4.12.2019
Starliner test flight slips two days
WASHINGTON — Boeing announced Dec. 3 that it’s delaying the uncrewed test flight of the company’s CST-100 Starliner commercial crew vehicle by two days because of a minor launch vehicle issue.
In an on-stage interview during a U.S. Chamber of Commerce commercial space conference here, Jim Chilton, senior vice president of the space and launch division of Boeing Defense, Space and Security, said Boeing had just received range approval to slip the Orbital Flight Test (OFT) launch two days to Dec. 19 at 6:59 a.m. Eastern.
“We had something come up over the weekend on purge ducting,” Chilton said, adding it was “a little off” and that the company decided to take the time to correct the problem and delay the launch.
United Launch Alliance, which provides the Atlas 5 rocket that will launch the Starliner, said in a later statement it involved an air supply duct. “Additional time was needed for the ULA and Boeing teams to complete an analysis of the issue, replace the duct and complete processing ahead of launch,” ULA stated. An industry source said the duct in particular was for the cavity in the launch vehicle adapter between the bottom of the Starliner and the top of the rocket’s Centaur upper stage.
The Orbital Flight Test is an uncrewed test flight of the vehicle, similar to the Demo-1 mission conducted by SpaceX’s Crew Dragon spacecraft in March. The flight will test the vehicle’s capabilities, including docking with the International Space Station, over the course of about a week. The spacecraft will then land, with White Sands Missile Range in New Mexico the primary landing site.
That mission will be followed by a crewed test flight, with NASA astronauts Michael Fincke and Nicole Mann as well as Boeing astronaut Chris Ferguson on board. NASA has not set a date for that launch, but it is not expected before spring 2020.
Quelle: SN
+++
Launch of first Starliner orbital test flight slips to Dec. 19
The first launch of Boeing’s Starliner space capsule aboard a United Launch Alliance Atlas 5 rocket has been delayed to Dec. 19, officials announced Tuesday.
The liftoff of the Starliner’s Orbital Flight Test on top of was previously scheduled for Dec. 17 on a week-long demonstration mission to the International Space Station. The mission is a critical precursor for the Starliner’s first flight with astronauts, a milestone Boeing officials say is scheduled for mid-2020.
“During pre-launch processing of the Atlas 5, there was an issue with the rocket’s purge air supply duct,” ULA said in a statement Tuesday. “Additional time was needed for the ULA and Boeing teams to complete an analysis of the issue, replace the duct and complete processing ahead of launch.”
The purge air supply duct is a new feature on the Atlas 5 rocket inside the launch vehicle adapter cavity, according to ULA. The adapter structure connects the Atlas 5 rocket with the Starliner spacecraft.
The duct is a tube that carries air from the ground environmental control system into the launch vehicle adapter cavity for pre-launch cooling of avionics and the Starliner service module, ULA said.
Liftoff time Dec. 19 is scheduled for roughly 6:59 a.m. EDT (1159 GMT), approximately 10 minutes before sunrise. The exact launch time will be determined closer to launch day based on the latest tracking of the space station’s orbit.
“We continue to work closely with Boeing to ensure that the Starliner flies as soon as the spacecraft and launch vehicle are ready,” ULA said.
Boeing is developing the Starliner crew capsule under a $4.2 billion contract awarded by NASA in 2014. NASA has tapped Boeing and SpaceX to develop new human-rated spaceships to end U.S. reliance on Russian Soyuz crew ferry ships to transport astronauts to and from the space station.

ULA has assembled the Atlas 5 rocket over the last month inside the Vertical Integration Facility just south of pad 41. Technicians first stacked the Atlas first stage on its mobile launch platform inside the VIF, then added two strap-on solid rocket boosters Nov. 6 and Nov. 7. The Atlas 5’s dual-engine Centaur upper stage was hoisted atop the rocket Nov. 8, followed by a sequence of checkouts on the launcher before Boeing’s Starliner crew capsule arrived for installation on the launch vehicle Nov. 21.
The Atlas 5 will ride its mobile launch platform for the 1,800-foot journey to pad 41 Wednesday, where ULA has built a crew access tower and white room to allow astronauts to board the Starliner through its side hatch.
