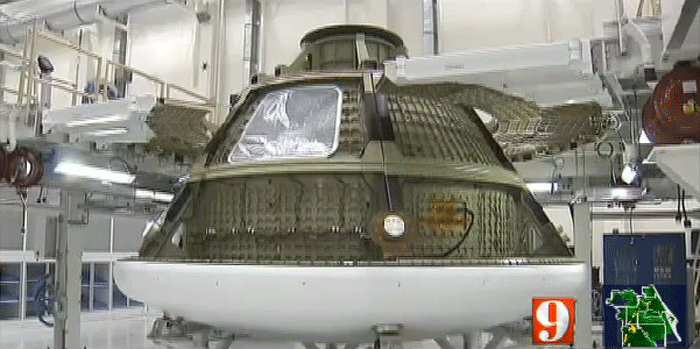
.
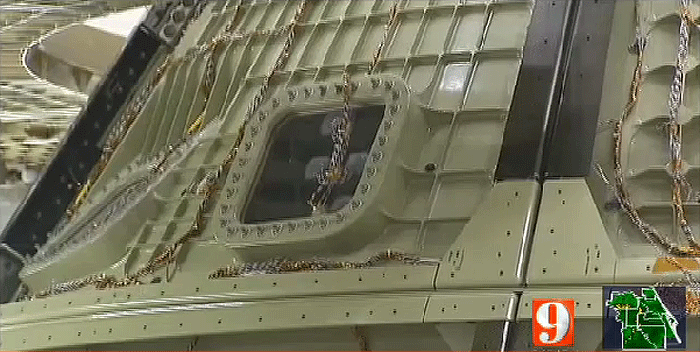
KENNEDY SPACE CENTER, Fla. — Channel 9 was given an up-close look at NASA's Orion spacecraft, which will make its first trip to space in December.
The next-generation spacecraft will have its first unmanned test flight by the end of 2014. Brevard County reporter Melonie Holt got a first look at the powerful rocket boosters that will carry Orion into space.
"We're excited about this mission. We talk about the stepping stones to getting to Mars and for us this EFT mission is so important to us," NASA Associate Administrator Robert Lightfoot said.
The boosters are being held in the Horizontal Integration Facility.
"There's a lot of thrust needed to support this very important mission," Tony Taliancich, with United Launch Alliance, said.
An exploration test flight was pushed back to December to accommodate a pair of Air Force launches earlier in the year. But Kennedy Space Center Director Bob Cabana said Orion will be ready by its original September launch window.
"It's going to be complete on time. These guys are working seven days a week. That vehicle is going to roll out of there a complete spacecraft," Cabana said.
During the test flight, Orion will travel 3,600 miles into space and orbit the Earth twice. The capsule will re-enter Earth's atmosphere at speeds approaching 20,000 miles per hour, generating temperatures as high as 4,000 degrees Fahrenheit, before splashing into the Pacific Ocean.
"Crews are going to fly in this capsule in 2017. It's just an exciting time for us at the agency," Cabana said.
.
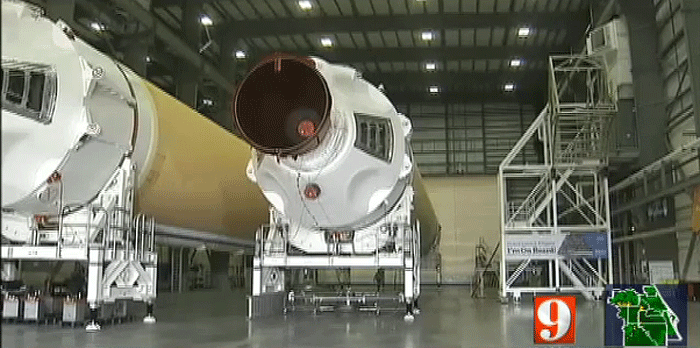
.
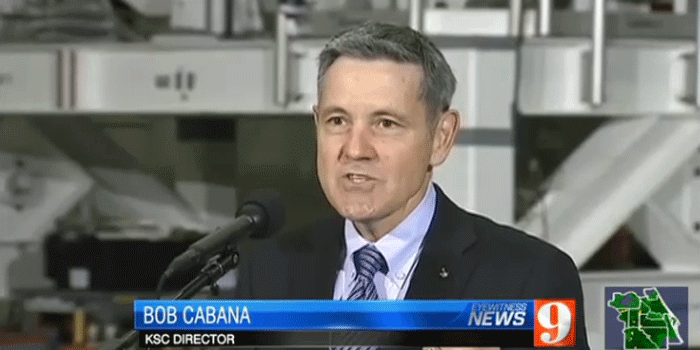
.
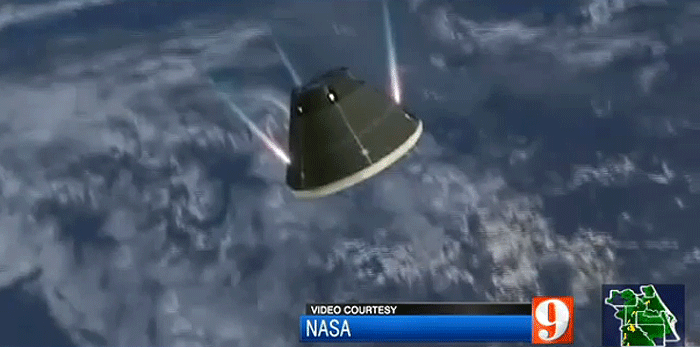
Quelle: WFTV
.
NASA delays Orion space capsule's first test
Crews roll out NASA's Orion space capsule in this undated photo. The space agency announced March 14 they were delaying the capsule's first test until December. (PHOTO/NASA, File)
.
CAPE CANAVERAL AIR FORCE STATION --
A test of NASA's next generation spacecraft, designed to take humans to an asteroid or Mars, is being delayed.
The space agency announced that it’s delaying the first test of the Orion space capsule until December.
The U.S. Air Force is bumping Orion’s September launch, so that it can send two national priority payloads to space first.
“We support our customers’ requirements,” said Tony Taliancich, with United Launch Alliance, the maker of the Delta IV rocket. “We provide a lot of options, those options for this particular situation were provided to both the Air Force and NASA and this is the order they chose.”
Two of the three boosters arrived earlier this month at the Cape Canaveral Air Force Station, where United Launch Alliance will assemble the Delta IV rocket.
Nearby, teams at Kennedy Space Center are working 7 days a week to get Orion ready for launch.
Orion and the Delta IV rocket will now launch for Exploration Flight Test 1 (EFT-1) in December.
The Orion capsule will be launched 3,600 miles into space, traveling 15 times father than the International Space Station.
This first mission will be unmanned, but it will test Orion’s electronic systems, the heat shield and its parachute before splashing down in the Pacific.
“We’re excited about this mission,” said NASA Associate Administrator Robert Lightfoot. “You know, we talk about the stepping stones getting to Mars that we’re trying to do here as an agency, and for us this EFT-1 test is so important for us.”
Orion is expected to be launched on NASA’s new heavy lift rocket, the Space Launch System, in 2017.
The first manned Orion mission won’t happen until 2021, when NASA wants to send humans to an asteroid.
NASA is hoping a Mars mission will happen in the 2030s.
Quelle: NEWS13
.
Update: 8.04.2014
.
Orion Avionics System Ready for First Test Flight
.
