12.10.2021
COLORADO SPRINGS, Co. — “There is no spoon.”
So said a bald child in a toga to Keanu Reeves in the 1999 sci-fi flick “The Matrix,” which (spoiler alert) depicts a dystopian future where most of humanity exists within a digital simulation.
It’s also the title of a manifesto on digital acquisitions by the former assistant secretary of the U.S. Air Force for acquisition, technology and logistics, Will Roper. Released in 2020 and littered with Matrix references (and designed with a green and black color scheme reminiscent of the movie), the 19-page document outlines how and why the Department of the Air Force must use digital simulations and models to design and build its systems.
“The last area that we have to have strategic agility is in being able to computerize or virtualize everything about our development and production, assembly, even sustainment of systems so that we can finally get past the tyranny of the real world and take learning and feedback into the digital one,” Roper said in a Matrix-themed presentation nearly a year ago.
The promises of a digital ecosystem — faster development, integrated assembly and the ability to test systems before they’re built — are appealing to the Department of Defense, which frequently struggles with cost overruns and significant delays for its space systems.
Roper has since left government, but the digital revolution continues, and the U.S. Space Force wants to lead the way.
In May, Chief of Space Operations Gen. Jay Raymond announced the new service’s intent to be the world’s first fully digital service, adopting digital engineering practices to transform how the military designs, buys and builds systems.
The Space Force has abandoned Roper’s Matrix-heavy framing, but it’s using the same basic framework: hyper-realistic simulations of the environment in which its satellites will operate, and digital twins to help design and build architectures, constellations, satellites, payloads, ground systems and more to ensure operators can deliver the space-based capabilities needed by war fighters around the world.
It’s an ambitious vision, but the Space Force is taking steps to implement it, and industry says it’s ready.
Enter the Matrix
The digital revolution begins at the very start of the acquisition process: force design.
That step is the big-picture determination of the Space Force’s needs and the best architecture to address its mission. The Space Warfighting Analysis Center (SWAC) will use high-fidelity simulations that can realistically depict the orbital environment, space and terrestrial weather, threats and the effects it anticipates encountering to create that force design, which can then be distilled into a set of requirements.
According to SWAC Director Andrew Cox, these simulations have to represent three main elements with high fidelity: the threat; the physical and engineering constraints; and the cost.
“The reason those three things are important is because as we are at the headwaters, feeding requirements into the budget process that’s run by [Lt. Gen. William] Liquori. We don’t want to hand him force designs that he’s building requirements off of and budgets off of that are unrealistic, that are not affordable and that are vulnerable,” Cox said at the Air Force Association’s Air, Space and Cyber Conference in September.
Liquori, who serves as the Space Force’s deputy chief of space operations for strategy, plans, programs, requirements and analysis, said those force designs and “performance envelopes” then move to his requirements team.
“The intent will be to put a wrapper on those to make a digital requirements package,” he said. “And then we pass that onto the acquisition community, who then will take and move that into digital engineering.”
Typically, the requirements would then go to the Space Force’s acquisition community, the vast bulk of which exists under Space Systems Command. The command would then look to industry for solutions.
But even here, the Space Force is doing things differently. The Space Warfighting Analysis Center is inviting industry to join its officials in an October classified business briefing, during which they plan to share the simulations and models that informed the force design. That will give contractors interested in working with the Space Force input at that big-picture level, using a common framework of the threats and the mission.
Fleshing out digital models
When the requirements are officially set, they’ll go to the acquisition community, which will work with contractors in a digital engineering environment. Instead of relying on the 2D blueprints that drove the space race in the 1950s and 1960s, digital engineering uses 3D virtual models.
So digital models are just 3D blueprints, right? Yes, but they’re much more. Experts say what they really do is put those requirements and designs into a single, shared, sophisticated place across the space enterprise.
“When we talk about the concept of digital, think about it from the standpoint of really understanding how to drive speed and effectivity along the entire value stream — whether you’re talking space, whether you’re talking aircraft, whether you’re talking computers and IT,” David Ray, senior vice president of the space business unit at SAIC, told C4ISRNET.