Two trackmobile railcars will power the journey on rails from the VIF to the launch mount at pad 41.
ULA, Boeing and NASA teams are gearing up for the Integrated Day-of-Launch Test, or IDOLT, exercise to practice launch day procedures ahead of the Starliner’s first space mission.
The Atlas 5 launch team has lengthened the countdown for Starliner missions to more than 11 hours from its standard duration of early seven hours. The extra time allows a “blue team” of specialists — analogous to the space shuttle-era closeout crew — to assist astronauts in boarding the Starliner spacecraft after the Atlas 5 is fueled with cryogenic propellants.
The test “will give us the opportunity to deploy the crew access arm and verify all the access tower and arm interfaces with the spacecraft,” said Caleb Weiss, ULA’s mission manager for the Starliner program. “We will fully tank the vehicle, and we will have people out there at the pad that will be simulating day launch operations, just like they will be for a real launch day.
“So they will be in the white room, they’ll open up the hatch of the Starliner,” Weiss said in an earlier interview with Spaceflight Now. “They will practice going in and out, loading cargo, configuring Starliner for flight. So it’ll be a really good end-to-end system checkout of all the launch vehicle and spacecraft systems working together, as well as the people who are executing the operations.”
Once the IDOLT exercise is complete, the rocket will return to the VIF for additional testing and preparation activities ahead of liftoff later this month.
Quelle: SN
----
Update: 7.12.2019
.
NASA Engineers Break SLS Test Tank on Purpose to Test Extreme Limits
Engineers at NASA’s Marshall Space Flight Center in Huntsville, Alabama, on Dec. 5 deliberately pushed the world’s largest rocket fuel tank beyond its design limits to really understand its breaking point. The test version of the Space Launch System rocket’s liquid hydrogen tank withstood more than 260% of expected flight loads over five hours before engineers detected a buckling point, which then ruptured. Engineers concluded the test at approximately 11 p.m.
“We purposely took this tank to its extreme limits and broke it because pushing systems to the point of failure gives us additional data to help us build rockets intelligently,” said Neil Otte, chief engineer of the SLS Stages Office at Marshall. “We will be flying the Space Launch System for decades to come, and breaking the propellant tank today will help us safely and efficiently evolve the SLS rocket as our desired missions evolve.”
The test version of the tank aced earlier tests, withstanding forces expected at engine thrust levels planned for Artemis lunar missions, showing no signs of cracks, buckling or breaking. The test on Dec. 5 -- conducted using a combination of gaseous nitrogen for pressurization and hydraulics for loads -- pushed the tank to the limits by exposing it to higher forces that caused it to break as engineers predicted. Earlier tests at Marshall certified the tank for both the current version of the SLS -- called Block 1, which will use an upper stage called the Interim Cryogenic Propulsion Stage -- and the Block 1B version that will replace the ICPS with the more powerful Exploration Upper Stage.
“This final tank test marks the largest-ever controlled test-to-failure of a NASA rocket stage pressurized tank,” said Mike Nichols, Marshall’s lead test engineer for the tank. This data will benefit all aerospace companies designing rocket tanks.”
For all the tests, NASA and Boeing engineers simulated liftoff and flight stresses on a test version of the Space Launch System liquid hydrogen tank that is structurally identical to the flight tank. Throughout the tests in Marshall’s 215-foot-tall test stand, they used large hydraulic pistons to deliver millions of pounds of punishing compression, tension and bending forces on the robust test tank.
The test tank was fitted with thousands of sensors to measure stress, pressure and temperature, while high-speed cameras and microphones captured every moment to identify buckling or cracking in the cylindrical tank wall.
“The initial tank buckling failure occurred at the same relative location as predicted by the Boeing analysis team and initiated within 3% of the predicted failure load,” said Luke Denney, qualification test manager for Boeing’s Test & Evaluation Group. “The accuracy of these predictions against real life testing validates our structural models and provides high confidence in the tank design.”
Teams at Michoud are wrapping up functional testing of the assembled SLS core stage for the Artemis I mission and already are building the core stage for the Artemis II mission. The 212-foot-tall core stage is the largest, most complex rocket stage NASA has built since the Saturn V stages that powered the Apollo missions to the Moon.