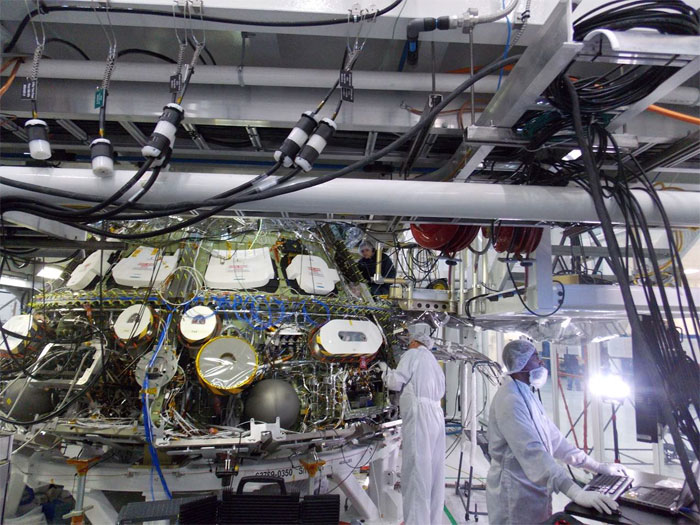
DENVER, Apr. 7, 2014 – Testing of the Orion spacecraft’s avionics system has concluded at the Lockheed Martin [NYSE: LMT] Operations & Checkout facility at Kennedy Space Center in Florida. After powering on and sending commands to more than 20 different critical systems installed on the spacecraft’s crew module, NASA and Lockheed Martin engineers have verified the avionics for Exploration Flight Test-1 (EFT-1) are ready to support a successful flight and re-entry of the spacecraft.
Following the initial power on of the Vehicle Main Computer in October, engineers have since methodically installed additional harnessing, wiring and electronics onto the crew module—completing the avionics system that serves as the eyes, ears and brains of the spacecraft. During these tests, engineers one-by-one activated and sent commands to the pyrotechnics, batteries, thermal control, cameras, guidance and navigation, propulsion, and environmental control life support systems, all while evaluating signal quality, on-board system responses, and data production.
“Each and every one of these systems is critical to mission success and they must perform flawlessly to ensure the safety of future crews,” said Cleon Lacefield, Lockheed Martin Orion program manager. “Now that we’ve finished functional testing, the team will conduct performance testing and turn on all the systems at once, simulating the spacecraft’s operations during EFT-1.”
During Orion’s test flight, the uncrewed spacecraft will launch on the Delta IV Heavy and will travel 3,600 miles beyond low Earth orbit. That same day, Orion will return to Earth at a speed of approximately 20,000 mph for a splashdown in the Pacific Ocean. EFT-1 will provide engineers with critical data about Orion's heat shield, flight systems, and capabilities to validate designs of the spacecraft before it begins carrying humans to new destinations in deep space.
Headquartered in Bethesda, Md., Lockheed Martin is a global security and aerospace company that employs approximately 115,000 people worldwide and is principally engaged in the research, design, development, manufacture, integration and sustainment of advanced technology systems, products and services. The Corporation’s net sales for 2013 were $45.4 billion.
Quelle: Lockheed-Martin
.
Update: 24.04.2014
.
NASA Tests Orion’s Parachute Performance over Arizona while Work Progresses in Florida
.
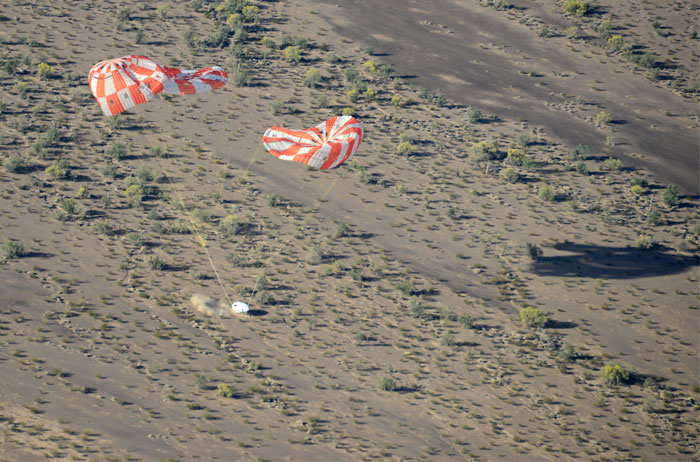
The team designing the parachute system for NASA’s Orion spacecraft has demonstrated almost every parachute failure they could imagine. But on April 23, they tested how the system would perform if the failure wasn’t in the parachutes.
Orion is the safest spacecraft ever built to carry humans, and its Launch Abort System can take a good deal of the credit for that distinction. In an emergency on the launch pad or during the early stages of ascent, it can activate in milliseconds to pull the crew to safety. Once it has pulled the crew away from the emergency, it’s up to the parachutes to bring them down for a safe landing.
“We hope we never have to use the parachutes this way,” said Chris Johnson, project manager for the parachutes. “We want to see them deploy after a successful mission every time. But we need to know they can perform in an emergency, too.”
In a pad abort or a low altitude launch abort, Orion’s three main parachutes would be called on to lower the crew module to the ground without the help of the two drogues that normally precede them. The parachute system won’t have as long to do the job since the spacecraft will be at much lower altitude than for a nominal reentry mission, and with the vehicle going slower, they won’t deploy as quickly. And on top of all of these factors, the crew module will be flying sideways when the parachutes deploy, instead of falling straight down as it does during reentry.
To simulate those conditions, a test version of Orion was dropped from a C-17 at 13,000 feet above the U.S. Army’s Yuma Proving Ground, with the main parachutes deploying soon after leaving the plane, before the capsule had a chance to straighten out. All the elements worked together and the parachutes reached a fully open state setting up a soft landing as expected. But the real value of the test will come with the data the engineers were able to gather from it.
“We wanted to record how long it took to inflate the parachutes in a launch pad abort scenario and collect data on how the different conditions affected the quality of the parachute deployment,” Johnson said. “With this test successfully completed, our next step is to dig into that information and use it to fine tune the launch abort trajectories for flight.”
In addition to the new test conditions, this was also the first time that the steel risers connecting the parachute lines to Orion were replaced with the textile risers that will be incorporated into future Orion spacecraft after Orion’s first flight this year. The new risers are lighter and more flexible – two qualities that will come in particularly handy when Orion is ready to carry humans into space.
While engineers continue to test Orion's parachutes for future missions, engineers at NASA's Kennedy Space Center in Florida continue to make progress on the Orion spacecraft being prepared for its December trip to space. Inside the Operations and Checkout Building high bay, the crew module is positioned on a special portable test chamber for multi-point random vibration testing. Accelerometers and strain gauges have been attached to Orion in various locations. During a series of tests, each lasting only 30 seconds, Orion is being subjected to gradually increasing levels of vibrations that simulate levels the vehicle will experience during launch, orbit and descent. The data will be reviewed to assess the health of the crew module.
Orion’s first flight will launch an uncrewed capsule 3,600 miles into space for a four-hour mission to test several of its most critical systems, including its parachutes. After making two orbits, Orion will return to Earth at almost 20,000 miles per hour and endure temperatures near 4,000 degrees Fahrenheit, before its parachutes slow it down for a landing in the Pacific Ocean.
Quelle: NASA
.
Update: 21.05.2014
.
NASA MAY BRING ORION'S TEST FLIGHT FORWARD
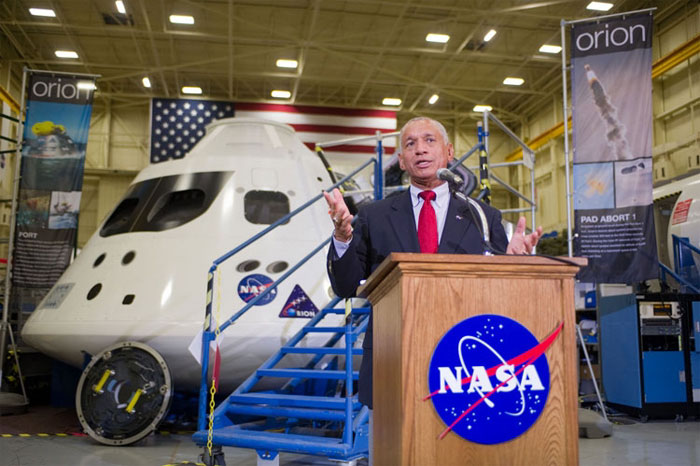
Sen—The maiden flight of NASA’s new Orion spacecraft could be brought forward to September, Administrator Charles Bolden has told Sen in an exclusive interview.
The unmanned mission, dubbed Exploration Flight Test-1 (EFT-1), is currently scheduled for December this year.
It was put back three months from the original target date to make way for the launch of military surveilance satellites for the US Air Force.