Perhaps the most significant promise of digital engineering is the ability to test systems in the design stage, well before they hit the factory floor. These digital twins of the real-life satellite are so detailed and accurate the Space Force can test them in a virtual version of space to see if they work.
“That granularity, what that does is allows you to validate and test as early as possible in the life cycle,” AGI’s digital engineering lead, Mark Visco, told C4ISRNET. “So what happened in the past, people were putting test and evaluation at the end. So they’d build everything, test it, and ‘Crap, it didn’t work’ or ‘That design was bad.’”
“Well now we can simulate with that level of real fidelity of: ‘Here’s what you’re actually going to try to build.’ I can test it virtually with computers — you know, within months of my design — and say: ‘Oh, that design is not going to work.’ And I can wring out all of the design flaws or all of the design shortcomings along the way before I start bending any metal or before I start creating circuit boards,” Visco added.
And at any point, said Liquori, the Space Force can take the digital twin and plug it back into the model-based systems engineering environment, replacing the placeholder system to see how it executes the mission.
The hope is this will address the common complaint about the Pentagon delivering systems that, well, don’t deliver.
Another promising aspect of model-based system engineering is the ability to quickly modify the design as requirements change, giving additional flexibility to contractors. That’s something Bill Gattle, L3Harris Technologies’ president of space systems, discovered through the firm’s work on the Missile Defense Agency’s Hypersonic and Ballistic Tracking Space Sensor.
“You can put a new requirement in and it will change the requirements, tell you what requirement is different, and it will tell you what hardware just broke or what you have to fix. So it’s all interconnected, and you can do that in a day,” Gattle said. “Versus today, if you were to do that on a mechanical system that we’ve built five years ago, [it] would take us weeks to figure out what exactly that requirement is without all that stuff.”
Model-based system engineering allows for the quick modification of a design as requirements change, something L3Harris Technologies noticed during work on the Missile Defense Agency’s Hypersonic and Ballistic Tracking Space Sensor. (L3Harris Technologies)
New artificial intelligence tools also speed up the design process, automatically running through a dizzying number of engineering options to find the best system for a user’s needs. In one instance, recalled AGI’s Visco, his company was able to use digital modeling to go through tens of thousands of design options with a customer. By inputting the customer’s requirements and priorities, the model automatically updates to offer the best design options. That sort of design work was virtually impossible in the analog days, Visco added.
Today, humans aren’t needed for whole steps of the design process. Engineers can take advantage of generative design, where they feed requirements into a software tool that automatically designs a piece to fit a need. The process is mostly used for simple tasks, like designing a physical arm to hold an antenna on a satellite, but that frees up human engineers to tackle harder problems, like designing the actual antenna.
“We’re doing our first usage of those generative designs and building them into systems today. We’re in those infancy steps,” said Lockheed Martin’s Johnathon Caldwell, the company’s vice president of business innovation, transformation and enterprise excellence.
There’s even talk, said Gattle, of the Space Force switching requirements late in the design process to see how well companies’ digital engineering solutions can respond.
But it’s not just the Space Force that will be able to interact with digital twins. An important benefit of digital engineering is collaboration without in-person meetings, said Ray. Engineering teams from dispersed locations can simultaneously access the digital twin. When one team plugs in a new part to the digital twin, other teams can see how the change affects or breaks their contribution.
Video game training?
The digital revolution doesn’t end with acquisitions. Lt. Gen. Chance Saltzman, the Space Force’s chief operations officer, said those virtual environments and digital models will be integral to the service’s efforts to train guardians — the title given to Space Force personnel.
The service must build a virtual test and training infrastructure to give operators experience with systems and validate their tactics against a “formidable array of threats that they will face in the field,” Saltzman said.
“Finally, the virtual environment must include digital twins of our weapon systems, realistic space weather models, and interactive simulators that connect red/blue forces,” he explained Sept. 21 during the Air Force Association conference. “What I have in mind should look more like an augmented reality video game. We need to take advantage of this moving technology. We need to put our operators in their domain to interact with the system and see/feel the effects of the consequences of their actions.
“Because our live operations are a virtual experience, a virtual training environment can be very realistic,” Saltzman added.