“We are happy that NASA’s tests with the core stage structural test article will contribute not only to Space Launch System flights but also to the design of future rocket propellant tanks,” said Julie Bassler, manager of the SLS Stages Office.
SLS is the only rocket that can send Orion, astronauts and supplies to the Moon on a single mission. SLS, Orion and the Gateway in orbit around the Moon, are NASA’s backbone for deep space exploration and the Artemis program, which will send the first woman and next man to the lunar surface by 2024.
NASA and Boeing look ahead to long-term SLS production
NEW ORLEANS — As NASA marked the completion of the core stage of the first Space Launch System rocket, the agency and the rocket’s prime contractor are in the midst of negotiations for a long-term production contract for additional vehicles.
NASA announced in October that it was starting negotiations with Boeing for a production contract that would cover up to 10 core stages for the SLS, starting with the third SLS rocket. Boeing is already under contract for the first two SLS vehicles and NASA has authorized initial funding for the third SLS in order for it to be ready in time for a human lunar landing mission in 2024.
NASA expects that, with a long-term contract in place, it will be able to bring down the costs of individual SLS vehicles. “If you buy one SLS rocket, the price is really high. If you buy two, the price goes down significantly, and if you buy the three it keeps going down,” NASA Administrator Jim Bridenstine said at a Dec. 9 event at the Michoud Assembly Facility here.
Bridenstine said at the event that the agency was seeking such economies of scale in any contract for future SLS vehicles, depending on how many the agency needed for its future exploration plans. “We need to look at the price based on a negotiation between NASA and our prime contractor,” he said, a reference to Boeing. “That negotiation, and how many we buy, ultimately will determine what that final cost will be per rocket.”
Bridenstine didn’t state a price target for the SLS under any new contract, although at a NASA town hall meeting Dec. 3 he estimated the per-vehicle cost to eventually reach $800–900 million. In an interview with CNN Dec. 9, he estimated a single SLS today costs $1.6 billion, but could get down $800 million under a long-term production contract.
Those contract negotiations are going well, according to a Boeing official. “I personally don’t think we’re that far apart,” Jim Chilton, senior vice president for space and launch at Boeing Defense, Space and Security, said in a Dec. 9 interview. “It’s actually going pretty fast.” The scope of that long-term contract, he said, would likely cover 10 vehicles, although initial funding would be for just the third and fourth SLS vehicles.
Another factor will be how quickly those vehicles will be produced. Some in Congress have sought to increase the SLS production rate to two vehicles a year as soon as 2024. That would enable another SLS to be available to support human lunar missions: Boeing, for example, has proposed developing a lunar lander that would be launched as a single vehicle on an SLS, rather than in modules launches on commercial rockets. Congress has also required that NASA use an SLS to launch its Europa Clipper mission.
Chilton said that, while Michoud was not designed for high production rates, he didn’t see many problems in going to two SLS vehicles a year. Despite the long delays in the production of the first SLS core stage, he said the company could produce future SLS core stages at a rate of one every eight months. “So we’re not that far off it,” he said of a two-per-year production rate.
While Chilton said he thought that Boeing could produce two SLS vehicles a year by 2024, Bridenstine was not nearly as optimistic. “Nobody has presented me a plan that says that that’s happening, but certainly I would fully support it if they could make it happen,” he told reporters at the event. “I’m not counting on that for 2024, quite frankly.”
“For 2024 we need to be focused on getting that Artemis 3 SLS complete, and using other rockets to do payload deliveries and that kind of thing apart from the SLS itself,” Bridenstine added. NASA’s current architecture calls on using commercial rockets for delivery of lunar Gateway elements and modules for the lunar lander, with SLS reserved for the launch of the crewed Orion spacecraft.
Another issue will be the transition from the original Block 1 version of the SLS, which uses the Interim Cryogenic Propulsion Stage as its upper stage, to the Block 1B with the more powerful Exploration Upper Stage. NASA’s current plans call for using the Block 1 SLS for the first three missions, then moving to the Block 1B, although some have called for a faster transition.