But speaking exclusively to Sen blogger Ken Kremer, former astronaut Bolden revealed that the original launch slot could be reinstated and NASA was keeping all options open.
The team of engineers and scientists are working to have the spacecraft in place to launch in September, whatever date is finally picked. “The vehicle will be ready to fly in September,” Bolden told Sen.
The Orion Multi-Purpose Crew Vehicle will be blasted into space on its test flight atop America’s most powerful rocket, the United Launch Alliance Delta IV Heavy.
It will fly further from Earth than any spacecraft designed for humans since the end of the Apollo programme, reaching a distance of 5,800 km (3,600 miles). An important part of the mission will be to test Orion’s heat shield when the capsule re-enters the atmosphere at a speed of around 32,000 kilometres per hour (20,000 mph).
Ken talked with Bolden, who flew four times on the space shuttle, including the mission to deploy the Hubble Space Telescope, at NASA’s Goddard Space Flight Center in Maryland.
Read the full interview in Ken’s blog for Sen.:
http://www.sen.com/ken-kremer/orion-team-keeps-options-open-for-september-launch-interview-with-nasa-administrator-bolden
,
Update: 22.05.2014
.
Orion In Final Assembly At Kennedy Space Center
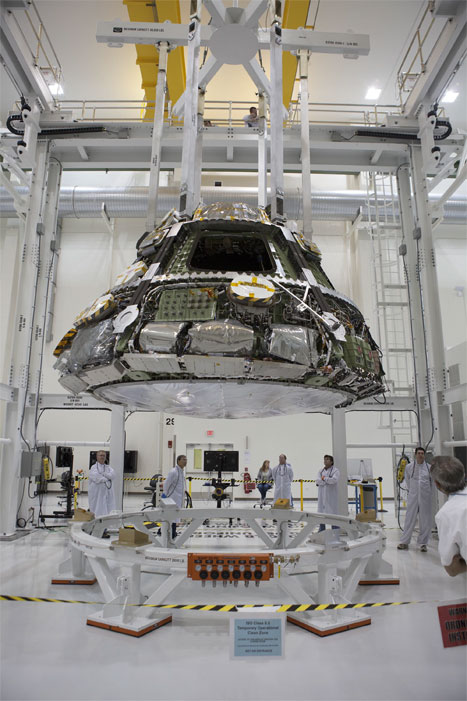
The Orion crew module is placed in a lift fixture to prepare for the heat shield installation.
.
Team Progressing Toward Exploration Flight Test-1
DENVER, May 21, 2014 –Lockheed Martin [NYSE: LMT] and NASA engineers have started the process of installing the largest heat shield ever built onto the Orion spacecraft’s crew module. The heat shield installation marks one of the final steps in the spacecraft’s assembly leading up to its first test flight, Exploration Flight Test-1 (EFT-1), later this year.
EFT-1 will provide engineers data about the heat shield’s ability to protect the crew module from the extreme 4000-degree heat of reentry and an ocean splashdown following Orion’s 20,000 mph reentry from space. In addition, key systems such as avionics, separation events, attitude control and guidance, parachute deployment, and ground operations will be evaluated. Comprehensive data from the test flight will influence design decisions most critical to crew safety to lower risks and safely carry humans on future missions to deep space.
The team remains on schedule to complete the following milestones for the Dec. 4, 2014 launch date:
The crew module and service module will mate together and will undergo functional testing
The backshell tiles and forward bay cover will be installed onto the crew module
The crew module and service module will mate to the Delta IV Heavy second stage adapter
The spacecraft will be fueled and serviced at the Kennedy Space Center Payload Hazardous Servicing Facility
The launch abort system will be stacked on top of the spacecraft
The spacecraft will be prepped and transported to Launch Pad 37 where Lockheed Martin and United Launch Alliance will perform pad integration and launch operations
“This team has done a great job keeping us on track for Orion’s first test flight,” said Cleon Lacefield, Lockheed Martin vice president and Orion program manager. “That’s no easy task when you’re designing and building a unique vehicle for human exploration of deep space.”
Quelle: Lockheed Martin
.
Update: 6.06.2014
.
NASA's Orion Spacecraft is Ready to Feel the Heat
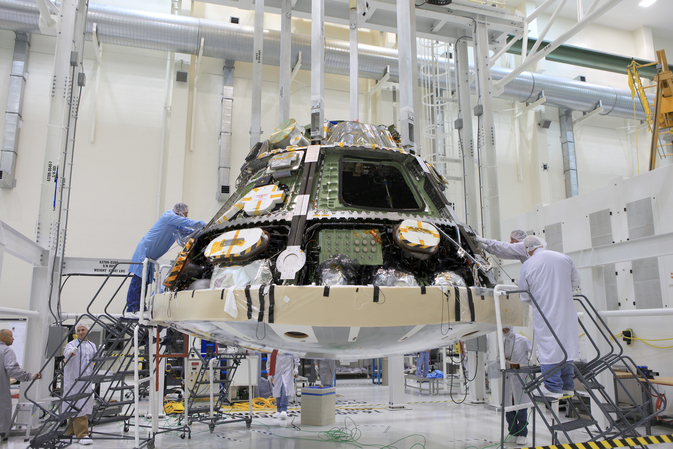
Engineers completed installing the heat shield on NASA’s Orion spacecraft ahead of its first trip to space in December. The flight test will send an uncrewed Orion 3,600 miles into space before returning it to Earth for the splashdown in the Pacific Ocean. The heat shield will help protect the Orion crew vehicle from temperatures of about 4,000 degrees Fahrenheit during its reentry into Earth’s atmosphere.
.
NASA and Lockheed Martin engineers have installed the largest heat shield ever constructed on the crew module of the agency's Orion spacecraft. The work marks a major milestone on the path toward the spacecraft's first launch in December.
"It is extremely exciting to see the heat shield in place, ready to do its job," said Mark Geyer, Orion Program manager at NASA's Johnson Space Center in Houston. "The heat shield is such a critical piece, not just for this mission, but for our plans to send humans into deep space."
The heat shield is made of a coating called Avcoat, which burns away as it heats up in a process called ablation to prevent the transfer of extreme temperatures to the crew module. The Avcoat is covered with a silver reflective tape that protects the material from the extreme cold temperatures of space.
Orion’s flight test, or Exploration Flight Test-1, will provide engineers with data about the heat shield's ability to protect Orion and its future crews from the 4,000-degree heat of reentry and an ocean splashdown following the spacecraft’s 20,000-mph reentry from space.
Data gathered during the flight will inform decisions about design improvements on the heat shield and other Orion systems, and authenticate existing computer models and new approaches to space systems design and development. This process is critical to reducing overall risks and costs of future Orion missions -- missions that will include exploring an asteroid and Mars.
Orion's flight test also will provide important data for the agency’s Space Launch System (SLS) rocket and ocean recovery of Orion. Engineers at NASA’s Marshall Space Flight Center in Huntsville, Alabama, have built an advanced adapter to connect Orion to the United Launch Alliance Delta IV Heavy rocket that will launch the spacecraft during the December test. The adapter also will be used during future SLS missions. NASA’s Ground Systems Development and Operations Program, based at Kennedy Space Center in Florida, will recover the Orion crew module with the U.S. Navy after its splashdown in the Pacific Ocean.
The heat shield was manufactured at Lockheed Martin's Waterton Facility near Denver. Construction was completed at Textron Defense Systems near Boston before the heat shield was shipped to the Operations and Checkout Building at Kennedy, where Orion is being assembled.
In the coming months, the Orion crew and service modules will be joined and put through functional tests before the spacecraft is transported to Kennedy’s Payload Hazardous Servicing Facility for fueling. The spacecraft then will be transferred to the Launch Abort System (LAS) Facility to be connected to the LAS before making the journey to Cape Canaveral’s Space Launch Complex 37 for pad integration and launch operations.
.