Comparing this theoretical virtual environment with a popular football video game his son plays, he said the training would be like the franchise mode, where users build a team and set the tactics, but don’t have to control individual players. Likewise, space operators don’t need to learn how to control satellites with a joystick. What they do need to do is learn how to build the right set of capabilities and formulate the best tactics to use against any given opponent.
“Imagine a game where you’re immersed in a struggle to preserve your mission — say satellite communications — against an adversary attempting to degrade relations. You make decisions. The game executes the tactics. We get real time feedback on what is working, what is not. You adjust. You make more decisions. All the while, player two — the red team [causing a satellite communications] jam — is executing their tactics to deny your block communications. Someone wins, someone loses. Both debrief, and we learn from their mistakes,” Saltzman said.
Just like the virtual environment the Space Warfighting Analysis Center will use to design capability architectures, this training environment will host digital twins of Space Force systems, high-fidelity effects, a realistic depiction of space weather and the orbital environment, and terrestrial weather that could affect missions.
Paul Tilghman, the senior director of Azure Spectrum Technologies at Microsoft, agrees with Saltzman.
During the Air Force Association conference, he said the Unreal Engine, a game creation platform that serves as the basis of hundreds of video games, could be adapted by the Space Force. With the right inputs, it could be used to create a digital environment with accurate physics, weather and threats.
The adoption of cloud computing in gaming could also point the way for the Space Force. Cloud gaming, wherein processing of data in video games is conducted at remote servers, enables users to play games without owning the newest console or expensive hardware. If the Space Force’s digital revolution is to be as ubiquitous as officials insist, it could be more sensible to rely on the cloud rather than install advanced hardware to run the high-fidelity simulations for every user or location.
“This is a big opportunity where I think computing power from the cloud can help,” said Tilghman, whose employer sells cloud services to several space companies.
Industry adoption
The Space Force announced its digital intentions in May, but digital engineering has been around for years. Its use within the DoD, however, is limited. Roper’s manifesto describes only three programs as “radically digital”: the T-7A Red Hawk aircraft, the Ground Based Strategic Deterrent weapon system and the Next Generation Air Dominance fighter.
“Space Force has the … unique opportunity that they’re trying to stand up a new service,” Caldwell, the Lockheed executive, said. “It doesn’t have to have all of the heritage bureaucracy … and I think they’ve done really well at trying to take advantage of the moment.”
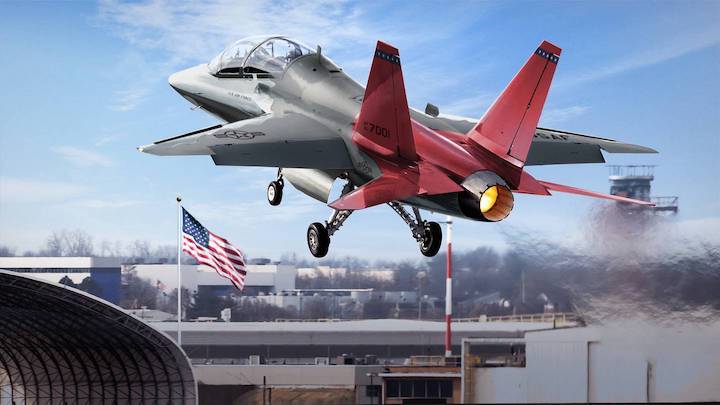
:quality(70)/cloudfront-us-east-1.images.arcpublishing.com/mco/KXUXS7WQ6NHRPA4TKJRO44SF3A.jpg)
Although digital engineering has been around for years, its use within the Pentagon is limited. Will Roper’s manifesto described only three programs as “radically digital” — one being the T-7A Red Hawk. (Boeing)
The space industry, Caldwell added, is at various stages of “crawl, walk, run” when it comes to adopting digital engineering. Even at Lockheed Martin, he said, diverse programs have different levels of digital involvement. For instance, while the company has integrated digital processes throughout the Next Generation Interceptor Program, others only use parts of the digital thread.
Other contractors agreed digital adoption varies across industries, companies and even internal programs.