“Starting in 2024, the Exploration Upper Stage (EUS) will power NASA missions that carry crew and heavy cargo deeper into space,” Boeing said in a Dec. 9 statement about development of the stage. “NASA expects to fly the EUS on the Artemis 3 mission to deliver combined payloads, such as large elements of the Gateway lunar orbiter or an integrated Human Lander System, along with Orion.” A NASA statement in October said use of the EUS would begin with the Artemis 4 mission.
Chilton said that work on EUS, which was paused for a time, is proceeding, with the stage now between its preliminary and critical design reviews. The EUS, like the core stage, will be produced at Michoud. “Our target is ’24,” he said of having the EUS ready. “The Artemis 3, 4 time frame.”
Quelle: SN
----
Update: 16.12.2019
.
Boeing, NASA getting ready for SLS Core Stage Green Run campaign ahead of Stennis arrival
As NASA showed off the first assembled Space Launch System (SLS) Core Stage to government stakeholders and media at the Michoud Assembly Facility (MAF) in New Orleans, prime contractor Boeing continued preparations to ship the stage to the Stennis Space Center in Mississippi as soon as they can. While the TV camera “red lights” were on during a live morning broadcast on December 9 at the beginning of “Artemis Day” event festivities held at MAF, similar “test in progress” lights were on around the stage as Boeing and RS-25 prime contractor Aerojet Rocketdyne continued working to complete engine leak checks.
In parallel, NASA and contractor teams at Stennis are wrapping up work at the B Test Stand there so the Core Stage can be installed in the B-2 stage test position there next month. Boeing is now estimating that the Stage “Green Run” test campaign will last up to ten months before the stage will be ready to ship to Kennedy Space Center (KSC) in Florida for final preparations for a 2021 Artemis 1 launch.
The centerpiece of the test campaign is an eight-minute long, flight duration “hot-fire” of the stage in the B-2 stand, which could take place in the middle of the year; however, the extent of repairs and refurbishment of the stage after the first-time firing is an unknown and test managers are bookkeeping two to three months to restore the stage to a safe enough condition to travel to KSC.
At MAF functional testing to verify that the systems of Core Stage-1 are connected and communicating with each other correctly is still in progress, and the tentative date for shipment to Stennis is now just after New Year’s. Once testing is complete, final outfitting of the stage must be completed where it is currently lying in the SLS Final Assembly area, and then it will be moved for loading onto NASA transporters to roll out to the barge and head to Stennis.
Stage shipping preps in parallel with completing functional testing
NASA and Administrator Jim Bridenstine celebrated the completion of the first Core Stage at Michoud on December 9 and while all the working pieces are connected, prime contractor Boeing continues running through a final integrated functional test (FIFT) of the stage.
“We’re in functional testing, so we’ve connected all the major pieces of the rocket, we’re making sure they all talk to each other,” Amanda Gertjejansen, Core Stage-1 Operations Manager for Boeing, said in an interview on December 9. “Once we’re done with functional test we’ve got to prep the vehicle to ship.”
As seen during the media event on December 9, the stage is lying horizontally in the Area 47 footprint of the Area 47/48 duplex in Building 103, where Core Stage Final Assembly takes place. With functional testing still underway, the stage is still missing several flight covers and remains surrounded by work stands.
“The purpose of the Green Run is to satisfy design objectives, so we’ve got really, really good models that are predicting how the vehicle is going to react once we load it with liquid oxygen, liquid hydrogen, and we do the hot-fire,” Nappi explained. “The Green Run is to verify that yeah those models were right, and you only need to do that once and then you can depend on your models for any changes that occur.”
The models also allow engineers to analyze how the stage would behave under a larger set of operating conditions, including outside the currently defined limits. Previously, NASA and Boeing had also planned on conducting an acceptance test of the second Core Stage; however, in the name of schedule the necessity of both months-long Green Run campaigns came into question.
“It’s about ten months to get it all done and if we have a little bit of luck we could get it done a little sooner than that,” Nappi said. If the stage arrives at Stennis in early January, that would put arrival at KSC in the October time-frame next year, implying that the Artemis 1 launch date target would be well into 2021.
A final decision in the summer was to perform the Green Run campaign once on the first flight unit; plans to do the same for the second unit were canceled.