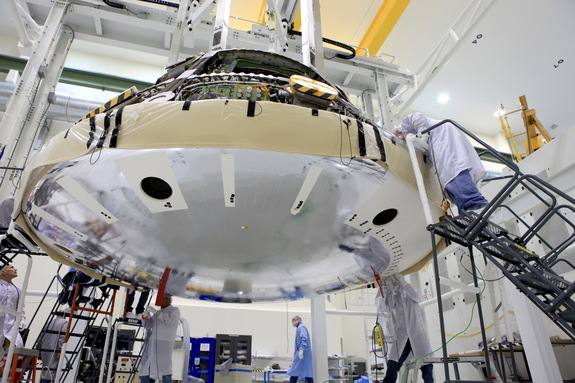
NASA's Orion spacecraft boasts the world's largest heat shield at 16.5 feet (5 meters) in diameter. Image uploaded June 5, 2014.
Quelle: NASA
.
10.06.2014
.
Boeing shows off crew capsule at KSC
CAPE CANAVERAL -- Six months ago, Kennedy Space Center's former shuttle engine shop looked to Chris Ferguson like an abandoned New York City subway station.
Today, the floors and walls gleamed white and newly installed air conditioning pumped through the bays where shuttle main engines were serviced through the final mission, which Ferguson led three years ago next month.
He said his recent tweet of a photo of the refurbished site, where Boeing hopes to assemble CST-100 commercial crew capsules, received and enthusiastic and telling response.
"America wants their space program back," said Ferguson, director of crew and mission systems for Boeing's CST-100 program. "We're beginning to see the first vestiges of that, and it's good for the American public, it's good for the Florida economy."
Inside the production facility today, Boeing displayed a mockup of the capsule that the company hopes will end the gap in human spaceflight missions launched from Florida.
Coming less than two weeks after SpaceX unveiled a Dragon capsule designed to carry astronauts, the event was the latest building momentum towards NASA's selection of the companies that could fly astronauts to the International Space Station by 2017.
NASA's Commercial Crew Program plans to award one or more contracts in August or September.
U.S. Sen. Bill Nelson said Monday he expects NASA to select multiple winners if funding next year holds close to the $805 million the Senate has proposed.
.
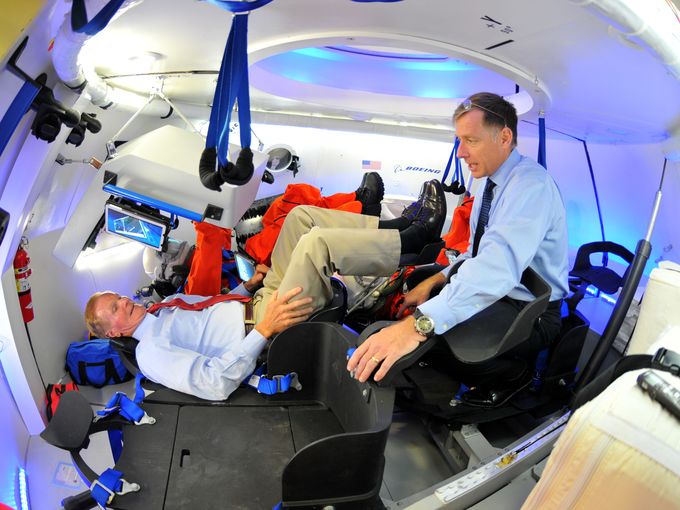
.
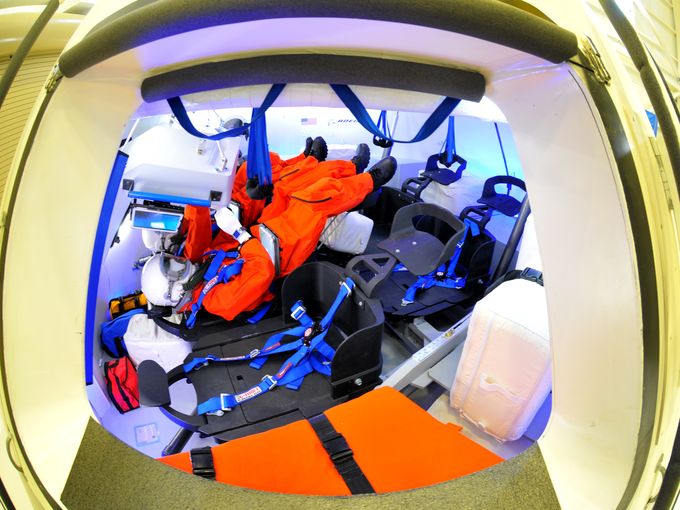
.
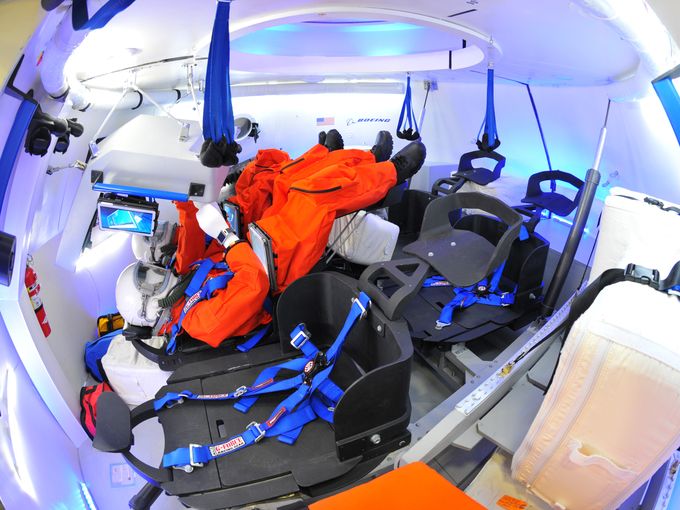
.
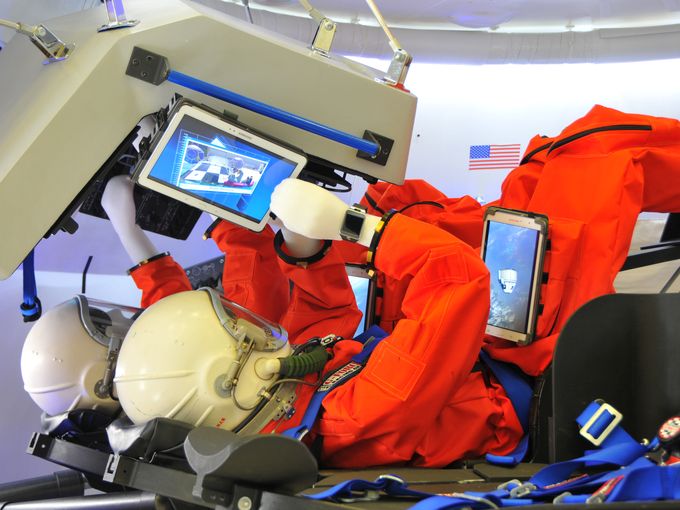
"That's enough money for NASA to do the competition for at least two (companies), and maybe more," he said. "That of course is up to NASA as they evaluate all the proposals."
In addition to Boeing's CST-100 and SpaceX's Dragon, the competition includes Sierra Nevada's Dream Chaser mini-shuttle.
NASA has contributed about $1.5 billion to the development of commercial crew vehicles since 2010. Boeing's roughly $600 million is the most received by any one company.
Nelson was the first to climb into one of the CST-100's five black, reclined seats, alongside two mock astronauts in orange pressure suits. Then a member of the House, Nelson flew on shuttle Columbia in January 1986.
The capsule featured an overhead panel of digital displays and switches and Samsung tablets for the crew, blue interior lighting and room to tuck small cargo bags.
"It's not going to be the space shuttle," said Ferguson. "It doesn't have the capability for 50,000 pounds of cargo. But what it brings to the table is a very safe ride to low Earth orbit for up to five American astronauts."
Boeing's formal presentation contrasted with the party-like atmosphere when SpaceX CEO Elon Musk recently unveiled Dragon Version 2 to a cheering crowd at the company's Southern California headquarters, shown via Webcast.
And unlike SpaceX, Boeing takes pride in the CST-100's use of proven rather than new technologies. Whereas the Dragon plans to use a futuristic precision powered landing system, the CST-100 will land on airbags.