“I’d say better practices are evolving. Everybody is on a journey,” Visco said.
Independent of government prompting, Visco added, AGI hired an independent firm to analyze the benefits of introducing digital engineering. The researchers found it could improve the cycle sixfold, so what would normally take six years could be done in one.
Carol Erikson, Northrop Grumman’s vice president of digital transformation, said the company has long worked to adopt digital tools, starting with major aircraft programs and moving into other areas. In developing the Enhanced Polar System Control and Planning Segment a decade ago, the company found digital engineering enabled it to find and correct defects far earlier, saving time and money.
“We have taken what we learned from EPS CAPS and other early adopter programs and scaled those digital engineering capabilities in order to apply them to [the Ground Based Strategic Deterrent], our Protected Tactical SATCOM, Evolved Strategic SATCOM and Next-Gen OPIR programs,” Erikson said.
Finding flaws
During a tour of Lockheed Martin’s facilities outside of Denver, Colorado, company officials showed off tools used to bolster digital efforts. Within Lockheed’s so-called Accelerator Environment — a small, open-floor room effectively serving as a 24/7 playground for engineers and interns to test new ideas — the company is exploring ways to broaden its digital practices. Among the technologies under exploration are new virtual reality systems that let users interact with digital models in a 3D space, and smart tools that can upload manufacturing data to the cloud.
By going through the motions of assembly in virtual reality, engineers can identify potential problems and address them before manufacturing begins. In an example demonstrated in the Pulsar Accelerator, users took control of an internal panel, bringing it inside a space vehicle to see whether it could fit into a tight space. In this instance, technicians discovered fasteners on a panel didn’t fit the rest of a design, said Darin Bolthouse, senior manager of the Collaborative Human Immersive Lab at Lockheed Martin Space.
“It would have been something they would not have found [before assembly],” he said.
The company can convert any of its digital models for testing in the virtual reality environment. A small or medium model can be converted in 10 minutes, said Bolthouse, although larger, more complicated designs can take longer.
Lockheed engineers are also exploring how to integrate smart tools with digital models.
Take torquing, for example. When building a satellite, technicians go from fastener to fastener, torquing each to specification with a wrench and recording the measurement by pen and paper. Then a second technician double checks the torques. It’s the definition of a nondigital process.
With the new smart torque tool, the process is partially automated and digitized. A green light on the smart tool signifies the torque — or the applied force — is within specifications, and the measurement is uploaded to the cloud without the need to double check.
Lockheed wants to eventually be able to directly insert those torquing measurements into a digital model so engineers can see how the system is built in real time. And artificial intelligence tools would look through the torque data to identify anomalies and test how products hold up.
The first steps into the Matrix
Space Force officials say the nascent service is making headway on implementing its digital agenda.
“Those data standards are being developed. The platform is being developed. The hardware stack is being developed so we can all communicate on a common framework,” Space Systems Command chief Gen. Mike Guetlein said at the Space Symposium in Colorado Springs. “And now we’re starting to talk about: What does that digital platform look like that’s going to drive us all going forward?”
One of the key pieces will be the new, cloud-based “Digital Engineering Environment,” in which vendors can share digital twins with the Space Force and other industry partners. Space Force officials said the classified version was coming online at the time of their announcement in May, while an unclassified environment was expected to be ready in early fall.
The service’s digital priorities are already reflected in its major satellite contracts. Shortly after the May announcement, the Space and Missile Systems Center (since redesignated as Space Systems Command) awarded contracts to two companies — Raytheon Technologies and Millennium Space Systems — to design digital models of missile warning satellites to be tested in high-fidelity simulations. Those tests will show if the service can improve its missile warning architecture by placing the satellites in a new orbital regime.
But challenges remain. Contractors point to the need for universal standards and more granularity for the digital models to help unlock the full potential of digital engineering. But they also say the private sector will resolve those issues if the Space Force continues to incentivize the adoption of digital engineering in its contracting.
“I think it works itself out as long as Space Force is still continuing to push the agenda,” Ray said. “I think Space Force is paving the way for the entire DoD.”
Quelle: C4ISRNet