Nappi provided an overview of the Green Run activities at Stennis: “What’s involved once the vehicle gets here is getting it in the stand and this is really a joint effort between Stennis and the NASA Marshall Stages Office and us as a contractor, Boeing, to get that vehicle in position where we can hot-fire it,” he said. “So as soon as we get it in the stand we’ll take about two or three weeks where we’re going to do something called a modal, which is essentially just a response test to see how the vehicle reacts, again matching up those results with the models that we’ve created to make sure that it’s reacting like we expected it to.”
As was practiced at Stennis with the Core Stage Pathfinder, the flight stage will be rolled off of the Pegasus barge that moves it from MAF to Stennis, lifted up with two cranes, rotated from horizontal to vertical, and then the primary test stand derrick crane will install the stage in the stand where it will be bolted down and the crane disconnected.
“From the time the barge gets here it takes about three, four days and then it’ll be in the stand,” Nappi noted.
Photo Caption: The B Test Stand derrick crane lifts the Core Stage Pathfinder out of the stand’s B-2 position on August 29. After installing Core Stage-1 into the stand in January, the crane will be used to lift the stage up out of the hold-down attachments to perform three separate modal test runs over a period of a couple of weeks. The modal tests are the first of many test cases to be run as a part of the Stage Green Run campaign.)
The modal test measuring the structural frequency response of the Core Stage by itself is three separate test runs where the derrick crane is reattached and the stage is partially lifted out of the stand so it is hanging on the crane to perform the test. “We lift it three times, so we take it, lift it up, do the modal test, put it back in the stand. Do some data analysis, come back again pick it up, do modal, put it back in the stand. Same thing, three times.”
“Once we’re done with modal then we’ll bolt the vehicle down in the stand and we’ll start getting access,” Nappi explained. “We’ve got to get access into the engine section, we have to get access into the intertank, we have to get access into the forward skirt so that we can start configuring the vehicle for test.”
“We also have some work that we’re going to complete from MAF, the LH2 (liquid hydrogen) feedlines still need to be connected so we’re going to have about two or three months worth of work to get those feedlines connected so that when we start our power on testing we’ll have the vehicle in flight configuration.”
The LH2 feedlines and fill and drain line are positioned inside the engine compartment, but can’t be secured while the stage is horizontal. Boeing, with NASA’s concurrence, traded deferring that work to Stennis in order to buy back several months of time at MAF by completing the rest of the stage assembly in the horizontal.
After the LH2 Main Propulsion System (MPS) lines are secured, checked out, and final spray-on foam insulation (SOFI) closeout work completed, the power-up testing will start to verify that the stage is ready to be loaded with propellant and then fired; the cryogenic tanking and test-firing will be firsts for the SLS Program.
“We’ll do what we call power-up testing or confidence testing,” Nappi explained. “This is the first time that this vehicle has been in this stand and has seen the software that we’ve created to run these tests, so we want to take a really slow and methodical set of steps to make sure that that all works together properly so that when we do go do the ‘wet dress’ (Wet Dress Rehearsal) and the hot-fire everything is working like it’s supposed to.”
Special software will run on the stage’s three redundant flight computers to account for the static nature of the eight-minute long test; otherwise, most of the stage’s systems have to perform as they would during a dynamic ascent to orbit insertion. Boeing has also developed the Core Stage Controller (also known as the Stage Controller) package of ground software and avionics that manages that side of the Stennis testing.
“The tests are validating that all of our systems are working, that our avionics systems are working, our hydraulic systems are working, TVC systems are working, our Main Propulsion Systems are all working. We’ll have people in our control room that will be monitoring all their systems as we bring every single black box up and we actuate every valve and we’re checking to make sure that when we send the command that it works and the indications come back and they’re coming back like they’re supposed to.”
“So we’re going to take a couple of months testing everything with the software and the vehicle and the stand to make sure that it works right,” he added. “When we’re done with that we’re going to take a step back and say it’s time to load this vehicle with LH2 and LOX (liquid oxygen) and see how it reacts.”