Starting with an uncrewed test flight in January 2017, Boeing's CST-100 missions would launch from Cape Canaveral Air Force Station atop United Launch Alliance Atlas V rockets.
ULA officials on Monday showed off a model of the nearly 200-foot tall access tower that would support crewed missions from Launch Complex 41. Its completion is targeted for September 2016.
Although Boeing would only fly one or two missions a year for NASA, up to six CST-100 service modules could be processed simultaneously in the former engine shop. Crew modules would be assembled in an adjacent former shuttle hangar called Orbiter Processing Facility-3, where construction continued Monday.
The facilities, also including a nearby office building, are being renovated with the help of $20 million from the state of Florida.
Boeing has not decided how to proceed if it does not win a commercial crew contract, but Space Florida is confident another company would use the facilities if Boeing does not.
If it does, Boeing has said the program could create up to 550 local jobs that would start ramping up this fall as components for a test capsule arrived.
"I have a tremendous respect for the disciplined culture, the hard working people here at the Space Coast," said John Elbon, vice president and general manager of Boeing Space Exploration.
NASA once hoped to launch commercial crew missions in 2015, but funding has pushed that goal to late 2017. Russia's Soyuz spacecraft will offer the only crew access to the station until then.
Nelson encouraged NASA to try for missions sooner, but few believe the program can be accelerated at this point.
"I wish you'd target to 2016, because there is a whole bunch of us here, everyone in this audience, that wants to see Americans on American rockets, rocketing back into orbit," he said. "That can't come soon enough."
Quelle: Florida Today
.
Update: 11.06.2014
.
NASA's Orion Spacecraft Stacks Up for First Flight
.
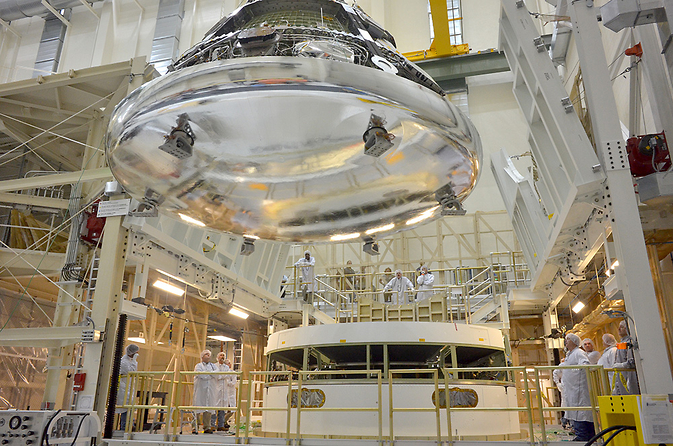
The Orion crew module for Exploration Flight Test-1 is shown in the Final Assembly and System Testing (FAST) Cell, positioned over the service module just prior to mating the two sections together. The FAST cell is where the integrated crew and service modules are put through their final system tests prior to rolling out of the Operations and Checkout Building at NASA's Kennedy Space Center in Florida for integration with its rocket. Technicians are in position to assist with the final alignment steps once the crew module is nearly in contact with the service module. In December, Orion will launch 3,600 miles into space in a four-hour flight to test the systems that will be critical for survival in future human missions to deep space.
.
With just six months until its first trip to space, NASA’s Orion spacecraft continues taking shape at the agency's Kennedy Space Center in Florida.
Engineers began stacking the crew module on top of the completed service module Monday, the first step in moving the three primary Orion elements –crew module, service module and launch abort system – into the correct configuration for launch.
"Now that we're getting so close to launch, the spacecraft completion work is visible every day," said Mark Geyer, NASA's Orion Program manager. "Orion's flight test will provide us with important data that will help us test out systems and further refine the design so we can safely send humans far into the solar system to uncover new scientific discoveries on future missions."
With the crew module now in place, the engineers will secure it and make the necessary power connections between to the service module over the course of the week. Once the bolts and fluid connector between the modules are in place, the stacked spacecraft will undergo electrical, avionic and radio frequency tests.
The modules are being put together in the Final Assembly and System Testing (FAST) Cell in the Operations and Checkout Facility at Kennedy. Here, the integrated modules will be put through their final system tests prior to rolling out of the facility for integration with the United Launch Alliance Delta IV Heavy rocket that will send it on its mission.
Orion is being prepared for its first launch later this year, an uncrewed flight that will take it 3,600 miles above Earth, in a 4.5 hour mission to test the systems critical for future human missions to deep space. After two orbits, Orion will reenter Earth’s atmosphere at almost 20,000 miles per hour before its parachute system deploys to slow the spacecraft for a splashdown in the Pacific Ocean.
Orion's flight test also will provide important data for the agency’s Space Launch System (SLS) rocket and ocean recovery of Orion. Engineers at NASA’s Marshall Space Flight Center in Huntsville, Alabama, have built an advanced adapter to connect Orion to the Delta IV Heavy rocket that will launch the spacecraft during the December test. The adapter also will be used during future SLS missions. NASA’s Ground Systems Development and Operations Program, based at Kennedy, will recover the Orion crew module with the U.S. Navy after its splashdown in the Pacific Ocean.
Quelle: NASA
.
Update: 14.06.2014
.
Kennedy Space Center director says Orion capsule will launch Dec. 6, defends NASA's exploration plan
Kennedy Space Center Director Robert Cabana speaking at the U.S. Space & Rocket Center in Huntsville, Ala., on June 12, 2014.
.
NASA will launch its Orion capsule the first time Dec. 6, Kennedy Space Center Director Robert Cabana said in Huntsville Thursday. That's the scheduled launch date, which could slip a few days, but NASA wants to test the capsule this year to keep its Space Launch System program on track.
Cabana said the capsule will be ready for the test earlier, but NASA has given up an earlier launch date to a national security mission. In the December flight, an uncrewed Orion will lift off atop a Delta IV Heavy rocket built by United Launch Alliance in Decatur, Ala., orbit the globe twice and splash down in the Pacific. NASA will be testing the capsule's control systems, heat shields and a new parachute system.
Cabana gave the timeline while delivering one of a series of "Pass the Torch" lectures on the American space program at the U.S. Space & Rocket Center Thursday. NASA has mastered near-Earth missions, he said, but it needs months in the more-distant "proving zone" of deep space to develop the systems needed for the trip to Mars. Some argue for a return to the moon, but Cabana pointed to the fiscal reality.
"If you look at NASA's budget, it increases by 1 percent for the next five years," Cabana said. "That's essentially a flat budget. We have be very cool and lay out a plan that's going to eventually get us to Mars."
The proposed asteroid redirect mission, where NASA would move part or all of an asteroid to a lunar orbit where astronauts could explore for months, is that plan, Cabana said. It has been criticized as uninspiring, but Cabana said it fits the budget and will help NASA develop the skills to go farther.
Cabana indirectly acknowledged critics who say NASA's decision to build the big rocket called the Space Launch System first takes too much discretionary income in that flat budget leaving too little for everything else needed to explore. He said, "We still have to build a habitability module and a lander and so on to eventually get to Mars in the 2030s."
But Cabana said the rocket will be what gets NASA anywhere in deep space. "Some folks call it the rocket to nowhere," Cabana said. "Well, man, that's the rocket to everywhere."
Quelle: AL
.
Update: 19.06.2014
.
Five Things We’ll Learn from Orion’s First Flight Test
All the superlatives associated with Orion's first mission this year – farthest a spacecraft for humans has gone in 40 years, largest heat shield, safest vehicle ever built – can be dazzling, no doubt. But the reason engineers are chomping at the bit for Orion's first mission is the promise of crucial flight test data that can be applied to the design for future missions. Orion only has two flight test opportunities before astronauts climb aboard for the first crewed mission in 2021 – so gleaning the maximum information possible from Exploration Flight Test (EFT)-1 in December (and later, Exploration Mission-1 in 2017) is of the highest priority. Here are the top five things the engineers will be paying attention to:
1. Launch Abort System Separation – The launch abort system (LAS) is a key reason that Orion is intended to become the safest spacecraft ever built. In an emergency it could activate to pull the crew module and the astronauts it will carry away from the launch pad and the rocket in milliseconds. Hopefully it’s never needed, and since no crew will fly on EFT-1 the rescue system won’t be active.
But even when a launch goes perfectly, the 904-pound LAS jettison motor has to perform flawlessly. If it doesn’t get rid of the LAS 6 minutes and 20 seconds into the mission, there will be no landing – the LAS protects the crew module during ascent, but to do so, it blocks the parachutes that allow Orion to safely splashdown.
The Launch Abort System separation is just the first of 17 separations or jettisons that have to happen exactly as planned for the mission to be successful.
2. Parachute Deployment – For EFT-1, Orion will travel 3,600 miles above the Earth so that when it performs its deorbit burn, it will come screaming back into the Earth’s atmosphere at almost 20,000 miles per hour. Before it splashes down in the Pacific Ocean, it needs to slow down to 1/1000th of its entry speed – a relatively gentle 20 miles per hour.
Earth’s atmosphere does its part to put on the brakes, but to make landing survivable, Orion relies on its parachute system – primarily two drogue parachutes and three massive mains that together would cover almost an entire football field. They’ve been tested on Earth; test versions of Orion have been dropped from airplanes with a multitude of failure scenarios programmed into the parachute deployment sequence in an effort to make sure that every possibly problem is accounted for.
But the sheer number of possible problems to be tested indicates how complicated the system is – each parachute must deploy at the exact right time, open to the exact right percentages in the exact right stages, and be cut away exactly as planned. And no test on Earth can exactly simulate what the spacecraft will really experience on its return from space.
3. Heat Shield Protection – Before the parachutes even get a chance to deploy, Orion has to make it safely through Earth’s atmosphere. The reason that Orion is traveling so far and coming back in so fast is to give the heat shield a good workout – the idea is to get as close as possible to the temperatures Orion would experience during a return from Mars. At the speed it will be traveling, the temperature should reach almost 4,000 degrees Fahrenheit. At that same temperature, a nuclear reactor would melt down.
Standing between the crew module and all that heat is no more than 1.6 inches of Avcoat, a material that’s designed to burn away rather than transfer the temperatures back to Orion. Some 20 percent of the Avcoat will erode during the spacecraft’s journey back to Earth, and although it’s not the first time the materials has been used for this purpose, at 16.5 feet wide, Orion’s heat shield is the largest ever built. Technicians filled with Avcoat each of the 320,000 honeycomb cells that make up the shield’s structure by hand, then machined them to the precise fractions of inches called for by the design. Getting it exactly right is all that will get Orion through one of the most dynamic periods of its mission.
4. Radiation Levels – Traveling 15 times farther into space than the International Space Station will take Orion beyond the radiation protection offered by Earth’s atmosphere and magnetic field. In fact, the majority of EFT-1 will take place inside the Van Allen Belts, clouds of heavy radiation that surround Earth. No spacecraft built for humans has passed through the Van Allen Belts since the Apollo missions, and even those only passed through the belts – they didn’t linger.
Future crews don’t plan to spend more time than necessary inside the Van Allen Belts, either, but long missions to deep space will expose them to more radiation than astronauts have ever dealt with before. EFT-1’s extended stay in the Van Allen Belts offers a unique opportunity to see how Orion’s shielding will hold up to it. Sensors will record the peak radiation seen during the flight, as well as radiation levels throughout the flight, which can be mapped back to geographic hot spots.
5. Computer Function – Orion’s computer is the first of its kind to be flown in space. It can process 480 million instructions per second. That’s 25 times faster than the International Space Station’s computers, 400 times faster than the space shuttle’s computers and 4,000 times faster than Apollo’s.
But to operate in space, it has to be able to handle extreme heat and cold, heavy radiation and the intense vibrations of launches, aborts and landings. And it has to operate through all of that without a single mistake. Just restarting the computer would take 15 seconds; and while that might sound lightning fast compared to your PC, you can cover a lot of ground in 15 seconds when you’re strapped to a rocket.
.
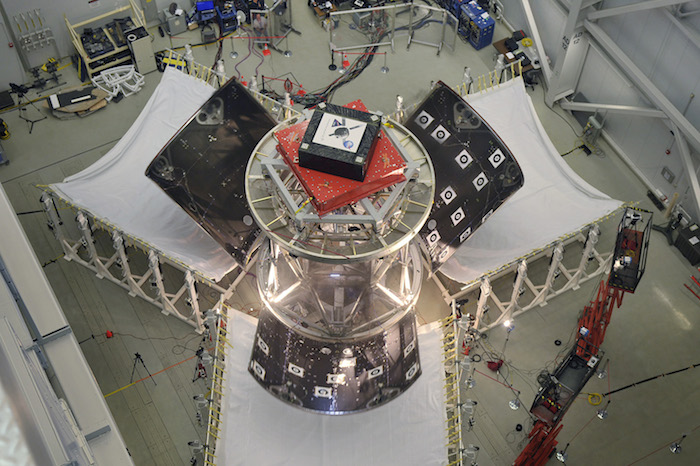
The three panels or fairings encapsulating a stand-in for Orion’s service module successfully detach and fall into the Fairing Catch System during a test Nov. 6, 2013 at Lockheed Martin’s facility in Sunnyvale, Calif.
Image Credit: Lockheed Martin
.
Quelle: NASA
.
Update: 25.06.2014
.
Parachutes for NASA's Orion Spacecraft Hit No Snags in Most Difficult Test
.
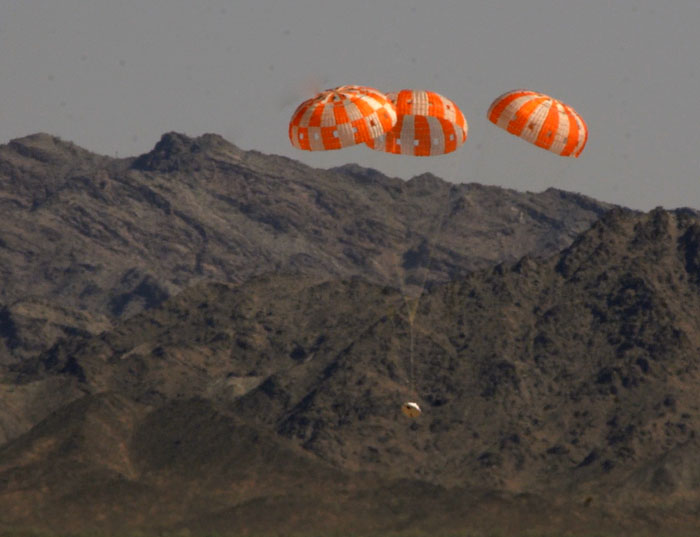
A test version of NASA’s Orion spacecraft descends under its three main parachutes above the U.S. Army Proving Ground in Arizona in the agency’s most difficult test of the parachutes system’s performance. NASA is preparing Orion for its first trip to space in December, a two-hour, four-orbit flight that will send an uncrewed spacecraft more than 3,600 miles into space before returning it to Earth to test the performance of many of the spacecraft’s critical systems needed to carry crew to deep space destinations in the future.
.
NASA completed the most complex and flight-like test of the parachute system for the agency's Orion spacecraft on Wednesday.
A test version of Orion touched down safely in the Arizona desert after being pulled out of a C-17 aircraft, 35,000 feet above the U.S. Army's Yuma Proving Ground. It was the first time some parachutes in the system had been tested at such a high altitude. Engineers also put additional stresses on the parachutes by allowing the test version of Orion to free fall for 10 seconds, which increased the vehicle's speed and aerodynamic pressure.
"We've put the parachutes through their paces in ground and airdrop testing in just about every conceivable way before we begin sending them into space on Exploration Flight Test (EFT)-1 before the year's done," said Orion Program Manager Mark Geyer. "The series of tests has proven the system and will help ensure crew and mission safety for our astronauts in the future."