Photo Caption: A view of the northern perimeter of the B Test Complex from Level 19 of the B-2 test stand position in December, 2018. The white-colored tubing to the right of the exhaust/water deluge pathway that extends out from the flame buckets of both B-1 (left) and B-2 (right) positions is where LOX will be dumped after it is drained from the Core Stage after the Wet Dress Rehearsal. Any LOX residuals left in the tank following the hot-fire test will also be dumped here. Gaseous oxygen boiloff will be vented out a port on the stage’s forward skirt.)
“We’re going to do what’s called a Wet Dress Rehearsal (WDR), load it with LH2 and LOX, make sure it doesn’t leak, we’re good. We detank it, these guys get us some more commodities so we can load that vehicle again and [then] we come back and we actually run the hot-fire.”
Boeing anticipates a short turnaround from the WDR to the hot-fire; what amounts to a scrub turnaround between the WDR tanking and the hot-fire tanking is driven by the infrastructure at Stennis to supply propellant and other support commodities to the fluid-hungry stage. The cryogenic propellants are supplied to the hydrogen-oxygen test stands at Stennis by barges docked around them.
“Our liquid oxygen barges here, each one of those holds about a hundred thousand gallons of liquid oxygen,” Maury Vander, NASA’s Test Operations Division Chief in the Stennis Engineering and Test Directorate, said. “Those [liquid hydrogen barges] are about two-hundred, forty thousand gallons of liquid hydrogen.”
“The vehicle holds five-hundred fifty thousand gallons of LH and about two-hundred thousand gallons of liquid oxygen so we’ve got enough, but we don’t have enough to try to recycle quickly. We’re making the conscious decision after the wet dress we’re going to discard the LOX and we’re going to drain back the liquid hydrogen so we’ve got to get trucks in here to replenish our barges and that’s what drives the five-day turnaround between wet dress to hot-fire.”
“When we do the wet dress, we’re just basically testing the health of the overall system,” Nappi noted. “Are we getting any leaks? Are the valves working properly? Is it a nominal type of tanking?”
“And detanking — it’s real important to assure that we can detank this vehicle as safely as we tanked that, so those are two real important parts of the test. Then when we do hot-fire you’re essentially just checking your flight readiness of all the main propulsion system and that it’s working properly and we’ll be watching it just like we would on day of launch.”
Following the hot-fire, Boeing has set aside a long period for refurbishing the stage. “It takes about two to three months after hot-fire,” Nappi said. “We haven’t hot-fired it yet so when we’re done we’ll take a step back, we’ll see what needs to be fixed before we put it on the barge.”
“First of all we have to do shipping preps, we have to get the vehicle ready to put on the barge. That’s all known work, we know what kind of preparations need to be made.”
“The second piece is the engine refurb, and the third piece is any damage that occurs during hot-fire,” he added. “This thing is going to fire for eight minutes and it’s going to be bolted down.”
“We expect to see some TPS damage and so we’re going to have to repair that, but we don’t have to repair it all here. We can take a lot of that to KSC if we like and do it on a non-interference basis at KSC.”
“So that work is undefined, we don’t know what the damage is going to be yet,” Nappi explained. “We suspect we know where some of it is going to be and we’re preparing for it, but until we know what it is we won’t be able to scope it.”
Aerojet Rocketdyne will refurbish the RS-25s while Boeing works on the rest of the stage. “They’ve come up with a minimal number of days that they need to essentially get the engines refurbished to a point where they’re safe enough to put it on the barge,” Nappi said. “After hot-fire it’s about two months.”
“We’re going to have a lot of instrumentation on the vehicle for this test so that instrumentation has to come off. That’s again known work, we will be able to do that under the envelope of the engines being refurbished,” he added.
There is also ground test instrumentation specific to the modal tests that will be conducted at the beginning of the campaign; Nappi said that instrumentation would be removed immediately after the modal tests are completed.