After Orion's free fall, its forward bay cover parachutes deployed, pulling away the spacecraft's forward bay cover, which is critical to the rest of the system performing as needed. The forward bay cover is a protective shell that stays on the spacecraft until it has reentered Earth's atmosphere. The parachutes that slow Orion to a safe landing speed are located under the cover, so the cover must be jettisoned before they can be unfurled.
Engineers also rigged one of the main parachutes to skip the second phase of a three-phase process of unfurling each parachute, called reefing. This tested whether one of the main parachutes could go directly from opening a little to being fully open without an intermediary step, proving the system can tolerate potential failures.
The test also marked the last time the entire parachute sequence will be tested before Orion launches into space in December on its first space flight test, EFT-1. During the flight, an uncrewed Orion will travel 3,600 miles into space, farther than any spacecraft built to carry humans has been in more than 40 years. Orion will travel at the speed necessary to test many of the systems critical to NASA's ability to bring astronauts home safely from missions to deep space, including an asteroid and eventually Mars.
During its return to Earth, Orion will reach a speed of up to 20,000 mph and experience temperatures near 4,000 degrees Fahrenheit. Once Orion has made it through the atmosphere, the parachute system, with two drogue parachutes and three massive main parachutes that together cover almost an entire football field will be responsible for slowing it down to just 20 mph for a safe splashdown in the Pacific Ocean.
Orion's next parachute test is set for August and will test the combined failure of one drogue parachute and one main parachute, as well as new parachute design features. It is one of three remaining tests needed to demonstrate the system's capability for human missions, but does not need to be completed before Orion's first flight later this year.
Quelle: NASA
.
Update: 2.08.2014
.
NASA Prepares for Second Orion Underway Recovery Test
.
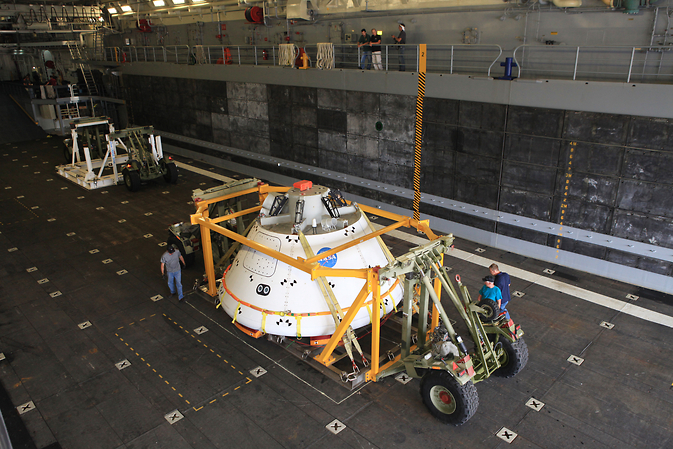
At the U.S. Naval Base San Diego in California, the Orion boilerplate test vehicle and support hardware are secured in the well deck of the USS Anchorage on July 29, 2014 for Underway Recovery Test 2. NASA, Lockheed Martin and the U.S. Navy will conduct tests in the Pacific Ocean to prepare for recovery of the Orion crew module, forward bay cover and parachutes on its return from a deep space mission. The second underway recovery test will allow the teams to demonstrate and evaluate the recovery processes, procedures, new hardware and personnel in open waters. The Ground Systems Development and Operations Program is conducting the underway recovery tests.
.
For NASA’s new Orion spacecraft, part of getting ready for its first launch is getting ready for its first splashdown.
Orion is the exploration spacecraft designed to carry astronauts to destinations not yet explored by humans, including an asteroid and Mars. It will have emergency abort capability, sustain the crew during space travel and provide safe re-entry from deep space return velocities.
After traveling 3,600 miles into space in December on the uncrewed Exploration Flight Test-1, Orion will return to Earth at a speed of 20,000 miles per hour and endure temperatures near 4,000 degrees Fahrenheit before landing in the Pacific Ocean. For the team tasked with recovering it, that is where the work begins.
NASA and Orion prime contractor Lockheed Martin are teaming up with the U.S. Navy and Department of Defense's Human Space Flight Support Detachment 3 to test techniques for recovering Orion from the water during Underway Recovery Test (URT) 2, Aug. 1-4, off the coast of San Diego, California.
URT 2 will pick up where URT 1 left off. During that first underway recovery test in February, dynamic conditions caused activities to conclude before all of the test objectives were met. Since then, the team has been working on concepts that would allow them to safely recover Orion despite such conditions.
"During this test, the team will investigate alternative procedures and recovery methods," said Mike Generale, Orion Recovery Operations manager and Recovery Test director at NASA's Kennedy Space Center in Florida. "One of the goals of the test is to have a primary and alternate means of recovering the Orion crew module for Exploration Flight Test-1 later this year."
The data gathered during Exploration Flight Test-1 will influence design decisions, validate existing computer models and innovative new approaches to space systems development, and reduce overall mission risks and costs for later Orion flights. The recovery of the vehicle is one of the things the flight will test, and the underway recovery tests prepare the combined NASA, Lockheed, and U.S. Navy team for the task.
For URT 2, the Orion test vehicle will be loaded into the well deck of the USS Anchorage (LPD 23), and the team will head out to sea, off the coast of San Diego, in search of sea conditions to support test needs. New support equipment developed for URT 2 will accompany the test vehicle.
New hardware includes an air bag system for the Crew Module Recovery Cradle and a load-distributing collar for placement around the crew module. The Prototype Laboratory at Kennedy designed a new device called the Line Load Attenuation Mechanical Assembly (LLAMA) that limits the tending-line forces for the Navy line handlers as Orion is guided into the ship's well deck.
Tending line snubbers, a kind of commercially available rubber shock absorbers sailors use for tending lines, also will be tested. In case the seas are too rough to secure the crew module in the recovery cradle and a contingency recovery is needed, a set of rubber bumpers were developed to provide a mat on the deck of the recovery ship for use. A lifting sling will be on hand for recovery by crane.
"Each of the new pieces of hardware will be evaluated for its relative merits, and the best solutions will be tested during URT 3 in September to discover the limits of their capabilities and suitability for Orion's Exploration Flight Test-1 in December," Generale said.
All of this testing ensures NASA can retrieve the Orion capsule safely because it helps the team understand how to adjust for various water conditions and contingency scenarios.
.
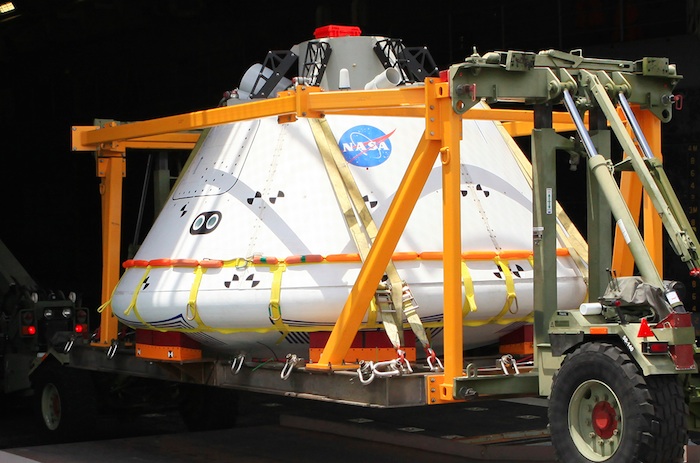
At the U.S. Naval Base San Diego in California, the Orion boilerplate test vehicle and support hardware are loaded in the well deck of the USS Anchorage on July 29, 2014 for Underway Recovery Test 2.
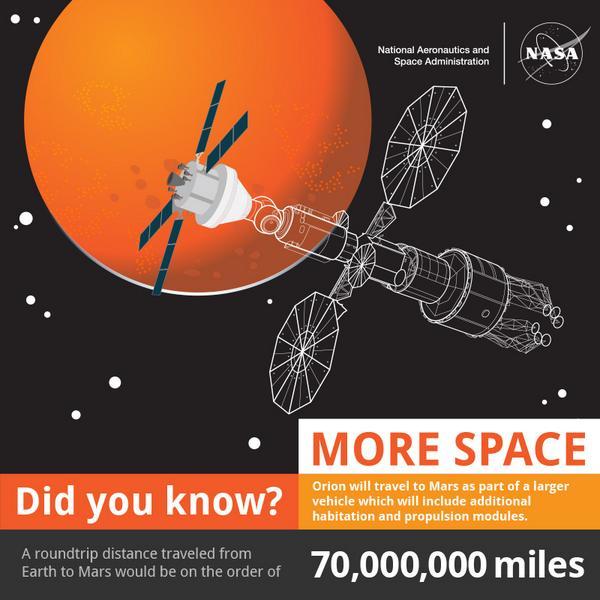
All the superlatives associated with Orion's first mission this year – farthest a spacecraft for humans has gone in 40 years, largest heat shield, safest vehicle ever built – can be dazzling, no doubt. But the reason engineers are chomping at the bit for Orion's first mission is the promise of crucial flight test data that can be applied to the design for future missions. Orion only has two flight test opportunities before astronauts climb aboard for the first crewed mission in 2021 – so gleaning the maximum information possible from Exploration Flight Test (EFT)-1 in December (and later, Exploration Mission-1 in 2017) is of the highest priority. Here are the top five things the engineers will be paying attention to:
1. Launch Abort System Separation – The launch abort system (LAS) is a key reason that Orion is intended to become the safest spacecraft ever built. In an emergency it could activate to pull the crew module and the astronauts it will carry away from the launch pad and the rocket in milliseconds. Hopefully it’s never needed, and since no crew will fly on EFT-1 the rescue system won’t be active.
But even when a launch goes perfectly, the 904-pound LAS jettison motor has to perform flawlessly. If it doesn’t get rid of the LAS 6 minutes and 20 seconds into the mission, there will be no landing – the LAS protects the crew module during ascent, but to do so, it blocks the parachutes that allow Orion to safely splashdown.
The Launch Abort System separation is just the first of 17 separations or jettisons that have to happen exactly as planned for the mission to be successful.
2. Parachute Deployment – For EFT-1, Orion will travel 3,600 miles above the Earth so that when it performs its deorbit burn, it will come screaming back into the Earth’s atmosphere at almost 20,000 miles per hour. Before it splashes down in the Pacific Ocean, it needs to slow down to 1/1000th of its entry speed – a relatively gentle 20 miles per hour.
Earth’s atmosphere does its part to put on the brakes, but to make landing survivable, Orion relies on its parachute system – primarily two drogue parachutes and three massive mains that together would cover almost an entire football field. They’ve been tested on Earth; test versions of Orion have been dropped from airplanes with a multitude of failure scenarios programmed into the parachute deployment sequence in an effort to make sure that every possibly problem is accounted for.
But the sheer number of possible problems to be tested indicates how complicated the system is – each parachute must deploy at the exact right time, open to the exact right percentages in the exact right stages, and be cut away exactly as planned. And no test on Earth can exactly simulate what the spacecraft will really experience on its return from space.
3. Heat Shield Protection – Before the parachutes even get a chance to deploy, Orion has to make it safely through Earth’s atmosphere. The reason that Orion is traveling so far and coming back in so fast is to give the heat shield a good workout – the idea is to get as close as possible to the temperatures Orion would experience during a return from Mars. At the speed it will be traveling, the temperature should reach almost 4,000 degrees Fahrenheit. At that same temperature, a nuclear reactor would melt down.
Standing between the crew module and all that heat is no more than 1.6 inches of Avcoat, a material that’s designed to burn away rather than transfer the temperatures back to Orion. Some 20 percent of the Avcoat will erode during the spacecraft’s journey back to Earth, and although it’s not the first time the materials has been used for this purpose, at 16.5 feet wide, Orion’s heat shield is the largest ever built. Technicians filled with Avcoat each of the 320,000 honeycomb cells that make up the shield’s structure by hand, then machined them to the precise fractions of inches called for by the design. Getting it exactly right is all that will get Orion through one of the most dynamic periods of its mission.
4. Radiation Levels – Traveling 15 times farther into space than the International Space Station will take Orion beyond the radiation protection offered by Earth’s atmosphere and magnetic field. In fact, the majority of EFT-1 will take place inside the Van Allen Belts, clouds of heavy radiation that surround Earth. No spacecraft built for humans has passed through the Van Allen Belts since the Apollo missions, and even those only passed through the belts – they didn’t linger.
Future crews don’t plan to spend more time than necessary inside the Van Allen Belts, either, but long missions to deep space will expose them to more radiation than astronauts have ever dealt with before. EFT-1’s extended stay in the Van Allen Belts offers a unique opportunity to see how Orion’s shielding will hold up to it. Sensors will record the peak radiation seen during the flight, as well as radiation levels throughout the flight, which can be mapped back to geographic hot spots.
5. Computer Function – Orion’s computer is the first of its kind to be flown in space. It can process 480 million instructions per second. That’s 25 times faster than the International Space Station’s computers, 400 times faster than the space shuttle’s computers and 4,000 times faster than Apollo’s.
But to operate in space, it has to be able to handle extreme heat and cold, heavy radiation and the intense vibrations of launches, aborts and landings. And it has to operate through all of that without a single mistake. Just restarting the computer would take 15 seconds; and while that might sound lightning fast compared to your PC, you can cover a lot of ground in 15 seconds when you’re strapped to a rocket.
Quelle: NASA
.
Update: 8.08.2014
.
NASA, Navy Prepare for Orion Spacecraft to Make a Splash
.
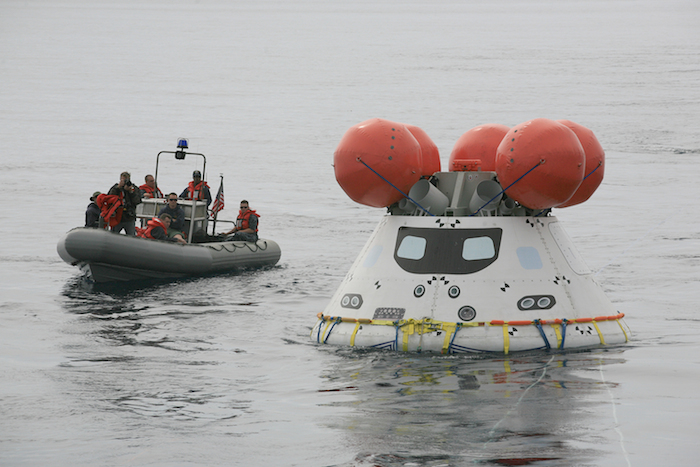
U.S. Navy personnel use a rigid hull inflatable boat to approach the Orion boilerplate test article during an evolution of the Underway Recovery Test 2 in the Pacific Ocean off the coast of San Diego, California on Aug. 2, 2014.
Image Credit: NASA/Kim Shiflett
.
A team of technicians, engineers, sailors and divers just wrapped up a successful week of testing and preparing for various scenarios that could play out when NASA's new Orion spacecraft splashes into the Pacific Ocean following its first space flight test in December.
After enduring the extreme environment of space, Orion will blaze back through Earth's atmosphere at speeds near 20,000 mph and temperatures approaching 4,000 degrees Fahrenheit. Its inaugural journey will end in the Pacific, off the Southern California coast, where a U.S. Navy ship will be waiting to retrieve it and return it to shore.
"We learned a lot about our hardware, gathered good data, and the test objectives were achieved,” said Mike Generale, NASA recovery operations manager in the Ground Systems Development and Operations Program. “We were able to put Orion out to sea and safely bring it back multiple times. We are ready to move on to the next step of our testing with a full dress rehearsal landing simulation on the next test."
NASA and Orion prime contractor Lockheed Martin teamed up with the U.S. Navy and the Defense Department's Human Space Flight Support Detachment 3 to try different techniques for recovering the 20,500-pound spacecraft safely during this second "underway recovery test." To address some of the lessons learned from the first recovery test in February, the team brought new hardware to test and tested a secondary recovery method that employs an onboard crane to recover Orion, as an alt
5824 Views