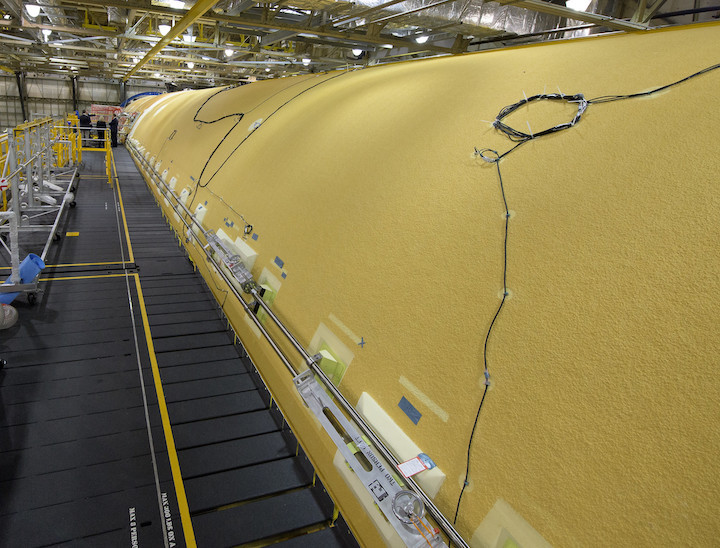
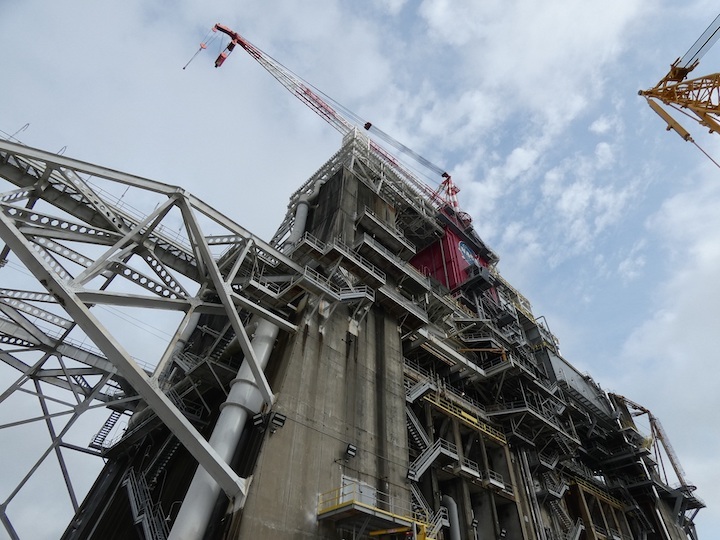
How big is NASA’s Space Launch System? Check these new images
NASA has been telling us how big the Space Launch System (SLS) rocket will be when finally assembled on the launch pad. “It’s the biggest rocket the agency has built since the Apollo V moon rocket,” the space agency says frequently.
New pictures taken over the holidays give the clearest understanding of just how large that is. NASA recently completed assembling the SLS core stage including its four space shuttle main engines and the liquid hydrogen and oxygen tanks that will feed them.
It has just rolled the core from the assembly building at the Michoud Assembly Facility near New Orleans to another facility to be prepped for water travel. The 212-foot-long core that also includes the rocket’s avionics (electronics) will travel from Michoud via barge to NASA’s nearby Stennis Space Center in Mississippi for live engine testing later this year.
When fully assembled with the upper stage including the Orion capsule and European Service Module, SLS will be 322 feet tall - taller than the Statue of Liberty - but still shorter than Apollo by nearly 60 feet. It is more powerful, however, with 8.5 million pounds of thrust compared to the moon rocket’s 7.5 million pounds.
SLS isn’t the only big rocket under development in America today. SpaceX has a 348-foot tall rocket called Starship under development, and Blue Origin is working on its New Glenn rocket that will be somewhere between 269 and 311 feet tall. All of these rockets are being designed to lift heavy payloads into orbit or journeying to Mars.
SLS development is led by NASA’s Marshall Space Flight Center in Huntsville, Ala., which also built the rocket’s avionics. Its main contractor is Boeing, which also has a large rocket workforce in the city. NASA expects to finish live engine testing this year and then ship the core to Florida’s Kennedy Space Center for vertical mating to the Orion capsule and service module. SLS will likely launch without a crew in 2021 for its first trip around the Moon.
As all that is happening, NASA and Boeing will be assembling two more SLS rockets. The second will fly astronauts around the Moon on a test flight, and the third will take America’s first woman and next man to the Moon for a landing. President Trump has ordered NASA to make that landing by 2024.
Quelle: AL
----
Update: 10.01.2020
.